ifm electronic proximity sensor
- time:2025-07-05 02:30:45
- Нажмите:0
Unlock Efficiency: How ifm Electronic Proximity Sensors Revolutionize Industrial Automation
Imagine an assembly line grinding to a halt because a simple part wasn’t detected, or production inconsistencies arising from unreliable positioning. In the high-stakes world of modern manufacturing and automation, these scenarios translate directly to lost time, money, and quality. Enter the unsung hero: the ifm electronic proximity sensor. Far more than just an “on/off” switch, these robust devices are critical components enabling precision, reliability, and efficiency across countless applications.
Understanding the Core: What Are ifm Electronic Proximity Sensors?
At their essence, ifm electronic proximity sensors are non-contact switching devices. They detect the presence or absence of an object within their specified sensing range without needing physical contact. This is achieved using various physical principles, primarily:
- Inductive Sensors: Detect metallic targets (ferrous and non-ferrous) by generating an electromagnetic field. When a metal object enters this field, it induces eddy currents, causing a change in the sensor’s oscillation that triggers the switching output. Ideal for harsh environments with dust, oil, or vibration.
- Capacitive Sensors: Detect virtually any material, including liquids, powders, plastics, wood, and glass, by sensing changes in capacitance caused by the object entering the sensor’s electrostatic field. Perfect for level detection in tanks or distinguishing between different materials.
- Magnetic Sensors: Specifically designed to detect permanent magnets. Often used for cylinder position feedback where magnets are embedded in piston rods.
The “electronic” aspect refers to the sophisticated circuitry within ifm sensors. This isn’t just basic switching; it involves advanced signal processing for noise immunity, temperature compensation for stable performance, and often integrated diagnostics.
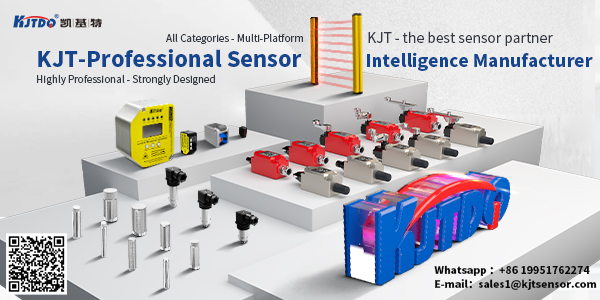
Why ifm Stands Out: Engineering Excellence for Demanding Environments
ifm has built a formidable reputation in industrial automation, and their proximity sensors exemplify this through several key differentiators:
- Uncompromising Durability and Reliability: Engineered to withstand industrial rigors. Many models feature robust metal housings (typically stainless steel or nickel-plated brass), high IP ratings (IP67, IP68, IP69K common) for resistance to dust, water jets, and harsh cleaning, and resilience against shock, vibration, and extreme temperatures. This translates to long service life and minimal unplanned downtime.
- Precision and Performance: ifm sensors offer excellent sensing ranges relative to their size, high repeat accuracy, and fast switching frequencies. This ensures reliable detection even under demanding conditions with fast-moving objects.
- Diverse and Specialized Portfolio: Beyond standard inductive and capacitive sensors, ifm offers specialized variants like high-temperature sensors, weld-field immune versions, food-grade designs, sensors for ATEX zones, and miniature models for space-constrained applications. This breadth ensures the right tool for virtually any job.
- Advanced Diagnostics and Connectivity: Modern ifm sensors often feature IO-Link capability. This revolutionary point-to-point communication adds a powerful layer. Sensors can transmit diagnostic data (e.g., operating hours, temperature warnings, signal quality, switch point drift), enable remote parameterization (like setting sensing distance or output behavior), and provide detailed process values beyond simple on/off signals. This facilitates predictive maintenance and simplifies integration into Industry 4.0 frameworks. Knowing a sensor is degrading before it fails is a game-changer.
- Ease of Use and Integration: Features like visible switching status LEDs, intuitive mounting options (threaded barrels like M8, M12, M18; flat designs; slots), and standardized cabling/connectors simplify installation and troubleshooting. Their compatibility with major PLC systems is seamless.
Key Applications: Where ifm Proximity Sensors Drive Value
The versatility of ifm electronic proximity sensors makes them ubiquitous:
- Position and End Position Detection: Confirming the presence, absence, or precise location of parts on conveyors, pallets, slides, or within machines. Vital for sequence control.
- Object Counting: Accurately tallying products on a line, packages on a conveyor, or components in an assembly process.
- Level Monitoring: Capacitive sensors reliably detect the fill level of liquids, granulates, or powders in tanks, silos, and hoppers. Critical for process control and avoiding overflow or run-dry situations.
- Metal Detection: Inductive sensors ensure only metallic parts proceed to specific machining stations or reject non-metallic contaminants.
- Speed Monitoring: Combined with ferrous targets, proximity sensors act as cost-effective rotary speed sensors for motors, gearboxes, or conveyors.
- Safety Functions: Used as part of safety circuits for door monitoring (ensuring guards are closed) or position verification before hazardous operations commence. (Note: Typically used in conjunction with certified safety relays/controllers).
- Cylinder Position Feedback: Magnetic sensors are the standard for detecting the extended/retracted position of pneumatic and hydraulic cylinders.
Beyond Switching: The Value Proposition of ifm
Investing in ifm electronic proximity sensors delivers tangible benefits:
- Maximized Machine Uptime: Their legendary reliability minimizes sensor-related stoppages.
- Enhanced Process Quality: Consistent and accurate object detection ensures processes run as intended, reducing errors and scrap.
- Reduced Maintenance Costs: Durability equals fewer replacements. Predictive maintenance enabled by IO-Link diagnostics allows for planned servicing, avoiding catastrophic failures and production losses.
- Improved Operational Efficiency: Faster cycle times enabled by high-speed sensing and reliable counting contribute to higher throughput.
- Simplified Engineering and Installation: Standardized designs, clear documentation, and intuitive features speed up machine builds and retrofits.
- Future-Proofing: IO-Link connectivity positions facilities for evolving Industry 4.0 / Smart Factory requirements, enhancing visibility and control.
From controlling high-speed packaging lines to ensuring precise robotic welding and monitoring critical fluid levels, ifm electronic proximity sensors are fundamental building blocks of modern automation. Their blend of ruggedness, precision, advanced features like IO-Link, and unwavering reliability makes them not just components, but strategic assets for engineers and plant managers striving for peak operational efficiency and competitive advantage. Understanding their capabilities and selecting the right ifm sensor for the application is a critical step towards building more resilient, productive, and intelligent industrial systems.