Неметаллический датчик приближения
- time:2025-07-08 03:31:20
- Нажмите:0
Beyond Metal Detection: The Essential Role of Non-Metallic Proximity Sensors
Imagine a high-speed bottling line – plastic containers whizzing by, glass jars clinking, cardboard packages gliding past. Or picture a modern woodworking shop, intricate cuts being made on composite materials. How does sophisticated machinery reliably “see” and interact with these non-conductive materials without missing a beat or causing damage? The answer lies in the often unsung heroes of industrial automation: non-metallic proximity sensors.
Unlike their inductive counterparts specifically designed for ferrous and non-ferrous metals, non-metallic proximity sensors are engineered to detect targets that don’t conduct electricity. This capability unlocks a vast array of applications across industries plagued by the limitations of metal-only detection, enabling automation that’s safer, more precise, and vastly more versatile.
Understanding the Core Technology: How “Non-Metallic” Sensing Works
The term “non-metallic proximity sensor” isn’t tied to a single technology but encompasses several key types, each suited for specific material properties:
Capacitive Proximity Sensors: These are the most common solution for detecting solids, powders, and liquids regardless of electrical conductivity. They function by generating an electrostatic field. When any material enters this field, it causes a measurable change in capacitance – essentially a shift in the sensor’s ability to store an electrical charge. Even minute changes caused by plastics, wood, paper, glass, liquids, or granular substances trigger the sensor’s output signal. Adjustable sensitivity is a crucial feature here, allowing engineers to fine-tune detection range and ignore background materials like container walls.
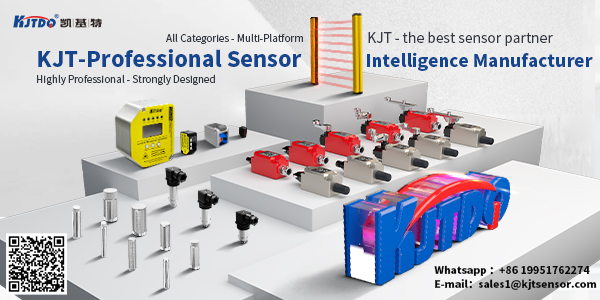
Ultrasonic Proximity Sensors: These sensors emit high-frequency sound waves and measure the time it takes for the echo to return. The distance to the target, rather than its material composition, is the primary detection principle. This makes them highly effective for detecting virtually any object, solid or liquid, at longer ranges than capacitive sensors. They excel in challenging environments with dust, fog, or target color variations that can confuse optical sensors, and are invaluable for continuous level monitoring of liquids and bulk solids.
Photoelectric Sensors (Specific Types): While photoelectric sensors are a broad category, diffuse and retro-reflective types equipped with specific light sources or advanced optics can reliably detect non-metallic objects. They detect the presence or absence of an object by sensing changes in light intensity (diffuse) or by the return of a light beam (retro-reflective). Advanced variants, sometimes incorporating background suppression or contrast detection techniques, offer reliable detection for transparent bottles, colored plastics, and uneven surfaces where basic reflection principles might fail.
Why Choose Non-Metallic Detection? The Compelling Advantages
Reaching for a non-metallic proximity sensor isn’t just about necessity; it offers tangible benefits:
- Unmatched Versatility: Detect virtually any material – plastics, glass, wood, cardboard, textiles, adhesives, liquids, powders, grains, biological materials. This opens doors to automation in previously challenging sectors.
- Solving Inductive Limitations: Inductive sensors simply can’t detect non-metallic objects. Non-metallic proximity sensors fill this critical gap in modern manufacturing and processing.
- Contactless Operation: Like all proximity sensors, they operate without physical touch, eliminating wear and tear on both the sensor and the target material. This is particularly vital for fragile items.
- Enhanced Hygiene: Sensors designed for sanitary environments (often capacitive or ultrasonic with specific housings) are essential in food, beverage, and pharmaceutical applications where cleanliness is paramount. They withstand washdowns and resist contamination.
- Reliable Level & Fill Control: Capacitive and ultrasonic sensors are indispensable for accurately monitoring levels of liquids, pastes, powders, and granular materials in tanks, silos, and hoppers.
- Improved Safety & Automation: Presence detection of non-metallic guards, doors, or obstacles using these sensors enhances machinery safety and prevents jams.
Critical Applications Driving Demand
The practical uses for non-metallic proximity sensors are extensive and growing:
- Food & Beverage Processing: Detecting plastic or glass bottles, cans, lids, caps, cardboard packaging fill levels of liquids/ingredients, verifying presence of food products on conveyor belts, ensuring tamper-evident seals are present. Food-grade capacitive sensors are common here.
- Packaging & Labeling: Verifying presence of cardboard boxes, plastic films, labels, tapes, bottles, blister packs, ensuring cartons are properly folded or glued.
- Woodworking & Furniture Manufacturing: Detecting wood boards, panels, MDF, laminates, veneers, verifying glue application, presence of components during assembly.
- Plastics & Rubber Industry: Detecting extruded plastic profiles, molded parts, pellets, rubber sheets, presence in injection molding machines.
- Pharmaceutical & Medical: Ensuring proper fill levels in vials and containers, verifying presence of plastic caps, blister packs, syringes, labels, and packaging components in sterile environments.
- Automotive (Non-Metal Components): Verifying presence of plastic bumpers, dashboards, interior trim pieces, rubber seals, glass panels, fluid levels in reservoirs (e.g., washer fluid, coolant).
- Chemical & Bulk Handling: Reliably monitoring levels of powders, granules, pellets, and aggressive liquids in tanks and silos.
- Printing & Paper: Detecting paper rolls, sheets, jams, verifying presence of ink cartridges or toners.
Selecting the Right Sensor: Key Considerations
Choosing the optimal non-metallic proximity sensor requires careful thought:
- Target Material: What exactly needs detecting? (Plastic? Glass? Liquid? Wood? Powder?) Different materials interact uniquely with capacitive and ultrasonic fields or light.
- Operating Environment: Consider temperature extremes, humidity, dust, dirt, potential chemical exposure, and washdown requirements (IP rating is crucial). Ultrasonic sensors often handle harsh, dusty environments best.
- Required Sensing Distance: Capacitive sensors generally have shorter ranges than ultrasonic ones. Measure the maximum distance the sensor needs to detect from. Some capacitive sensors offer extended ranges.
- Mounting Constraints: Physical space limitations around the installation point?
- Output Type Needed: Does the control system require a simple PNP/NPN switch, analog output (for level), or IO-Link communication for diagnostics?
- Response Speed: How quickly does the sensor need to detect targets on a fast-moving line? Photoelectric sensors often offer the fastest response times.
- Environmental Noise: Potential interference from other electrical equipment, vibration, or acoustic noise? Shielding and sensor selection (e.g., robust ultrasonic variants) mitigate this.
- Hygiene Requirements: Food, Pharma, and Beverage demand specific hygienic designs and certifications (e.g., EHEDG, FDA compliance).
From essential processes to innovative applications, non-metallic proximity sensors are the silent enablers of modern automation, ensuring efficiency, safety, and product quality wherever traditional metal detection falls short. By understanding the distinct capabilities of capacitive, ultrasonic, and photoelectric variants, engineers can implement the precise sensing solution needed to optimize performance across countless industries.