festo reed sensor
- time:2025-07-07 12:28:24
- Нажмите:0
Festo Reed Sensors: Reliable Magnetic Proximity Sensing in Industrial Automation
Unlock robust, simple, and dependable position detection with Festo reed sensors – the foundational technology powering countless automated systems.
In the intricate dance of modern industrial automation, knowing the precise position of a moving component is often mission-critical. Enter the Festo reed sensor, a stalwart solution leveraging fundamental physics for reliable proximity detection. While newer technologies constantly emerge, the simplicity, cost-effectiveness, and inherent robustness of reed switch sensors, especially those engineered by Festo for demanding industrial environments, ensure their enduring relevance. These unsung heroes provide essential feedback, particularly in pneumatic systems, ensuring cylinders extend, retract, and stop precisely where needed, cycle after cycle.
Understanding the Core Principle: Reed Switch Technology
At the heart of every Festo reed sensor lies a reed switch. This ingenious component is surprisingly simple: two thin, ferromagnetic metal reeds (typically nickel-iron alloy) are hermetically sealed within a small glass tube filled with an inert gas. When exposed to an external magnetic field – usually generated by a permanent magnet mounted on the moving part being monitored – these reeds magnetize. Their opposite poles attract, causing them to flex and make contact, effectively closing an electrical circuit. When the magnetic field is removed, the reeds’ natural springiness causes them to separate, opening the circuit again. This binary action (open/closed) provides a clear, unambiguous signal about the presence (or absence) of the magnet, and thus the position of the target.
Why Festo Reed Sensors Excel in Industrial Applications
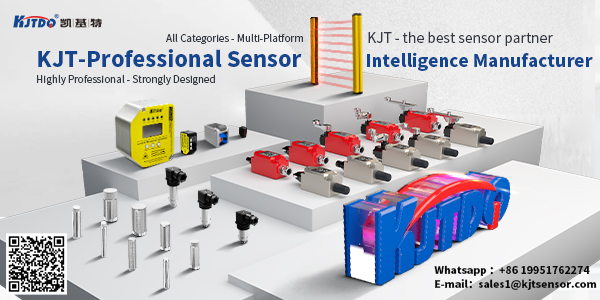
Festo harnesses this fundamental reed switch principle and builds upon it, optimizing these sensors for harsh industrial realities:
- Exceptional Durability and Longevity: The hermetic glass encapsulation protects the delicate reeds from dust, dirt, humidity, oil, and many corrosive agents commonly found in factories. With no moving parts subject to mechanical wear (the reed flexing occurs within the sealed environment), these sensors boast an incredibly long operational life, often reaching millions of switching cycles. Festo’s rigorous manufacturing standards ensure consistent quality and reliability crucial for continuous operation.
- Simplicity and Reliability: Their purely magnetic actuation means they require no physical contact with the target magnet. This non-contact operation eliminates wear on both the sensor and the target, further enhancing longevity. The output is a simple switch signal (often referred to as a reed contact sensor), making integration into control systems straightforward – typically connecting directly to PLC digital inputs or pilot lights.
- Cost-Effectiveness: Compared to many electronic proximity sensors (inductive, capacitive, photoelectric), reed sensors offer a significantly lower entry price point while delivering robust performance for basic position detection tasks. This makes them an economically attractive solution, especially for applications requiring multiple sensing points.
- High Switching Speed & Low Power Consumption: The lightweight reeds can respond extremely quickly to magnetic fields, enabling detection of very rapid movements. Furthermore, they require only minimal electrical power to operate the switch, contributing to overall system energy efficiency.
- Immunity to Environmental Factors: Reed sensors are unaffected by non-metallic contaminants like dust, wood chips, plastic shavings, or water spray (as long as the sensor body’s IP rating is suitable) that could easily disrupt optical sensors. They also function reliably in environments with electrical noise that might interfere with more sensitive electronic sensors.
Core Applications: Where Festo Reed Sensors Shine
Their unique strengths make Festo magnetic sensors, particularly reed types, ideal for numerous position-sensing scenarios:
- Pneumatic Cylinder End Position Detection: This is the quintessential application. Magnets embedded in the cylinder piston actuate reed sensors mounted externally on the cylinder body to signal fully retracted and/or fully extended positions. Festo position sensors designed for cylinders are precisely engineered for optimal magnetic coupling and secure mounting.
- Valve Spool Position Monitoring: Similar to cylinders, reed sensors can detect the position of spools inside directional control valves, confirming switching states.
- Door/Hatch Position Sensing: Used to verify if machine guards, access doors, or safety gates are securely closed (limit switch function).
- Simple Object Detection: Detecting the presence of a magnet-equipped carrier, pallet, or component passing a specific point.
- Level Sensing: In certain fluid tanks, a float containing a magnet rises and falls, actuating reed sensors at predetermined high and low levels.
Key Considerations and Selection Criteria
While highly reliable, selecting the right Festo proximity sensor based on reed technology requires attention to detail:
- Switching Distance: The critical distance at which the sensor reliably reacts to the magnet. Ensure the magnet passes close enough to the sensor’s sensing face. Festo provides precise specifications for each sensor model and often recommends compatible cylinder magnets.
- Magnet Strength and Orientation: The sensor’s performance is highly dependent on the strength and polarity of the target magnet. Always use the magnet specified or recommended by Festo for optimal operation.
- Electrical Specifications: Match the sensor’s voltage rating (e.g., DC 5-30V), current rating, and switching type (Normally Open / NO, Normally Closed / NC, or Changeover / SPDT) to your control system’s requirements.
- Environmental Conditions: Verify the sensor’s IP rating (Ingress Protection) ensures suitability for the operating environment – protection against dust and water jets is common. Consider operating and storage temperature ranges.
- Mounting Requirements: Festo offers various mounting options (brackets, barrel styles, threaded bodies) for integration onto cylinders, profiles, or machine frames. Ensure mechanical compatibility.
- Output Configuration: Reed sensors typically offer direct switching of load currents (e.g.,
Festo’s Value: Beyond the Basic Reed Switch
While leveraging the fundamental reed switch, Festo enhances these sensors for industrial use:
- Robust Housings: Engineered from resilient materials like stainless steel or PBT plastic to withstand shock, vibration, and chemical exposure.
- Optimized Sensing Geometry: Precise positioning of the internal reed switch relative to the housing surface maximizes sensitivity and switching distance consistency.
- Integrated Mounting Solutions: Dedicated brackets, clips, and pre-configured kits simplify and accelerate installation on Festo cylinders and other components.
- Variants: Offering choices like reed sensors with LED status indicators for visual confirmation of operation, or specific designs for high-pressure washdown environments.
Conclusion: A Proven Performer
In an era of complex electronics, the Festo reed sensor stands as a testament to the enduring power of simple, well-executed engineering. By mastering the fundamental interaction between magnetism and ferrous materials, Festo delivers proximity sensors prized for their rock-solid reliability, cost efficiency, and resilience in demanding industrial settings. For critical position feedback tasks, especially within pneumatic systems, these magnetic workhorses continue to offer an unmatched blend of performance and value, ensuring processes run smoothly and predictably. Choosing the right reed contact sensor from Festo means investing in proven dependability for your automation needs.