festo inductive sensor
- time:2025-07-05 01:24:28
- Нажмите:0
Festo Inductive Sensors: The Unseen Guardians of Reliable Automation
In the intricate dance of modern manufacturing and automation, where precision and uptime are paramount, countless components work tirelessly behind the scenes. Among these unsung heroes, Festo inductive sensors stand out as fundamental pillars of reliability. These robust yet sophisticated devices are the silent sentinels, ensuring objects are detected, positions are verified, and processes flow seamlessly – often in the harshest industrial environments imaginable. Understanding their capabilities reveals why they are a cornerstone technology, trusted globally in countless applications demanding unwavering performance.
The Essence of Contactless Detection: How Festo Inductive Sensors Operate
At their core, Festo inductive proximity sensors operate on a beautifully simple electromagnetic principle. They generate a high-frequency oscillating electromagnetic field from their active face. When a metallic target – be it steel, aluminum, brass, or others – enters this field, it induces tiny electrical currents (eddy currents) within the target. These eddy currents absorb energy from the sensor’s oscillating field. The sensor’s internal electronics are finely tuned to detect this energy loss. Once the threshold loss caused by a specific target material and distance is reached, the sensor’s output state switches. This all happens without any physical contact, making them inherently maintenance-free and exceptionally durable.
Why Festo Stands Apart: Key Advantages in Industrial Settings
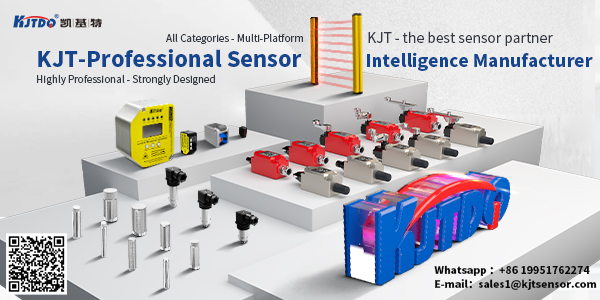
Festo has built a formidable reputation in industrial automation, and their inductive sensor range embodies this excellence. Here’s what makes them a preferred choice:
- Exceptional Robustness & Longevity: Engineered for demanding industrial realities, Festo sensors boast high ingress protection ratings (like IP67, IP68, IP69K), shielding them from dust, coolants, oils, and even high-pressure washdowns common in food processing or pharmaceutical production. Their resistance to shock, vibration, and electromagnetic interference (EMI) ensures reliable operation amidst machinery noise and movement.
- Maintenance-Free Operation: The fundamental contactless sensing principle eliminates mechanical wear and tear associated with limit switches. This translates directly to reduced downtime and lower total cost of ownership (TCO) – a critical factor in high-volume production environments.
- High Switching Frequency & Precision: Modern Festo inductive sensors offer rapid response times and high switching frequencies. This allows for detecting small, fast-moving objects or verifying positions precisely on high-speed assembly lines or packaging machinery, crucial for maintaining throughput and quality.
- Reliability Across Materials & Environments: While optimized for metals, Festo provides sensors tailored for specific materials (e.g., ferrous or non-ferrous metals, even with varying switching distances). Certain variants are specifically hardened to withstand extreme environments, including proximity to welding sparks or powerful magnetic fields found near large motors.
- Design Diversity & Integration Ease: Festo offers an extensive portfolio covering standard tubular sensors (M5, M8, M12, M18, M30), compact and flat designs, and specialized rectangular formats. This ensures the right fit for any spatial constraint. Features like factory-set or teach-in switching points, IO-Link compatibility for advanced diagnostics and parameterization, and diverse electrical connections (cable or connector variants) simplify integration into diverse control systems.
- Uncompromising Quality & Consistency: As with all Festo components, inductive sensors are manufactured to stringent quality standards. This guarantees consistent performance, batch-to-batch reliability, and adherence to industry certifications, providing engineers with peace of mind.
Indispensable Across Industries: Core Applications
The robustness and reliability of Festo inductive sensors make them ubiquitous in automation:
- Position Verification: Confirming the presence or absence of machine parts, end stops of cylinders (like Festo’s own pneumatic drives), pallet locations, and tool positioning in CNC machines. Key for sequential control logic.
- Object Counting: Tracking parts on conveyors, monitoring production volumes, and ensuring feed systems are stocked reliably. Their high switching frequency enables counting fast-moving items.
- End-of-Arm Tooling (EOAT): Essential on robots for confirming gripper closure, part acquisition, and tool changes.
- Level Detection: Monitoring metal levels in bins, hoppers, or tanks (e.g., metal slugs, chips).
- Safety & Monitoring: Used as part of safety interlock systems (though not primary safety sensors) to confirm guards are closed or machine components are in a safe state before cycle start. Predictive maintenance systems leverage IO-Link enabled sensors for early wear detection in components like bearings or chains.
- Material Handling & Packaging: Detecting metal components on conveyors, verifying case tapers, and controlling filling levels in metal containers.
- Automotive, Food & Beverage, Electronics: Found on virtually every assembly line, handling system, and processing machine where reliable, non-contact metal detection is needed – especially in environments requiring washdown-rated IP69K sensors.
Selecting the Right Festo Inductive Sensor: Key Considerations
Navigating Festo’s extensive inductive sensor range is straightforward when focusing on core parameters:
- Housing Format: Tubular (choose diameter), rectangular, or flat for tight spaces?
- Sensing Distance: Required nominal switching distance (Sn) based on target size and mounting constraints. Factor in real-world derating for non-ferrous targets.
- Target Material: Ferrous steel, non-ferrous (aluminum, brass, copper), or stainless steel? This significantly impacts effective sensing range.
- Electrical Characteristics: Required operating voltage (e.g., 10-30V DC), output type (PNP/NPN, NO/NC), and current rating.
- Environmental Demands: IP rating (IP67 for general factory, IP68/IP69K for submersion/washdown), temperature range, resistance to chemicals or welding sparks?
- Special Features: IO-Link for Industry 4.0 connectivity, AS-Interface compatibility, increased switching distance variants, high-temperature models, or analog output for position measurement?
The Foundation of Unseen Reliability
From the relentless pace of an automotive assembly line to the hygienic demands of a dairy plant, Festo inductive sensors provide the fundamental detection capabilities that keep modern automation running smoothly, safely, and efficiently. Their combination of robust construction, unwavering contactless operation, diverse design options, and the trusted quality of the Festo brand solidifies their position as indispensable workhorses. They are more than just sensors; they are reliable partners ensuring millions of detection cycles happen flawlessly, day in and day out, forming the resilient backbone of industrial automation. Understanding their capabilities empowers engineers to design systems built on a foundation of proven reliability.