датчик переключателя приближения Холла
- time:2025-07-10 04:12:52
- Нажмите:0
Hall Proximity Switch Sensors: Your Guide to Non-Contact Magnetic Detection
Ever need to know if something is there without touching it? In the complex world of automation and machinery, reliably detecting the presence, absence, or position of objects is fundamental. Yet, physical contact often leads to wear, damage, and premature failure. That’s where the ingenious Hall proximity switch sensor steps in – offering a robust, non-contact solution powered by a fundamental scientific principle. Understanding these sensors unlocks enhanced reliability and efficiency across countless applications.
The Science Behind the Switch: Understanding the Hall Effect
At the heart of every Hall proximity sensor lies the Hall effect, discovered by Edwin Hall in 1879. When an electrical current flows through a thin conductor (like a semiconductor material) and a magnetic field is applied perpendicular to this current flow, a voltage (the Hall voltage) is generated across the conductor at right angles to both the current and the magnetic field. This voltage is directly proportional to the strength of the magnetic field.
A Hall proximity switch sensor capitalizes on this phenomenon. It combines:
- A Hall Effect Element: The semiconductor chip that generates the Hall voltage when exposed to a magnetic field.
- Signal Conditioning Circuitry: This amplifies the tiny Hall voltage and processes it.
- An Output Stage: Typically a solid-state electronic switch (like a transistor). When the magnetic field strength crosses a predefined threshold, this switch rapidly changes state – like turning a light on or off.
- A Protective Housing: Encases the components, often incorporating magnets or being designed to sense external magnets on the target.
How Does a Hall Proximity Switch Actually Work?
The operation is elegantly simple and reliably contactless:
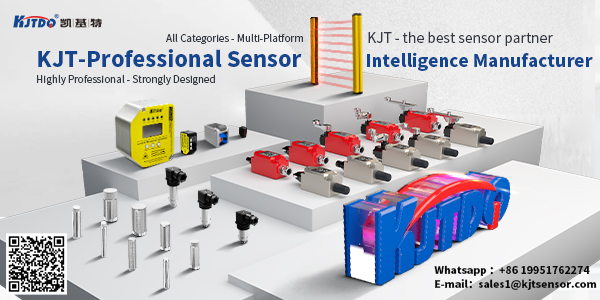
- Presence: The sensor is mounted in a fixed location. A permanent magnet is attached to the moving object (the “target”) that needs detection. As the target approaches the sensor, the magnet’s field strength at the Hall element increases.
- Threshold Crossing: When the magnet gets close enough, the magnetic flux density surpasses the sensor’s built-in activation threshold.
- Switching Action: The internal circuitry detects this increase due to the rising Hall voltage. It instantly triggers the output switching element to change state (e.g., from “OFF” to “ON”, or open-circuit to closed-circuit).
- Absence: As the target (and magnet) moves away, the magnetic field strength drops below the release threshold (often slightly lower than the activation threshold to prevent chatter), causing the output to return to its original state.
This magnetic field interaction provides true non-contact sensing, eliminating mechanical wear and enabling high-speed, long-life operation.
Key Types and Their Outputs
Hall proximity sensors primarily come in two flavors based on their output behavior:
- Unipolar Switches: These respond to one specific magnetic pole (usually the South pole facing the sensing side). They switch ON when the correct pole approaches and OFF when it moves away. They ignore the opposite pole. Simplicity and cost-effectiveness are their hallmarks.
- Bipolar Switches (Latching): These respond to both magnetic poles. Approaching a South pole switches the output ON. Approaching a North pole then switches it OFF (or vice-versa, depending on design). Crucially, they latch (or stay) in their last switched state even after the magnet is removed. This “memory” function is invaluable for applications like position verification or counting.
- Omnipolar Switches: A less common variant that switches ON when either pole approaches and OFF when the field disappears. Useful where magnet polarity orientation is uncertain.
The output itself is usually:
- Digital (Switch-like): Either NPN (sinking) or PNP (sourcing) transistor outputs, common in industrial PLC and control systems. These can handle significant currents to directly drive small relays, indicator lights, or PLC inputs.
- Analog: Some variants provide a voltage or current output proportional to the magnetic field strength, useful for position sensing (though less common in pure “proximity switch” roles).
Why Choose a Hall Proximity Switch? Key Advantages
Hall effect proximity sensors offer compelling benefits:
- True Non-Contact Operation: Eliminates physical wear and tear on both the sensor and target, ensuring extremely long operational life.
- High Reliability and Repeatability: Solid-state electronics are inherently robust against vibration, shock, and environmental contaminants like dust, oil, and moisture (depending on IP rating).
- High-Speed Switching: Capable of operating at frequencies well into the kilohertz range, ideal for counting fast-moving objects or high-speed position detection.
- Immunity to Environmental Factors: Unlike optical sensors, they aren’t affected by dirt, dust, fog, or ambient light. They perform consistently in challenging conditions.
- Wide Operating Temperature Range: Typically function reliably across a broad range, from sub-zero temperatures to well over 100°C.
- Position Insensitivity: Sensors with a suitable operating distance and omnipolar types aren’t sensitive to the exact position of the magnet within their sensing range, simplifying installation.
- Zero-Speed Sensing: Can detect a stationary magnetic field, perfect for end-of-travel or parked position confirmation.
Where Hall Proximity Switches Shine: Applications
Their unique strengths make Hall sensors indispensable across numerous sectors:
- Automotive: Gear position sensing, brake pedal/switches, seat belt buckles, steering wheel position, window/door limit switches, throttle position, camshaft/crankshaft position.
- Factory Automation & Robotics: End effector position, cylinder piston position (pneumatic/hydraulic), limit switches on linear/rotary axes, conveyor belt object counting, motor commutation (BLDC motors), door/window monitoring on cabinets.
- Consumer Electronics & Appliances: Lid/door closure detection in washing machines, dryers, refrigerators; blender/juicer safety interlocks; fluid level sensing (float magnets).
- Промышленное оборудование: Machine tool positioning, spindle orientation, paper feed detection, printing registration, safety interlocks.
- Medical Devices: Syringe pump position, bed/chair position feedback, cabinet door monitoring.
- Аэрокосмическая деятельность: Landing gear position, flap position, hatch closure confirmation.
Selecting the Right Hall Proximity Switch Sensor
Choosing the optimal sensor involves considering several factors:
- Operating Principle: Unipolar, Bipolar (Latching), or Omnipolar? Does the application require latching behavior? What magnet pole orientation is used?
- Sensing Distance (Switching Distance): How far away does the target magnet need to activate the sensor? Ensure the rated distance accounts for mounting tolerances and target movement.
- Output Type & Wiring: NPN or PNO transistor? Voltage level? Does it match the input requirements of your controller (PLC, microcontroller)? Usually requires a 3-wire connection (V+, 0V, Output).
- Supply Voltage: Match the sensor’s operating voltage range (e.g., 5V DC, 12-24V DC, 10-30V DC) to your system’s power supply.
- Environmental Protection (IP Rating): Will the sensor be exposed to dust, water, oils, or chemicals? Choose an appropriate IP rating (e.g., IP67 for washdown environments).
- Temperature Range: Ensure the sensor’s rated operating and storage temperatures cover the application environment.
- Housing Material & Size: Does the form factor fit the mounting location? Is stainless steel required for chemical resistance?
- Magnet Requirements: Understand the required magnet strength, size, and orientation relative to the sensor’s face. Manufacturer datasheets provide crucial guidance.
Beyond Basic Proximity: Limitations
While incredibly versatile, Hall proximity sensors have boundaries:
- Magnetic Field Required: They only detect magnetic fields