датчик приближения Бернштейна
- time:2025-07-11 03:52:16
- Нажмите:0
Bernstein Proximity Sensors: The Unseen Guardians of Industrial Automation
Imagine a high-speed bottling line humming along flawlessly, millions of pills precisely counted per minute, or robotic arms assembling complex machinery with micron-level accuracy. Behind these feats of modern manufacturing lies an often-unseen hero: the датчик приближения. And when reliability in the toughest industrial environments is non-negotiable, Bernstein proximity sensors consistently earn their place at the forefront. These precision workhorses provide the crucial non-contact detection that keeps processes running smoothly, safely, and efficiently.
Demystifying the Proximity Sensor
At its core, a proximity sensor detects the presence or absence of an object within its sensing range without physical contact. This eliminates mechanical wear, reduces maintenance needs, and allows for incredibly fast response times. Among the various types (inductive, capacitive, magnetic), inductive proximity sensors are the undisputed champions for detecting metallic objects in demanding industrial settings. This is precisely where Bernstein excels.
How Bernstein Inductive Proximity Sensors Work: Simplicity Meets Robustness
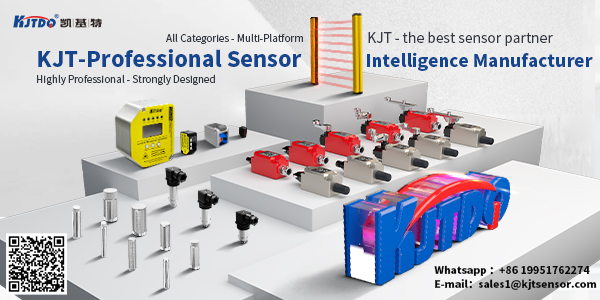
Bernstein inductive proximity sensors operate on a simple yet highly effective electromagnetic principle:
- Generating the Field: A high-frequency oscillator within the sensor generates an alternating electromagnetic field emanating from its active face.
- Disturbance Detection: When a metallic object (target) enters this field, eddy currents are induced on the target’s surface.
- Amplitude Shift: These eddy currents draw energy from the oscillator circuit, causing a measurable decrease in the oscillation amplitude.
- Signal Trigger: An integrated evaluation circuit continuously monitors this amplitude. Once the drop exceeds a preset threshold (indicating the target is within the specified sensing range), the sensor triggers a switching signal – its output state changes (e.g., from OFF to ON).
- Output: This change is communicated instantly via the sensor’s electrical output (NPN or PNP transistor), signaling the presence of the object to the control system (PLC, robot controller, etc.).
The elegance lies in the complete lack of physical interaction. Bernstein designs these sensors to perform this sequence reliably millions of times under harsh conditions like vibration, temperature extremes, dust, oil, and coolant spray.
Why Bernstein Stands Out: Key Attributes and Advantages
Choosing Bernstein proximity sensors means investing in performance and longevity. Here’s what sets them apart:
- Unmatched Robustness & Durability: Built for the harshest industrial realities. Bernstein sensors typically feature stainless steel housings (V2A or V4A/316L), nickel-plated brass, or rugged engineered plastics. They boast exceptional resistance to shock, vibration, and chemicals commonly found on factory floors.
- High Ingress Protection (IP Ratings): Critical for reliability in dirty or wet environments. Bernstein sensors frequently achieve IP67, IP68, and even IP69K ratings, meaning they are protected against powerful water jets, temporary immersion, and dust ingress. This makes them ideal for applications in food & beverage processing, automotive washdowns, or foundries.
- Temperature Resilience: Engineered to operate reliably across wide temperature ranges, often from -25°C to +70°C or even wider, ensuring consistent performance in refrigerated environments or near heat sources.
- Precision Sensing & Repeatability: Offering short-, standard-, and long-range detection capabilities with high repeat accuracy. This precision ensures consistent triggering, vital for positioning, counting, and quality control tasks.
- Electrical Versatility: Available with both NPN (sourcing) and PNP (sourcing) output configurations (NO/NC), plus AC/DC variants, offering maximum compatibility with diverse control systems worldwide. Models with analog outputs (e.g., 4-20mA, 0-10V) are also available for continuous distance measurement.
- Design Optimizations: Bernstein provides numerous form factors (barrel M8, M12, M18, M30; rectangular block; flat-pack), shielding options (flush mountable for detection in metal surroundings or non-flush for longer ranges), and connection types (cable, connector M8/M12). Their popular BES series exemplifies this versatility.
- Enhanced Functionality: Beyond basic detection, many Bernstein sensors offer features like operating state indicators (LEDs), short-circuit and overload protection, reverse polarity protection, and resistance to magnetic fields – crucial near welding equipment or motors.
Where Bernstein Proximity Sensors Prove Indispensable
Their robustness and reliability make them critical components across countless sectors:
- Factory Automation: Position sensing in actuators, cylinders, robots; end-of-travel detection; presence verification of parts on conveyors, pallets, or fixtures; machine guarding perimeter checks.
- Automotive Manufacturing: Monitoring robotic welding arms; detecting vehicle bodies on assembly lines; verifying component insertion; sensing piston or gear position in powertrain assembly.
- Packaging Machinery: Bottle/cap detection; fill level control (using capacitive variants); label presence verification; box counting and diverting.
- Перевозка материалов: Monitoring conveyor belt movement; detecting pallet position in AS/RS (Automated Storage/Retrieval Systems); object counting on sorting lines.
- Food & Beverage: Ensuring container presence for filling and capping; detecting metal objects (product safety); monitoring valve positions – demanding high IP ratings for washdown.
- Machine Tools & CNC: Tool changer position verification; workpiece clamping detection; door interlocking for safety; coolant level monitoring (capacitive).
Selecting and Implementing Bernstein Sensors Effectively
Maximizing the performance of your Bernstein proximity sensors involves careful consideration:
- Target Material: Inductive sensors are optimized for ferrous metals (iron, steel). Detection range for non-ferrous metals (aluminum, brass, copper) is typically reduced (often 50-60% less). Confirm material compatibility. For non-metallic objects, consider Bernstein capacitive sensors.
- Required Sensing Range (Sn): Choose a sensor with a range (Sensing range - Sn) slightly exceeding your application’s actual gap. Factor in target size and material. Bernstein provides detailed datasheets specifying Sn for different target types and sizes (e.g., standard Fe360 target).
- Mounting Constraints: Will the sensor be mounted flush or non-flush? Is the surrounding mounting material metallic? Flush-mountable sensors are essential when installed in metal to avoid incorrect triggering from the mount itself.
- Environmental Conditions: Is the sensor exposed to dust, water, oil, chemicals, extreme temperatures, or welding fields? Select the housing material (stainless steel highly recommended for harsh conditions) and IP rating accordingly. IP67/IP68/IP69K is essential for washdown environments. Look for high temperature ratings.
- Electrical Requirements: Match the sensor’s **operating voltage