magnetic distance sensor
- time:2025-07-05 02:48:49
- Нажмите:0
Magnetic Distance Sensors: The Non-Contact Measurement Technology Revolutionizing Precision
Imagine measuring the precise gap within a complex machine, the minute movements of a robotic arm, or the level of fluid in a sealed tank – all without physically touching anything. This isn’t science fiction; it’s the everyday reality enabled by magnetic distance sensors. These powerful devices harness the fundamental properties of magnetic fields to provide accurate, reliable, and non-intrusive distance and position measurements across countless industries.
What is a Magnetic Distance Sensor?
At its core, a magnetic distance sensor is an electronic device designed to detect the presence, distance, or position of a target object by sensing changes in a magnetic field. Unlike tactile methods requiring direct contact, these sensors operate entirely remotely. They typically consist of two main components:
- A Sensor Element: This is the heart of the device, containing the technology that detects and translates magnetic field variations into an electrical signal (e.g., Hall effect element, magnetoresistive element, coil).
- A Magnetic Target: An object (often a simple permanent magnet) attached to the item whose position or movement needs measuring. The sensor tracks changes in the magnetic field generated by this target.
How Do Magnetic Distance Sensors Work? The Core Principles
The working principle hinges on the relationship between the sensor element and the magnetic target:
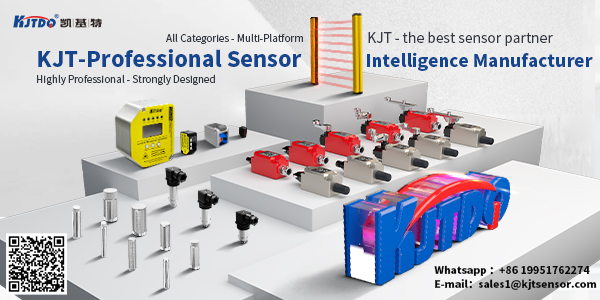
- Field Interaction: The magnetic target generates a static or dynamic magnetic field around it.
- Sensing Variation: As the target moves relative to the sensor, the characteristics of the magnetic field experienced by the sensor element change. This could be the field strength, its direction, or the time for a signal to propagate.
- Signal Conversion: The sensor element is specifically designed to be sensitive to these magnetic field changes. It converts the physical magnetic variation into a proportional electrical signal (voltage or current).
- Output Generation: The sensor’s internal electronics process this raw signal, often providing a standardized output. This could be analog (e.g., 4-20mA, 0-10V proportional to distance), digital (e.g., PWM, I2C, SPI), or a simple Переключить сигнал indicating a threshold has been crossed.
Key Types of Magnetic Distance Sensing Technology
Several distinct technologies fall under the umbrella of magnetic distance sensors, each with unique advantages:
- Hall Effect Sensors: Perhaps the most common type. These sensors utilize the Hall effect – when a current-carrying conductor is placed perpendicular to a magnetic field, a voltage (the Hall voltage) develops across it. The strength of this voltage is proportional to the magnetic field strength. They are robust, cost-effective, and offer good linearity for position sensing. Widely used for detecting proximity, rotation (via gear teeth), and simple linear displacement.
- Magnetostrictive Linear Position Sensors: Known for exceptional accuracy and long stroke lengths. These sensors rely on the magnetostrictive effect – certain ferromagnetic materials change shape slightly when exposed to a magnetic field. A position magnet moves along a waveguide tube. The sensor sends an electrical current pulse down the waveguide, creating a circular magnetic field. The interaction between this field and the position magnet’s field generates a torsional stress wave. The time-of-flight for this wave to return to the sensor head is measured with extreme precision, directly correlating to the magnet’s position. They offer non-contact, wear-free operation, high resolution, and excellent repeatability, making them ideal for hydraulic cylinders, industrial machinery, and process control.
- Inductive Proximity Sensors (Magnetic Target Variant): While often used with metallic targets, many specifically detect the presence of permanent magnets. An oscillator coil generates a high-frequency electromagnetic field. A nearby magnetic target (strongly ferromagnetic) induces eddy currents or significantly alters the field characteristics, which the sensor detects. They are extremely robust against dust, dirt, fluids, and vibration, commonly used for simple position detection limits (Домой or end position sensing).
- Magnetoresistive (MR) Sensors: Offer high sensitivity to magnetic field direction. MR sensors (including Anisotropic MR - AMR, Giant MR - GMR, Tunnel MR - TMR) change their electrical resistance based on the angle and strength of an applied magnetic field. They can detect incredibly subtle field changes and precise angular position but are often used in conjunction with magnets to derive linear displacement or speed information.
Critical Advantages Driving Adoption
The rise of magnetic distance sensors isn’t accidental; they offer compelling benefits:
- Non-Contact Operation: The key advantage. Eliminates wear, friction, and mechanical stress on both the sensor and target, ensuring long operational life and minimal maintenance.
- Robustness & Reliability: Typically sealed against environmental hazards like dust, oil, water, and chemicals. Immune to vibration and shock that plague contact-based systems.
- High Precision and Repeatability: Technologies like magnetostrictive sensors offer micron-level resolution and exceptional measurement consistency.
- Многогранность: Capable of functioning reliably in harsh environments (high temperature, pressure, vacuum, radiation) where optical or other contact sensors might fail.
- Cost-Effectiveness: Especially for Hall effect and inductive variants, providing reliable sensing at competitive prices.
- Simple Installation: Often only requires mounting the sensor body and attaching a magnet to the moving target.
Ubiquitous Applications: Where Magnetic Distance Sensors Shine
Their unique blend of features makes magnetic distance sensors indispensable across numerous sectors:
- Промышленная автоматизация: Monitoring cylinder piston position, valve stem travel, conveyor belt positioning, robotic arm articulation, press stroke control.
- Automotive: Throttle position sensing, suspension travel measurement, gear shift position, brake pedal position, clutch engagement, seat position memory.
- Medical Equipment: Precise control in imaging devices (MRI positioning systems often use MR sensors), surgical robotics, infusion pump mechanisms.
- Construction & Heavy Machinery: Boom extension/retraction, blade leveling, hydraulic actuator feedback in excavators, cranes, and bulldozers.
- Robotics: Providing critical feedback for joint angles, end-effector position, and collision detection.
- Аэрокосмическая деятельность: Control surface (aileron, rudder, flap) position feedback, landing gear status, actuator monitoring.
- Consumer Electronics: Lid/door open/close detection in laptops and appliances, screen position in convertible devices.
- Process Control & Level Sensing: Measuring fluid levels in tanks (using a float with an embedded magnet tracked by an external sensor), material level in silos.
Choosing the Right Magnetic Distance Sensor
Selecting the optimal sensor involves careful consideration:
- Measurement Range: How far does the target move?
- Required Accuracy & Resolution: How precise and fine-grained do the measurements need to be?
- Output Signal Type: Analog voltage/current, digital interface (SSI, PWM, I2C), or simple switch?
- Environmental Conditions: Temperature extremes, pressure, exposure to chemicals, moisture, or explosive atmospheres?
- Installation Constraints: Physical space limitations?
- Target Magnet: Size, strength, and mounting feasibility?
- Cost: Balancing performance needs with budget.
The Future of Non-Contact Sensing
Magnetic distance sensor technology continues to evolve. Advancements in materials science (like enhanced TMR elements) are pushing the boundaries of sensitivity and miniaturization. Integration of sophisticated signal processing and diagnostics directly into sensor electronics (*