m18 proximity sensor
- time:2025-07-05 02:12:41
- Нажмите:0
M18 Proximity Sensors: The Compact Powerhouses Revolutionizing Industrial Automation
Imagine a factory humming with precision. Robotic arms weld with micron accuracy, conveyor belts move products flawlessly, and machines start and stop exactly when needed. Behind this seamless orchestration often lie unsung heroes: M18 proximity sensors. These compact, rugged devices are fundamental to modern industrial automation, providing the critical “eyes” that detect the presence or absence of metallic objects without physical contact. Understanding their role, capabilities, and applications is key to optimizing efficiency and reliability in countless processes.
What Makes the M18 Form Factor So Special?
The “M18” designation refers explicitly to the sensor’s threaded barrel diameter – 18 millimeters. This standardized size strikes a remarkable balance between compactness and robust performance. Compared to larger sensors (like M30), M18 proximity sensors fit effortlessly into tight spaces on machinery, robots, and assembly lines where real estate is precious. Yet, they offer significantly longer sensing ranges and greater physical resilience than their smaller M12 or M8 counterparts. This ideal blend of size, range, and durability explains why the M18 format is arguably the most popular industrial inductive proximity sensor worldwide.
Core Working Principle: Inductive Sensing
The vast majority of M18 sensors operate on the inductive sensing principle. Here’s the elegant science behind it:
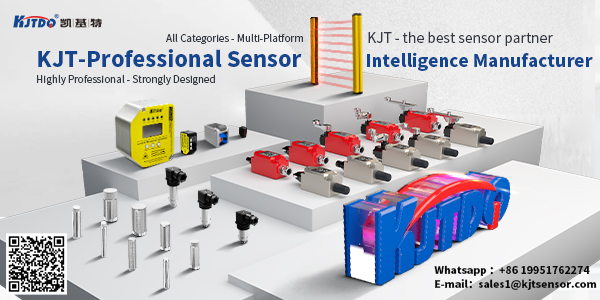
- Internal Oscillator: The sensor contains a coil energized by a high-frequency oscillator, creating an electromagnetic field at its active face.
- Field Disturbance: When a ferrous (iron-based) or non-ferrous (like aluminum, brass, copper) metal target enters this field, it induces eddy currents within the metal itself.
- Energy Dampening: These eddy currents draw energy from the oscillator circuit, causing its amplitude to decrease.
- Signal Processing: An internal circuit detects this reduction in oscillation amplitude.
- Output Switch: Once the amplitude drop surpasses a predefined threshold (corresponding to the sensor’s specified sensing range), the sensor’s output state switches – typically turning a solid-state NPN or PNP transistor ON or OFF.
This contactless detection method is crucial. It eliminates mechanical wear and tear, ensuring a long operational life measured in millions of cycles, far exceeding mechanical limit switches.
Key Specifications and Features: What Defines Performance?
Selecting the right M18 proximity sensor hinges on understanding key specifications:
- Sensing Range (Sn): The nominal distance at which the sensor reliably detects a standard target (usually mild steel). For M18 inductive sensors, this typically ranges from 2mm to 8mm, depending on the specific model and whether it features a shielded or unshielded design. Unshielded types offer slightly longer ranges but require more surrounding clearance, while shielded types can be flush-mounted in metal.
- Output Type: Primarily 3-wire DC versions dominate:
- NPN (Sinking): Outputs the negative (0V) line when active.
- PNP (Sourcing): Outputs the positive voltage (e.g., +24V DC) when active.
- Normally Open (NO) / Normally Closed (NC): Refers to the output’s electrical state when Нет! target is present.
- Housing Material: Нержавеющая сталь (particularly 303, 304, or 316 variants) is the gold standard for corrosion and chemical resistance. Nickel-plated brass is a common cost-effective option for less demanding environments.
- IP Rating: Ingress Protection ratings like IP67 or IP69K are crucial. IP67 ensures protection against dust ingress and temporary immersion in water (1 meter for 30 mins). IP69K offers protection against high-pressure, high-temperature water jets, essential for harsh washdowns in food & beverage or pharmaceutical settings.
- Switching Frequency: Indicates how rapidly the sensor can detect passing targets. For M18s, common frequencies range from 500 Hz to 5 kHz, suitable for high-speed counting or position verification tasks.
- Voltage Range: Most operate on standard industrial DC voltages like 10-30V DC. AC versions are less common.
Where Do M18 Proximity Sensors Shine? Applications Galore
The versatility of M18 inductive proximity sensors makes them indispensable across virtually every industrial sector:
- Machine Tooling: Detecting tool presence/absence, confirming chuck clamping, monitoring part fixtures, and controlling coolant flow.
- Material Handling & Packaging: Counting bottles/cans on conveyors, verifying box flaps are closed, detecting pallet positions, ensuring product transfer gates are clear.
- Robotics: End-of-arm tooling confirmation (Is the gripper holding a part?), verifying home positions, and providing collision detection feedback.
- Automotive Assembly: Precise positioning verification of components on the line, detecting pistons or shafts in engines, and ensuring robots pick the correct parts.
- Food & Beverage / Pharmaceutical: Made from food-grade stainless steel (e.g., 316L), IP69K-rated M18 sensors monitor fill levels, detect metal lids/caps, track containers on conveyors, and ensure machinery guards are closed, handling rigorous cleaning protocols.
- General Manufacturing: Monitoring cylinder piston positions, detecting gear teeth rotation for speed measurement, verifying part presence before machining, and controlling automated doors or slides.
Installation and Mounting: Precision Matters
While robust, proper installation maximizes performance and longevity:
- Secure Mounting: Use the M18 threaded barrel to screw securely into a tapped hole, matching the thread pitch (commonly M18x1.0 or M18x1.5). Avoid overtightening.
- Shielded vs. Unshielded: Shielded sensors (recognizable by a flush sensing face) can be mounted flush with or within metal structures. Unshielded sensors (sensing face protruding slightly) require specific clearance around the sides to function correctly – consult datasheets.
- Target Material & Size: Standard sensing ranges are specified for mild steel. Detection ranges for non-ferrous metals (aluminum, brass, copper) are typically reduced – often 60-70% less than the rated Sn for steel. Ensure the target is large enough to consistently enter the sensor’s detection field. Small, fast-moving targets require careful consideration.
- Environmental Factors: Position sensors away from extreme heat sources, strong magnetic fields, welding currents, or heavy vibration whenever possible. Ensure electrical connections are clean, secure, and follow wiring diagrams precisely, observing polarity for DC types.
Choosing the Right M18 Sensor for Your Application
Consider these critical factors:
- Target Material: Ferrous (use standard)? Non-ferrous? (Requires a non-ferrous specific model or accounts for reduced range).
- Required Sensing Distance: Factor in installation constraints and target size.
- Operating Environment: Harsh conditions? Washdown? (Dictates IP rating and housing material - stainless steel, IP69K is king for harshness).
- Electrical Interface: What PLC or controller are you using? (NPN vs. PNP compatibility).
- Output Configuration: Normally Open (NO) or Normally Closed (NC)? Does your logic require a signal on presence or absence?
- Special Requirements: High switching speeds? Analog output needed? Extended temperature range? Factor size constraints (M18 is compact, but double-check).
The Future is Sensing: Advancements and Reliability
M18 proximity sensors continue to evolve. We see trends toward:
- IO-Link Integration: Adding this smart communication protocol transforms simple sensors into intelligent devices, enabling remote configuration, diagnostics, parameterization, and process data monitoring – significantly reducing downtime.
- Enhanced Durability: Continuous improvements in sealing technologies and housing materials extend life expectancy in ever-more demanding environments