конденсаторный датчик ближнего действия
- time:2025-07-05 00:12:26
- Нажмите:0
Sensing the Unseen: How Capacitive Proximity Sensors Revolutionize Non-Contact Detection
Ever wondered how vending machines magically dispense drinks when you wave your hand, or how automated assembly lines flawlessly detect clear bottles whizzing past? Often invisible to the eye, capacitive proximity sensors are the silent workhorses enabling this touchless magic. Unlike their mechanical or optical counterparts, these versatile sensors operate on a fundamental principle of physics, detecting objects without physical contact through subtle changes in an electrical field. Understanding their operation and advantages unlocks insights into countless modern automated processes.
The Science Behind the Sensing: It’s All About Fields
At the heart of every конденсаторный датчик приближения lies a simple concept: an oscillator circuit generating an electromagnetic field emanating from the sensor’s active surface. This field behaves much like the invisible field surrounding a capacitor – hence the name. When an object enters this detection zone, it alters the sensor’s dielectric constant or capacitance. Essentially, the object influences how the electrical field propagates through space. This change is minutely measured by the sensor’s circuitry. If this change exceeds a predefined threshold – the sensing distance – the sensor’s output state switches, signaling the presence of the object. Crucially, non-contact detection means no wear and tear from physical interaction.
What Can They “See”? Beyond Metal Detection
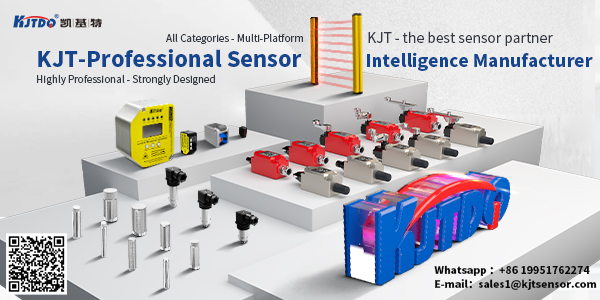
A key strength of конденсаторный датчик is their remarkable versatility detecting materials. Unlike inductive proximity sensors, which primarily detect metals, capacitive variants excel with a much broader range:
- Conductive Materials: Metals (similar to inductive sensors) are easily detected due to their strong influence on the electric field.
- Non-Conductive Materials: This is where they truly shine. Plastics, glass, wood, cardboard, textiles, powders, granules, liquids (including water and oil), and even biological materials (like your hand!) can be reliably sensed. The sensor detects the material’s dielectric constant – a measure of how well it concentrates electrostatic lines of flux compared to air. Materials with higher dielectric constants (like water) are generally easier to detect at greater distances than those with lower constants (like dry wood).
Flood vs. Focused: Shaping the Field
Capacitive sensors offer different field patterns to suit various application needs:
- Flood or Unshielded Mode: Sensors designed for this mode allow the electric field to radiate omnidirectionally from the front and sides. This offers a larger detection zone but makes them susceptible to false triggering from nearby objects, liquids, or even mounting surfaces. Careful installation is critical.
- Focused or Shielded Mode: These sensors incorporate an internal grounded shielding ring (often visible as a metal band near the sensing face). This effectively focuses the electric field directly forward. Shielded capacitive sensors are far less susceptible to side interference, making them ideal for flush mounting in metal, detecting objects in confined spaces, or distinguishing targets in crowded environments. They generally offer a shorter but more precise sensing range than unshielded types.
Why Choose Capacitive? Key Advantages for Robust Operation
The unique operating principle translates into several compelling advantages:
- Material Versatility: As discussed, their ability to detect both conductors and insulators is unmatched by other common proximity sensor types.
- Non-Contact Detection: Eliminates mechanical wear, guaranteeing long service life and reducing maintenance costs. Failure prevention is inherent.
- Contaminant Immunity: They can reliably detect objects through thin-walled plastic or glass containers, and are generally unaffected by dust, dirt, moisture, or oils (unless these substances drastically alter the dielectric constant near the sensor face). This is vital in harsh industrial environments like food processing or chemical plants.
- Liquid Level Detection: Their ability to sense most liquids through container walls makes them a popular, cost-effective choice for tank level control of water, chemicals, oils, and granular substances.
- Solid Object Presence: Perfect for verifying the presence of items on conveyors, in bins or hoppers, or during automated assembly – regardless of material (boxes, bottles, wood blocks, etc.).
- Simple Installation: Often require minimal setup beyond adjusting the sensitivity threshold and securing the sensor.
Key Applications: Where Touchless Detection Matters Most
Capacitive proximity sensors find critical applications across diverse sectors:
- Packaging & Filling: Detecting plastic/glass bottles, verifying filled levels in containers (through walls), checking case/box presence.
- Food & Beverage: Level sensing in tanks holding liquids, pastes, or grains; detecting packaged products on lines; monitoring ingredient bins. Their contaminant immunity is crucial here.
- Перевозка материалов: Verifying the presence of pallets, boxes, sacks, or other non-metallic loads on conveyors or at pick points.
- Wood & Paper Industry: Detecting logs, lumber, paper rolls, cardboard stacks.
- Chemical & Pharmaceutical: Liquid level control in tanks (often corrosive); detecting plastic vials or containers.
- Automotive Assembly: Verifying the presence of plastic bumpers, dash components, fluid reservoirs.
- DIY & Consumer Electronics: Touch interfaces (like those using projected capacitive touch screens), simple presence detection in appliances.
Factors to Consider for Optimal Performance: Sensing Range and More
Selecting the right capacitive sensor involves understanding key parameters:
- Sensing Distance (Sn): The nominal operating distance specified by the manufacturer for a standard target (usually steel). Crucially, the effective range for non-metallic objects depends heavily on their dielectric constant. Water (εr ~80) might be detectable at near Sn, while dry wood (εr ~2-6) might only be detectable at a fraction of Sn. Always consult sensor specifications for material-specific correction factors.
- Target Size: Smaller targets require closer proximity for reliable detection, especially non-conductive ones. The sensor must “see” enough of the target material to cause sufficient capacitance change.
- Environment: Temperature extremes, humidity, and electrical noise can affect performance. Choose sensors rated for the specific harsh industrial environments where they will operate. Avoid mounting near strong electromagnetic fields.
- Mounting: Ensure correct installation (flushed or non-flushed) as per the sensor’s design (shielded/unshielded) to prevent false triggers or reduced range. Proper shielding selection is paramount.
- Sensitivity Adjustment: Most capacitive sensors feature a potentiometer. Fine-tuning the sensitivity allows optimizing detection for specific materials and ignoring background interference (like sensing liquid inside a plastic bottle while ignoring the bottle itself). Calibration in the actual installation is often necessary. Avoid setting it unnecessarily high to prevent instability.