Сенсорный датчик M18
- time:2025-07-07 12:00:09
- Нажмите:0
The M18 Inductive Sensor: Precision Proximity Detection for Demanding Automation
Imagine a high-speed assembly line humming with activity. Robotic arms whir, conveyor belts surge forward, and components slot together with millimeter precision. How does this complex machinery know exactly where each metal part is without constant manual oversight? The silent, tireless heroes enabling this precise detection are often M18 Inductive Proximity Sensors. This compact yet powerful workhorse is fundamental to modern industrial automation, offering unparalleled reliability for non-contact metal detection.
Understanding the M18 Inductive Sensor
At its core, an индукционный датчик приближения detects the presence of metallic objects without requiring physical touch. The “M18” designation refers specifically to the standardized cylindrical housing diameter of 18 millimeters. This size strikes an optimal balance, providing a robust physical form factor suitable for tight installation spaces while allowing a substantial sensing range. These sensors operate on the inductive principle: an internal oscillator generates a high-frequency electromagnetic field emanating from the sensor’s active face. When a ferrous (iron-based) or non-ferrous (like aluminum, brass, or copper) metal target enters this field, eddy currents are induced within the target. These eddy currents draw energy from the sensor’s oscillating field, causing a detectable change in its amplitude or frequency. The sensor’s built-in electronics process this change and trigger a solid-state output switch (like turning a light on or off electronically), signaling the presence of the target.
Why the M18 Size Reigns Supreme
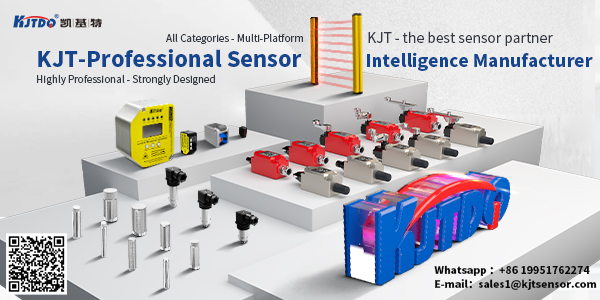
The widespread adoption of the M18 inductive sensor format isn’t accidental. It offers distinct advantages:
- Versatility & Standardization: The 18mm diameter is an industry standard. This means M18 sensors from different manufacturers often share similar mounting dimensions (thread type, typically M18x1 or M18x1.5), sensing ranges, and electrical characteristics (like connection styles: cable or connector types like M8/M12). This interchangeability simplifies sourcing, replacement, and maintenance.
- Прочная структура: Built for demanding industrial environments, M18 sensors feature sturdy metal (often stainless steel) or thermoplastic housings. They typically boast high Ingress Protection (IP) ratings, such as МП67 or IP68, meaning they are highly resistant to dust and capable of withstanding temporary immersion in water – crucial for washdown areas, foundries, or outdoor applications. They are also highly resistant to shock and vibration.
- Practical Sensing Range: For an M18 inductive sensor, the nominal sensing range (Sn) typically ranges from 2mm to 8mm, depending on the specific model and target material (ferrous metals offer the longest range). This range is often ideal for common machine automation tasks like detecting pistons, end positions, part presence, or counting metallic objects on conveyors.
- Reliable Non-Contact Operation: Because they detect targets without physical contact, M18 inductive sensors eliminate mechanical wear and tear. This translates to exceptional longevity and minimal maintenance, significantly reducing downtime and operating costs.
- Output Flexibility: M18 sensors are available with different electronic output configurations to interface seamlessly with Programmable Logic Controllers (PLCs) and other control systems. The main types are:
- NPN Output (Sinking): Switches the negative (ground) leg of the load. Common in Asian-manufactured equipment.
- PNP Output (Sourcing): Switches the positive voltage leg of the load. Common in European and North American equipment.
- Normally Open (NO) / Normally Closed (NC): Defines the output state when no target is present.
- Mounting Options: M18 sensors feature an external thread along their barrel, allowing simple and secure installation into threaded holes or brackets. Considerations include flush mounting (sensor face level with the surrounding metal) for reduced side detection influence, or non-flush mounting (sensor face protruding) which often provides a slightly longer sensing range. Shielded sensors are designed for flush mounting and offer reduced sensitivity to nearby metal, while Unshielded types are optimized for non-flush mounting and maximum range.
Key Applications: Where the M18 Excels
The M18 inductive sensor’s blend of size, ruggedness, and reliable detection makes it ubiquitous across countless industries:
- Factory Automation: Detecting position of cylinders, end stops of linear actuators, presence/absence of parts on conveyors or pallets, robotic arm positioning, tool changer confirmation, and machine guarding.
- Packaging Machinery: Verifying metal lids or caps are present and positioned correctly, counting cans or bottles (via metal components), detecting foil seals, and monitoring filling levels (using metal floats).
- Перевозка материалов: Confirming the position of forklift components, detecting metal pallets or carts, monitoring position on automated guided vehicles (AGVs), and part transfer verification.
- Automotive Manufacturing: Engine block positioning, gear detection in transmissions, verifying placement of suspension components, detecting pistons in cylinders, and robotic welding seam tracking.
- Machining Centers: Tool presence verification in tool changers, chuck jaw positioning, part clamping confirmation, and coolant level monitoring (with metal float).
- Building & Construction: Elevator car position detection, door open/close status, security systems for detecting gate positions.
Selecting the Right M18 Sensor: Key Considerations
Choosing the optimal M18 sensor involves evaluating several factors:
- Target Material: Specify whether it’s ferrous steel, stainless steel, aluminum, brass, or copper. The sensor’s range varies significantly with material type. Always refer to the sensor’s datasheet.
- Required Sensing Distance (Sn): Choose a sensor with a nominal range slightly larger than the maximum distance your target will pass the sensor face. Account for potential installation tolerances.
- Output Type (NPN/PNP, NO/NC): Must match the input requirements of your PLC or control system. NPN vs PNP compatibility is critical.
- Operating Voltage: Most industrial M18 sensors operate on 10-30V DC. Ensure compatibility with your power supply.
- Environmental Factors: Consider ambient temperature extremes, potential exposure to coolants, oils, chemicals, welding sparks, or high-pressure washdown. Select appropriate housing material (stainless steel often preferred for harsh conditions) and a sufficiently high IP rating (IP67/IP68 is standard for robust needs).
- Mounting Constraints: Determine if flush or non-flush mounting is possible/required. Choose shielded or unshielded accordingly.
- Connection Style: Pre-terminated cable or a connector plug (like industry-standard M8 or M12)? Cable length needed?
- Special Features: Some models offer IO-Link communication for advanced diagnostics and parameterization, extra long sensing ranges, high-temperature resistance, or specific approvals (ATEX for hazardous areas).
Installation and Care: Maximizing Performance
Proper installation is key to reliability: