ИК - датчик регулируемого сближения
- time:2025-07-11 00:21:10
- Нажмите:0
Unlocking Flexibility: The Power of Adjustable IR Proximity Sensors
In the intricate dance of modern automation, robotics, and countless electronic devices, sensing proximity reliably is fundamental. Imagine a world where every sensor was rigid, fixed to a single detection range or sensitivity level. The result? Constant recalibration, hardware swaps for different tasks, and frustrating limitations. Enter the infrared adjustable proximity sensor – a game-changer designed for adaptability, offering engineers and designers unprecedented control over detection performance. This isn’t just about sensing presence; it’s about fine-tuning how that sensing happens to perfectly match the application’s unique demands.
Understanding the Core: Infrared Proximity Sensing
At its heart, an IR proximity sensor operates on a simple principle. It emits an invisible beam of infrared light. When an object enters its field of view, some of this emitted light reflects back towards the sensor. An internal photodetector receives this reflected signal. The sensor’s electronics then analyze the intensity of the returned light – generally, a closer or larger object reflects more light. Based on this intensity and pre-configured settings, the sensor triggers its output signal (often a simple ON/OFF switch) to indicate the object’s presence within the defined detection zone.
The Crucial “Adjustable” Factor: What Can You Tweak?
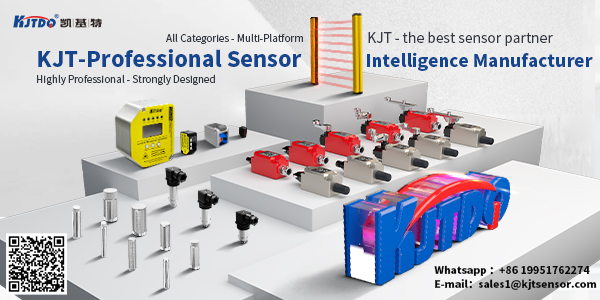
The standard IR proximity sensor gets the job done, but the adjustable variant elevates its utility significantly. This adjustability typically manifests in several key parameters:
- Detection Range: This is the most common and often critical adjustment. Instead of being locked into a fixed sensing distance (e.g., 10mm), an adjustable IR proximity sensor allows you to fine-tune the operational range. This might mean shortening the range to avoid false triggers from background objects or extending it slightly to reliably detect objects at a specific, slightly farther point. This flexibility is invaluable in applications where object positions vary or space constraints dictate specific sensing distances.
- Sensitivity: Closely related to range, sensitivity adjustment allows you to control how readily the sensor triggers based on the reflected signal strength. Increasing sensitivity makes the sensor react to weaker signals (potentially detecting smaller, less reflective, or more distant objects). Decreasing sensitivity makes it require a stronger reflection, helping to ignore background interference, dust, or ambient light that might cause false activations. Precise sensitivity calibration is vital for reliable operation in challenging environments.
- Hysteresis: Often overlooked but incredibly useful, hysteresis adjustment controls the difference between the “turn ON” point and the “turn OFF” point. Without hysteresis, a sensor holding an object exactly at its detection threshold might rapidly oscillate its output. Adding hysteresis creates a dead band, ensuring a stable output once triggered and preventing chatter. This is crucial for controlling machinery or processes that shouldn’t be rapidly cycled.
- Output Mode (Less Common, but Available): Some advanced models offer configurable output logic (e.g., Normally Open/NO, Normally Closed/NC) or output type (e.g., NPN, PNP transistor) via switches or configuration tools, enhancing integration flexibility.
Why Adjustability Wins: Solving Real-World Challenges
The ability to fine-tune these parameters transforms the IR adjustable proximity sensor from a simple component into a highly adaptable solution:
- Optimizing for Diverse Objects: Detect a glossy metal part in one application and a matte black plastic piece in another without changing hardware? Adjustable sensitivity and range make it possible.
- Combating Environmental Noise: Industrial settings often have stray IR sources, dust, or vibration. Reducing sensitivity or tweaking the range can “tune out” this interference, ensuring reliability.
- Perfect Positioning Tolerance: Manufacturing tolerances mean parts aren’t always in the exact same spot. An adjustable range provides a buffer zone for reliable detection despite minor positional variations.
- Preventing False Triggers: Avoiding unintended activation from reflective backgrounds, conveyor structures, or even accumulated dust is paramount. Precise calibration of sensitivity and hysteresis is key.
- Maximizing Sensor Lifespan: Using the minimal necessary detection range can sometimes reduce the sensor’s workload and potential interference, contributing to longevity.
- Simplifying Inventory & Design: One sensor model with adjustment capabilities can often replace several fixed-range variants, simplifying BOMs and design choices.
Where Adjustable IR Proximity Sensors Shine
The applications are vast, spanning numerous industries:
- Factory Automation: Object detection on conveyors, part presence verification in assembly machines, end-of-travel sensing on actuators, robotic arm positioning – all benefiting from customizable detection range.
- Consumer Electronics & Appliances: Water level sensing in appliances (tuning for different fluid reflectivity), automatic soap/towel dispensers, touchless faucets, presence detection in smart devices.
- Printing & Paper Handling: Detecting paper jams, monitoring media presence (requiring sensitivity adjustment for different paper types), controlling media feed paths.
- Security Systems: Intrusion detection (adjusting range to cover specific zones), automatic doors/gates, tamper detection requiring fine-tuned sensitivity.
- Packaging Machinery: Ensuring carton flaps are folded correctly, detecting product absence in trays, controlling fill levels.
- Robotics: Collision avoidance (short-range sensing), part pickup verification, gripper positioning feedback.
Choosing and Implementing with Intention
Selecting the right adjustable IR proximity sensor goes beyond just seeing the “adjustable” label:
- Define Your Core Needs: What is the minimum and maximum detection distance required? What are the typical object characteristics (size, color, material)? What are the environmental conditions (dust, moisture, temperature, ambient light)?
- Understand Adjustment Mechanisms: Are adjustments via potentiometers (easy, accessible), DIP switches, or software-configurable? Potentiometers offer simplicity but can be accidentally moved; software offers precision but requires interface capability.
- Consider Hysteresis: Does your application benefit from a stable on/off state? If yes, ensure the sensor offers adjustable hysteresis.
- Mounting & Environment: Choose the correct housing (cylindrical, block-style) and material (stainless steel for harsh conditions). Ensure ingress protection (IP rating) matches the environment.
- Calibration is Key: Never skip proper calibration during installation and after any physical disturbance. Use the actual target object under real operating conditions to set the range and sensitivity optimally. Relying solely on factory defaults rarely yields optimal performance. Document the calibrated settings.
These sensors represent a sophisticated evolution in proximity detection. By offering precise control, they move beyond being simple switches to become intelligent, adaptable components capable of handling a wider scope of tasks with greater resilience and accuracy. Their ability to be tailored to specific challenges ensures they remain a vital and versatile tool in the engineer’s toolkit, continuously enabling smarter, more efficient, and more reliable automated systems across the technological landscape.