Линейный датчик скорости
- time:2025-07-06 01:48:34
- Нажмите:0
Linear Speed Sensors: The Backbone of Precise Motion Measurement and Control
You need to know exactly how fast something is moving in a straight line. Not rotating, not vibrating – moving linearly. Whether it’s a high-speed conveyor belt carrying delicate packages, the precise positioning of a robotic arm, or critical feedback for vehicle traction control systems, measuring linear velocity accurately is paramount for efficiency, safety, and product quality. This is where the Линейный датчик скорости becomes an indispensable hero in the world of automation and control.
Unlike their rotational counterparts (tachometers), linear speed sensors are specifically engineered to detect and report the velocity of an object moving along a straight or near-straight path. Their output is a direct representation of linear speed, typically in units like meters per second (m/s) or feet per second (ft/s). This direct measurement capability simplifies control systems and provides crucial data where rotational speed alone is insufficient.
Decoding the Core Principle: Relative Motion is Key
At the heart of most linear speed sensors lies the fundamental principle of detecting relative motion between the sensor itself and a target attached to (or inherent to) the moving object. The sensor is usually mounted stationary near the path of motion, while the target moves past or alongside it. The sensor continuously monitors the position of this target over extremely short time intervals. By calculating the change in the target’s position over these tiny time increments (distance divided by time), the sensor derives the instantaneous linear velocity.
The Technological Arsenal: How Do They Measure?
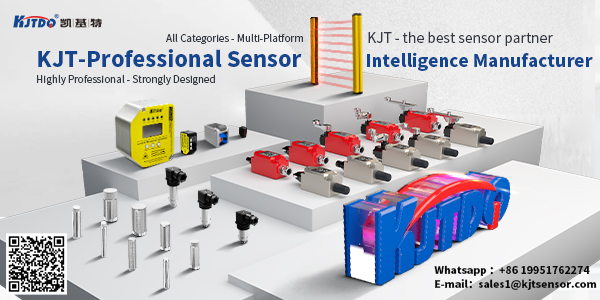
Several well-established physical principles are harnessed in linear speed sensing, each with distinct advantages:
- Magnetic Sensing (Hall-effect & Magnetoresistive): These are incredibly common. A magnetized target (like a strip with alternating North-South poles or a gear tooth made of ferrous material) moves past the sensor. Hall-effect sensors detect changes in the magnetic field, generating a pulse for each pole or tooth passing by. Magnetoresistive (MR) sensors detect changes in magnetic field direction, also producing a pulse train. Calculating the frequency of these pulses provides the velocity. They are robust, non-contact, and work well in harsh environments. MR sensors often offer higher resolution and lower speed detection capabilities than Hall-effect.
- Optical Sensing: Utilizes light (often infrared LED) and a photodetector. A reflective or encoded target interrupts the light beam. For linear measurement, this often involves a linear optical encoder strip with alternating reflective and non-reflective sections. The sensor counts the number of light/dark transitions per unit time to determine speed. Optical sensors offer very high resolution and accuracy but can be sensitive to contamination (dust, oil) and require a clear line of sight.
- Inductive (Eddy Current) Sensing: Primarily used for detecting ferrous metal targets. The sensor generates an electromagnetic field. When a conductive target moves through this field, it induces eddy currents whose properties change with speed. These sensors are rugged and excellent for dirty environments but typically have lower resolution and require metallic targets.
- Capacitive Sensing: Measures changes in capacitance between the sensor and a moving target. As the distance or overlap area changes with motion, the capacitance fluctuates, allowing speed calculation. Useful for non-metallic targets but can be sensitive to environmental factors like humidity.
Where Precision Matters: Key Applications
Linear speed sensors permeate countless industries:
- Industrial Automation & Manufacturing: Monitoring conveyor belt speeds for synchronization, production rate control, and safety interlocks. Controlling the feed rate of materials into processing machines (like cutters, printers, packaging equipment) requires precise linear velocity feedback. Robotic arm positioning often relies on linear speed data for smooth, accurate movements.
- Transportation & Automotive: Critical for Anti-lock Braking Systems (ABS) and Traction Control Systems (TCS), where knowing the linear wheel speed relative to the road surface is essential for preventing skids and maintaining control. Testing vehicle performance on dynamometers involves precise ground speed simulation. Train speed monitoring and door control systems leverage linear speed sensors.
- Material Handling & Logistics: High-speed sorting systems, airport baggage handling conveyors, and warehouse automation all depend on knowing the precise linear speed of parcels and containers to route them correctly and avoid collisions.
- Test & Measurement: Laboratories and R&D facilities use high-precision linear speed sensors to measure the velocity profiles of moving components during product testing and development.
- Аэрокосмическая деятельность: Testing landing gear extension/retraction speeds, monitoring component movement within assemblies.
Selecting the Right Sensor: Beyond Just Speed
Choosing the optimal linear speed sensor involves carefully weighing several factors:
- Measurement Range: What are the minimum and maximum speeds you need to detect? Some sensors excel at low speeds, others at high speeds.
- Accuracy & Resolution: How precise do your measurements need to be? What is the smallest detectable speed change?
- Target Type: Is it ferrous metal? Non-ferrous? Plastic? Reflective? Your target dictates which sensing technologies will work.
- Required Output Signal: Do you need a simple pulse train (TTL, HTL), an analog voltage or current proportional to speed, or a digital communication protocol (CAN, IO-Link)?
- Environmental Conditions: Will the sensor be exposed to extreme temperatures, moisture, dust, oil, chemicals, or strong vibrations? IP ratings and material construction are critical.
- Mounting Constraints: Space limitations, required sensing gap (distance to target), and mounting orientation can rule certain sensors in or out.
- Response Time: How quickly must the sensor react to speed changes?
Installation Insights: Getting it Right
Even the best sensor can deliver poor results if installed incorrectly. Proper alignment relative to the target path is often crucial, especially for optical and some magnetic sensors. Maintaining the correct sensing gap specified by the manufacturer is vital for optimal signal strength and accuracy. Ensuring the target characteristics (material, size, pattern pitch for encoded targets) match the sensor’s requirements is fundamental. Avoiding sources of electrical noise through proper shielding and grounding of cables is also essential for signal integrity.
The Future Track: Emerging Trends
The field of linear speed sensing continues to evolve. Integration of advanced signal processing directly into sensor heads is improving noise immunity and enabling pre-processing of data. The rise of Industrial Internet of Things (IIoT) drives demand for sensors with built-in communication protocols like IO-Link, providing not just speed data but also diagnostic information. Miniaturization makes sensors suitable for increasingly compact machinery, while research into new materials and sensing principles promises even higher accuracy, wider operating ranges, and greater resilience in extreme environments. The core need for reliable, precise linear velocity measurement remains constant, ensuring these sensors will keep machinery—and entire industries—moving forward efficiently and safely.