wenglor inductive sensor
- time:2025-07-09 02:49:10
- Нажмите:0
Wenglor Inductive Sensors: Precision, Reliability, and Innovation in Object Detection
Imagine a high-speed production line humming efficiently. Bottles zip past filling stations, robotic arms weld car frames with pinpoint accuracy, and metal components are precisely positioned for assembly. Behind this seamless orchestration lies a critical, often unseen, technology: inductive sensors. Among the leaders in this field, wenglor inductive sensor solutions consistently deliver the precision, reliability, and robustness that modern automation demands. They are the silent guardians ensuring processes run smoothly, safely, and without interruption.
The Essence of Inductive Sensing: Seeing Without Touching
At their core, inductive proximity sensors operate on a simple yet profound principle: they detect the presence or absence of metallic objects without physical contact. They achieve this by generating an electromagnetic field. When a metallic target enters this field, eddy currents are induced within the target itself. These currents cause a detectable change in the sensor’s internal oscillation amplitude. The sensor’s electronics convert this change into a clean, switch-like output signal.
This fundamental non-contact nature provides immense advantages:
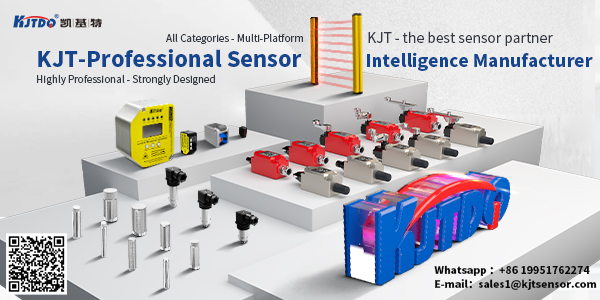
- Unrivaled Durability: With no moving parts to wear out, wenglor sensors boast exceptional longevity, even in the harshest industrial environments filled with dust, oil, vibrations, and temperature fluctuations.
- Maintenance-Free Operation: No physical contact means no mechanical wear and tear, significantly reducing downtime and maintenance costs.
- High-Speed Detection: Capable of operating at high switching frequencies, they effortlessly track fast-moving targets on conveyor belts or rapidly cycling machinery.
- Impervious to Surface Conditions: They reliably detect targets regardless of surface texture, color, transparency, or the presence of contaminants like dust or water (though liquid metal detection requires specific designs).
Why wenglor Inductive Sensors Excel: Engineered for Excellence
wenglor doesn’t just manufacture inductive sensors; they engineer solutions tailored to specific industrial challenges. Several factors set them apart:
- Outstanding Precision and Range: wenglor inductive sensors are renowned for their exceptional repeatability and switching distance accuracy. This means consistent, dependable detection every single time, critical for delicate positioning tasks or high-precision manufacturing. Their range-to-size ratio is often industry-leading.
- Unmatched Robustness: Built to endure, these sensors feature high-quality housings (often stainless steel V4A, Nickel-plated brass, or rugged PBT/PPS plastic) with superior ingress protection ratings (commonly IP67, IP68, IP69K). They resist shock, chemicals, and extreme temperatures, ensuring reliable performance in demanding settings like automotive plants, food processing, or foundries.
- Diverse Form Factors: From rugged cylindrical M8, M12, M18, M30 sizes to compact rectangular block designs or microminiature sensors for space-constrained applications, wenglor offers unparalleled variety. This flexibility allows engineers to select the perfect sensor for any mounting scenario.
- Advanced Functionality: Beyond simple presence detection, wenglor provides sensors with specialized capabilities:
- Factor 1 Sensors: Detect different metals (ferrous and non-ferrous) reliably at the same switching distance, simplifying setup and stock management.
- High-Temperature Models: Specifically engineered to function reliably in environments exceeding standard operating temperatures.
- Analog Output Sensors: Provide continuous distance or position information (e.g., 4-20mA, 0-10V), enabling precise measurement tasks.
- IO-Link Capability: Many modern wenglor sensors feature IO-Link communication, enabling advanced diagnostics, parameter setting via the controller, and seamless integration into Industry 4.0 / IIoT networks.
- Innovative Technologies: wenglor continuously pushes boundaries. Technologies like Delta-S technology significantly boost switching distances, while specialized designs offer immunity against interference from adjacent metals or sensors.
wenglor Inductive Sensors in Action: Core Applications
The versatility of wenglor inductive sensor systems makes them indispensable across virtually all manufacturing and automation sectors:
- Position Verification: Confirming the presence of pistons in cylinders, detecting end positions of slides or clamps, verifying part placement before machining or assembly. Their reliability prevents costly errors.
- Object Counting: Accurately tallying bottles, cans, packages, or metal components on high-speed conveyors with non-contact precision.
- End-of-Stroke Detection: Monitoring cylinders and actuators, ensuring movements complete correctly for machine sequencing and safety.
- Speed Monitoring: Using sensors to detect gear teeth or other metallic features for rotational speed measurement.
- Level Detection: Monitoring metal fill levels in tanks, hoppers, or silos (within limitations of the technology).
- Machine Safety: Contributing to safety systems by verifying guard positions or detecting faults before potentially hazardous conditions arise.
Selecting the Right wenglor Inductive Sensor
Choosing the optimal sensor involves careful consideration:
- Target Material: Is it ferrous steel, non-ferrous aluminum/brass/copper, or stainless steel? Standard sensors have different ranges for different metals; Factor 1 sensors offer uniformity.
- Required Sensing Distance: How far away does the sensor need to detect the target? Always consult wenglor datasheets for nominal and guaranteed operating distances.
- Mounting Space and Environment: Cylindrical vs. rectangular? Miniature size? Consider available space and the presence of vibration, chemicals, washdown requirements (IP69K), or extreme temperatures.
- Electrical Requirements: Preferred voltage supply (10-30V DC typical), output type (NPN/PNP, NO/NC, analog, IO-Link), and connection method (cable, connector).
- Special Features: Needed factor 1 capability? Analog output? High-temperature rating? IO-Link connectivity for smart factory integration?
Driving Innovation Forward
wenglor remains at the forefront of sensor technology. Continuous R&D focuses on enhancing performance (even longer ranges, smaller sizes), improving ruggedness, and deepening integration with smart manufacturing concepts. The integration of sensors with IO-Link is a key trend, transforming simple detection devices into intelligent data points within the Industrial Internet of Things (IIoT). This allows for predictive maintenance, remote diagnostics, and process optimization data, adding significant value beyond basic switching.
From the smallest microminiature sensor verifying component insertion on a PCB to robust heavy-duty sensors monitoring massive hydraulic presses, wenglor inductive sensor technology delivers the unwavering performance demanded by modern industry. Their commitment to precision engineering, material quality, and embracing connectivity ensures they remain a cornerstone of reliable, efficient, and increasingly intelligent automation systems globally. When metal detection demands the highest standards of accuracy, durability, and innovation, wenglor consistently provides the solution.