industrial proximity sensor
- time:2025-07-05 03:12:55
- Нажмите:0
The Unseen Guardians: Industrial Proximity Sensors Powering Modern Automation
Imagine a high-speed assembly line where robotic arms dance with precision, welding sparks fly, and products whizz by. Now, imagine the chaos if every positioning check required physical contact, or if safety gates couldn’t reliably detect an approaching worker. Industrial proximity sensors are the silent, indispensable heroes preventing such scenarios. These remarkable devices act as the digital fingertips of modern manufacturing, enabling machines to “sense” objects nearby without physical touch, driving efficiency, safety, and unprecedented levels of automation control.
Beyond Touch: The Core Principle
At their essence, an industrial proximity sensor is an electronic device designed to detect the presence or absence of an object within its sensing range without any physical contact. It achieves this feat by generating an electromagnetic field, light beam, or ultrasonic signal. When an object enters this field, it causes a detectable change – perhaps altering the field’s characteristics, reflecting a beam, or absorbing sound waves. The sensor’s integrated circuitry interprets this change and switches an output signal (typically turning a load ON or OFF), providing crucial information to the automation control system. This non-contact detection is fundamental to their value, eliminating wear and tear, enabling detection of delicate objects, and operating reliably in dirty, wet, or vibration-prone industrial environments.
The Main Contenders: Types and Technologies
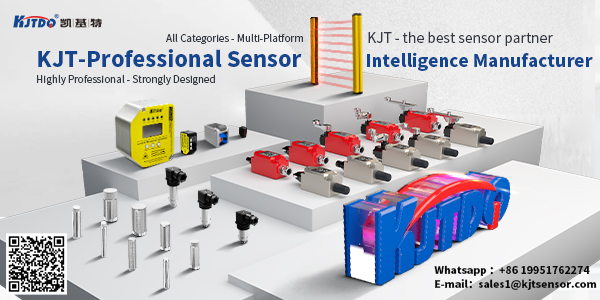
Not all sensing tasks are equal. The diverse demands of manufacturing have led to several key датчик приближения technologies, each excelling in specific scenarios:
- Inductive Proximity Sensors: The undisputed workhorses of metal detection. They generate an electromagnetic field. When a ferrous metal (like steel or iron) or non-ferrous metal (like aluminum or brass) enters this field, it induces eddy currents, causing a measurable change. Inductive sensors are renowned for their robustness, immunity to dust, oil, and moisture (often rated IP67 or higher), and excellent performance in heavy machinery and metalworking applications. Their limitation? They only detect metallic targets.
- Capacitive Proximity Sensors: Masters of versatility. These sensors detect changes in capacitance, a property that can be altered not just by metals, but by nearly any material, including plastics, wood, liquids, powders, and granular substances. The sensor forms one plate of a capacitor; the target object (or a change in the material level) acts as the other plate, altering the capacitance field. This makes конденсаторный датчик ideal for level detection (liquid in tanks, granules in hoppers), detecting non-metallic objects (bottles, cartons), or seeing through insulating materials. They are generally more sensitive to environmental factors like humidity than inductive types.
- Photoelectric Sensors (Often Classified Separately but Function as Proximity Detectors): Leveraging the power of light, these sensors use an emitter (light source - LED, laser) and a receiver. Common proximity-detecting configurations include:
- Diffuse Reflective: The sensor’s emitter and receiver are in one housing. Light hits the target and reflects back to the receiver. Detection is based on sufficient reflected light intensity. Good for most non-mirror-like objects at moderate ranges.
- Retroreflective: The emitter sends a beam to a fixed reflector; the receiver detects the reflected beam. The target breaks this beam. Offers longer sensing ranges and reliable detection of any object interrupting the beam.
- Through-Beam (Beam Break): Emitter and receiver are separate units. The target breaks the beam traveling between them. This provides the longest range and highest reliability, excellent for small objects or long paths.
Photoelectric sensors offer the longest sensing distances of the common proximity detection technologies and excel at detecting diverse objects regardless of material composition, color, or surface texture (though these factors can influence performance).
Why Industry Relies on Proximity Sensors: Core Applications
The impact of these small devices is vast, underpinning countless critical functions:
- Object Detection & Counting: Is the part present? Has the pallet arrived? How many bottles passed? Proximity sensors provide the fundamental “yes/no” signal for position verification and inventory tracking. This is the bedrock of automated process control.
- Positioning & End-of-Travel: Verifying a cylinder is fully extended or retracted, confirming a door is closed, checking a machine guard is in place. Position feedback ensures components are where they need to be for safe and correct operation.
- Speed Monitoring: Counting gear teeth or observing markers on a rotating shaft allows proximity sensors to monitor rotational speed (RPM) for process control and condition monitoring.
- Machine Safety: Fail-safe proximity sensors are integral parts of safety circuits, confirming guard doors are securely closed before dangerous machinery can operate, preventing catastrophic accidents. This application demands specialized, high-reliability sensors meeting stringent safety standards (e.g., SIL, PL).
- Level Control: Capacitive sensors are frequently deployed to detect high/low material levels in tanks, silos, and hoppers, triggering alarms or controlling filling processes.
- Discrimination: Detecting different types of materials (e.g., metal vs. plastic lids) based on how they interact with the sensor field.
Choosing the Right Guardian: Key Selection Factors
Selecting the optimal industrial proximity sensor isn’t guesswork. Critical considerations include:
- Target Material: Is it metal, plastic, liquid, or something else? This directly dictates whether inductive, capacitive, or photoelectric technology is suitable.
- Sensing Distance (Range): How far away does the object need to be detected? Ensure the sensor’s nominal range accommodates installation constraints and provides sufficient margin. Operating too close to a sensor can be unreliable.
- Output Type: Does the control system require a simple Digital Output (PNP/NPN switching), Analog Output (4-20mA, 0-10V for continuous distance measurement), or a specialized IO-Link connection for advanced diagnostics and parameterization?
- Environment: Will it face washdown conditions, extreme temperatures, heavy vibration, sprays of cutting oil, or metal debris? The sensor’s Ingress Protection (IP) rating, construction material (e.g., stainless steel), and technology resistance (e.g., inductive sensors resisting dirt) are paramount. Robustness is non-negotiable in harsh industrial settings.
- Mounting & Size: Space constraints often dictate compact form factors. Flush versus non-flush mounting options for inductive sensors also affect sensing range and installation flexibility.
- Performance Needs: Response time (critical for high-speed lines), repeatability (consistent detection under the same conditions), and switching frequency capabilities.
- Connectivity: From simple cable connections to quick-disconnect M12 plugs and advanced IO-Link communication enabling predictive maintenance data collection and remote configuration.
The Future is Sensing: Trends Shaping Proximity Sensors
Industrial proximity sensors continue to evolve:
- IO-Link Integration: This standardized point-to-point communication protocol is revolutionizing sensor connectivity. IO-Link proximity sensors provide far more than a simple ON/OFF signal. They offer diagnostic data (operating hours, temperature, signal strength), allow remote parameter changes (sensitivity, output mode), and simplify predictive maintenance by flagging potential issues before they cause downtime. This is a massive leap towards Industry 4.0 and Smart Factory goals.
- Enhanced Miniaturization: Demand for ever-smaller sensors continues, allowing installation in highly confined spaces within modern, compact machinery.
- Increased Intelligence at the Edge: Basic processing capabilities are moving closer to the sensor itself, enabling local decision-making and filtering to provide cleaner signals to the control system.
- Improved Environmental Resistance: Materials science advances are pushing the boundaries for sensors operating in extreme temperatures or corrosive chemical environments.
Conclusion: An Indispensable Force
From the simplest presence check to complex machine safety systems