Магнитный датчик ближнего действия
- time:2025-07-06 02:42:49
- Нажмите:0
Magnetic Proximity Sensors: The Silent Detectives Powering Modern Automation
Open a car door, start your dishwasher, or watch a high-speed production line – chances are, a magnetic proximity sensor is silently making it happen. These unassuming yet crucial components are the invisible workhorses of countless applications, providing reliable, non-contact detection of the presence or absence of ferromagnetic objects. Understanding their operation, strengths, and diverse applications reveals why they are indispensable in today’s automated world.
How Does a Magnetic Proximity Sensor Work? Unveiling the Principle
At its heart, a magnetic proximity sensor relies on a fundamental principle: the interaction between a permanent magnet and a sensing element triggered by changes in a magnetic field. Unlike inductive sensors that generate their own electromagnetic field to detect metallic objects, magnetic prox sensors utilize an externally generated magnetic field, typically from a separate magnet (often called a “target”) attached to the object being monitored.
Here’s the core operation:
- The Magnet: A permanent magnet is mounted on the moving part that needs detection (e.g., a door, piston, or machine component).
- The Sensor: The stationary sensor itself contains a magnetically sensitive element, most commonly either a:
- Reed Switch: Sealed glass capsule containing two ferromagnetic contacts. When the external magnet approaches, the contacts are magnetized and attract each other, closing the switch circuit. When the magnet moves away, the contacts spring back open. (Simple, robust, inexpensive).
- Hall Effect Sensor: Semiconductor device. When exposed to a magnetic field perpendicular to current flow, it generates a voltage difference (the Hall voltage). This small voltage is amplified and processed by integrated circuitry within the sensor to produce a clean, switch-like output signal. (Faster switching, longer life, more precise positioning capability, can detect both poles).
- Detection Event: As the target magnet moves into the sensor’s effective sensing range, it triggers the internal sensing element (reed switch closes or Hall voltage changes). This causes the sensor’s output state to change (e.g., from OFF to ON). The output reverts when the magnet moves away beyond the sensing range.
Key Characteristics and Advantages: Why Choose Magnetic Prox?
Magnetic proximity sensors offer a compelling set of features:
- Non-Contact Operation: No physical connection to the target is needed, eliminating wear and tear and enabling detection through non-ferromagnetic materials like plastic, glass, or aluminum enclosures. This is a significant benefit for durability and maintenance reduction.
- Immunity to Common Interferences: They are largely unaffected by dust, dirt, oils, moisture, vibrations, or acoustic noise that plague other sensing technologies, making them highly reliable in harsh industrial environments.
- Simple Installation: Typically requiring only power and ground connections (for active sensors like Hall Effect types), they are straightforward to install and integrate.
- Long Sensing Ranges (Relative to Size): Especially powerful magnets paired with sensitive Hall Effect sensors can achieve impressive sensing distances relative to their compact size.
- Position Independence: Unlike some optical sensors requiring precise alignment, magnetic sensors often detect the presence of the magnetic field regardless of its exact rotational position relative to the sensor face (axial sensing is common).
- Solid-State Reliability (Hall Effect): Hall Effect sensors have no moving parts like reed switches, offering potentially millions of switching cycles and excellent shock/vibration resistance. Reed switches, while having a finite mechanical life, are still highly robust for many applications.
Diverse Applications: Where Magnetic Prox Sensors Shine
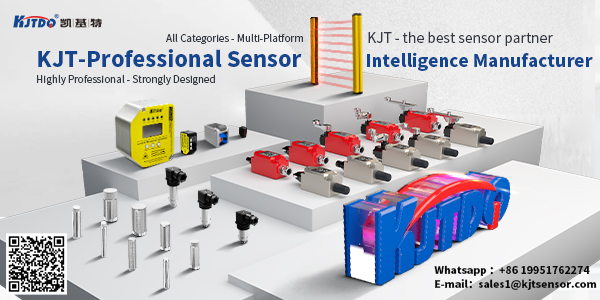
Their unique blend of robustness and non-contact detection makes them ideal for a vast array of scenarios:
- Промышленная автоматизация: Monitoring cylinder piston position (end-of-stroke detection), verifying door/cabinet closure on machines, detecting ferrous parts on conveyors, counting metallic objects, confirming tool changes.
- Automotive: Gear position sensing (manual transmissions), brake pedal position, clutch engagement detection, seat belt buckle detection, door/trunk/hood ajar switches, steering wheel position.
- Home Appliances: Detecting washing machine drum position, lid closure on dryers/dishwashers, water level sensors (using a float magnet), oven/stove door closure.
- Building Automation: Window/door security sensors (detecting opening/closing), elevator position control, automatic sliding door sensors.
- Medical Equipment: Position feedback in pumps, motors, and movable components within diagnostic or treatment devices.
- Consumer Electronics: Detect flip/slide phone positions, laptop lid open/close detection, presence detection in docks/cradles.
Reed Switch vs. Hall Effect: Choosing the Right Tool
Selecting between the two primary types hinges on application requirements:
Reed Switch Sensors:
Pros: Extremely simple, low cost, low power consumption (can be used passively in some circuits), bidirectional (detects either pole), high voltage/current handling possible, galvanic isolation.
Cons: Mechanical contacts subject to wear (finite life, though often millions of cycles), limited switching speed compared to solid-state, potentially lower shock/vibration resistance than Hall, susceptible to strong external magnetic fields interfering with operation.
Best For: Low-cost applications, slower switching speeds, very low power scenarios, simple presence/absence detection where external magnetic fields are controlled.
Hall Effect Sensors:
Pros: Solid-state reliability (no moving parts), very high switching speeds, precise position detection possible (especially latching types), excellent shock/vibration resistance, potentially longer sensing ranges, can be designed to be highly immune to external magnetic fields, directional sensing possible (identify N/S pole).
Cons: Generally require a power supply, typically more expensive than basic reed switches (though prices are competitive), complex electronics potentially more sensitive to electrical noise or extreme voltages.
Best For: High-speed applications, environments with significant vibration/shock, applications demanding millions of operations, precise positional needs, applications requiring immunity to stray fields.
Considerations for Implementation: Maximizing Performance
To ensure reliable operation:
- Sensing Range: Carefully consider the required distance between the sensor and target magnet when activated. Account for mounting tolerances and potential movement. Manufacturer specifications are crucial.
- Magnet Strength & Orientation: The magnet’s size, grade (e.g., N35, N52 Neodymium), distance, and polarity relative to the sensor significantly impact reliable switching. Stronger magnets generally provide longer ranges.
- Environmental Factors: While robust, extreme temperatures can affect magnet strength (especially ceramic magnets) and sensor electronics. Choose sensors rated for the operational temperature range.
- Target Material: Ensure the target the magnet is attached to is thick/strong enough not to flex excessively, which could alter the magnet-sensor distance.
- Electrical Compatibility: Match the sensor’s output type (PNP/NPN/NO/NC analog) and voltage requirements to your control system.
The Ubiquitous Workhorse
From ensuring our car doors are securely closed to enabling precision control in million-dollar manufacturing lines, magnetic proximity sensors are omnipresent yet invisible facilitators of modern life. Their elegant combination of non-contact operation, inherent ruggedness against harsh environments, and relative simplicity makes them a fundamental sensing solution across countless industries. Whether leveraging the simplicity of a reed switch or the precision and speed of Hall Effect technology, magnetic prox sensors continue to be the silent, reliable detectives detecting motion and position where it matters most. Understanding their core principles and advantages empowers engineers and designers to select the optimal sensor, unlocking the full potential of this versatile technology in driving efficiency and reliability within automated systems.