katlax proximity sensor
- time:2025-07-11 03:17:01
- Нажмите:0
KATLAX Proximity Sensors: The Unseen Guardians of Modern Automation
Imagine a complex assembly line humming with robotic arms, moving with uncanny precision. Or picture heavy machinery on a factory floor, operating seamlessly within tight confines. Now, consider the critical element ensuring these automated systems function safely and efficiently: the ability to detect objects without physical contact. This is where Katlax Proximity Sensors step in, acting as the silent, reliable sentinels of countless industrial applications. Understanding their capabilities and benefits is crucial for optimizing automation processes, enhancing safety, and minimizing costly downtime.
The Fundamental Shift: Contactless Detection
Traditional mechanical switches rely on physical touch to detect an object’s presence. While functional, they suffer from wear and tear, limited speed, and vulnerability to harsh environments. Proximity sensors represent a paradigm shift. They operate on the principle of generating an electromagnetic field and detecting changes caused by the approach of a conductive or magnetic target without any physical interaction. This non-contact nature is their defining strength, leading to significantly longer operational lifespans, higher reliability, and the ability to function at previously unattainable speeds. Their immunity to dirt, grease, and vibrations makes them indispensable in demanding industrial settings where mechanical switches would quickly fail.
What Makes Katlax Proximity Sensors Stand Out?
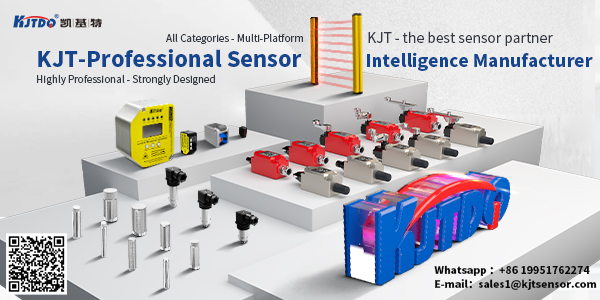
While the core principles of proximity sensing are well-established, the quality, robustness, and specific features offered differentiate manufacturers. Katlax has positioned itself as a provider of sensors known for several key attributes:
- Exceptional Sensing Range & Precision: Katlax designs sensors capable of detecting targets consistently within their specified ranges, offering reliable performance even under challenging conditions. Precise detection is paramount for applications like positioning, counting, or speed monitoring.
- Robust Construction & Environmental Resilience: Industrial environments are unforgiving. Katlax sensors are typically built with durable housings (often nickel-plated brass or stainless steel) offering high resistance to impact, shock, chemicals, oils, and coolant splashes. High IP ratings (Ingress Protection) are common, ensuring reliable operation despite dust and moisture ingress. This durability translates directly to reduced maintenance costs and enhanced process reliability.
- Stable Operation Across Temperatures: From freezing cold storage areas to sweltering foundries or paint shops, Katlax sensors are engineered to maintain consistent performance across a wide operational temperature range, ensuring stability where it matters most.
- Electromagnetic Compatibility (EMC): Modern factories are electrically noisy environments. Katlax sensors incorporate robust EMC protection, minimizing susceptibility to interference from variable frequency drives (VFDs), motors, welding equipment, and other sources of electrical noise, preventing false triggers and ensuring signal integrity.
- Versatility in Outputs & Configurations: Catering to diverse control system requirements, Katlax offers sensors with various output types:
- NPN (Sinking): Commonly used with PLCs (Programmable Logic Controllers) in many regions.
- PNP (Sourcing): Another prevalent standard for PLC integration.
- Analog Outputs: Providing a variable signal proportional to the distance to the target (e.g., 4-20mA, 0-10V).
- NO (Normally Open) / NC (Normally Closed): Standard switching logic options. This flexibility simplifies integration into existing control architectures.
- Shielded vs. Unshielded Options: Katlax provides choices depending on installation constraints. Shielded sensors offer flush mounting capability, ideal for tight spaces, though with a slightly reduced sensing range. Unshielded sensors provide a longer sensing range but require more clearance around the sensing face.
Where Katlax Proximity Sensors Excel: Key Applications
The unique combination of non-contact operation, ruggedness, and reliability makes Katlax proximity sensors ubiquitous across numerous sectors:
- Manufacturing & Assembly Lines: Detecting part presence/absence, counting products, verifying correct positioning, controlling robotic arm end positions, monitoring machine guards.
- Material Handling & Conveyor Systems: Verifying pallet/jig presence, detecting package jams, controlling sorting gates, confirming bin levels.
- Packaging Machinery: Monitoring fill levels (non-contact), detecting labels or caps, verifying case sealing.
- Автомобильная промышленность: Critical for robotic welding (positioning), paint shop automation, engine assembly verification, component testing.
- Machine Tooling: Tool breakage detection, spindle orientation, monitoring chuck positions, verifying workholding clamps.
- Food & Beverage Processing: Hygienic stainless-steel variants are vital for detecting containers, lids, or process stages within washdown environments.
- Textile Machinery: Detecting yarn breaks, monitoring spool rotations, controlling loom operations.
Selecting and Implementing Katlax Sensors Effectively
Choosing the right sensor for the job maximizes performance and longevity:
- Target Material: Proximity sensors primarily detect ferrous metals (steel, iron). Some models are optimized for non-ferrous metals (aluminum, copper) or specific materials. Confirm the sensor is suitable for your target. Katlax datasheets provide clear specifications.
- Required Sensing Distance: Be realistic. The rated operating distance (
Sn
) is for a standard target under ideal conditions. Choose a sensor with a range comfortably exceeding your minimum required distance, applying a derating factor (typically 0.5 to 0.8) to account for real-world variables like target size and temperature.
- Mounting Constraints: Consider available space. Will a shielded sensor fit? Does unshielded mounting provide sufficient clearance? Ensure the sensor body dimensions (cylindrical, block, etc.) suit the application.
- Environmental Factors: Critically assess temperature extremes, exposure to chemicals/oils/coolants, potential for physical impact, and dust/moisture levels (IP rating requirement). Katlax offers specific models for harsh conditions.
- Electrical Requirements: Match voltage supply requirements (commonly 10-30V DC) and output type (NPN, PNP, Analog) to your control system input card specifications.
- Installation Best Practices: Ensure proper alignment between sensor and target. Maintain recommended installation distances between multiple sensors to prevent mutual interference. Protect cables from abrasion and pinch points using conduits or cable carriers. Securely tighten mounting hardware to avoid vibration-induced loosening. Correct installation is paramount for reliable operation.
The Katlax Advantage: Driving Efficiency and Safety
In the intricate dance of modern automation, reliability and precision are non-negotiable. Katlax Proximity Sensors deliver precisely that. By providing accurate, non-contact detection in demanding environments, they form a critical foundation for:
- Enhanced Productivity: Minimizing false triggers and downtime caused by sensor failure.
- Improved Quality: Ensuring consistent part positioning and process verification.
- Reduced Maintenance Costs: Long lifespan and resistance to wear outlast mechanical alternatives.
- Increased Safety: Enabling safety interlocks on guards, confirming machine states, and preventing collisions.
Whether monitoring the precise position of a robotic welder, detecting a bottle cap on a high-speed filling line, or safeguarding personnel near moving machinery, Katlax Proximity Sensors operate tirelessly behind the scenes. Their unseen vigilance underpins the smooth, safe, and efficient operation of countless automated processes, proving that sometimes, the most critical components are those you never physically touch.