аналоговый индуктивный датчик
- time:2025-07-05 00:00:07
- Нажмите:0
Analog Inductive Sensors Explained: Precision Measurement Beyond On/Off Detection
In the intricate dance of automation and precise control, simply knowing if something is or isn’t present often isn’t enough. What if you need to know exactly how far away a metal object is, measure a tiny gap with high repeatability, or continuously monitor the position of a piston within a cylinder? This is where the аналоговый индуктивный датчик steps out of the shadow of its ubiquitous digital cousin, transitioning from a simple switch to a sophisticated measurement device, unlocking a world of nuanced process control.
Unlike their digital counterparts that offer a binary “on/off” signal when a metal target enters their sensing range, analog inductive sensors provide a continuous output signal proportional to the distance to the target. This output is typically a voltage (e.g., 0-10V) or a current (e.g., 4-20mA) that changes linearly (or sometimes non-linearly, depending on design) as the target moves within its operational range. This fundamental characteristic transforms them from mere presence detectors into powerful tools for non-contact position sensing and displacement measurement.
How Do They Sense & Measure? The Electromagnetic Heart
The core operating principle leverages electromagnetic induction, shared with digital sensors. Here’s a quick refresher on what makes them tick:
- Generating the Field: The sensor contains a coil wound around a ferrite core, forming an oscillator circuit. When powered, this circuit generates a high-frequency alternating magnetic field at the sensor’s active face.
- Eddy Current Interaction: When a conductive (usually metallic) target enters this magnetic field, eddy currents are induced on the target’s surface. These swirling currents oppose the magnetic field generated by the sensor coil.
- Damping the Oscillation: The energy loss caused by the eddy currents effectively damps the oscillation within the sensor coil circuit. The strength of this damping effect is directly proportional to the distance between the sensor face and the target.
- Measuring the Change: While a digital sensor only detects if this damping exceeds a threshold (triggering a switch), an аналоговый индуктивный датчик continuously monitors the degree of damping or the resulting change in the oscillator’s amplitude and/or frequency. This change is processed internally.
- Providing the Analog Output: The internal electronics convert the measured change in the electromagnetic field into a standardized, continuously variable analog output signal (voltage or current). This signal corresponds precisely to the target’s distance within the calibrated range.
This process allows for high-resolution, non-contact measurement without physical wear, making them ideal for demanding industrial environments.
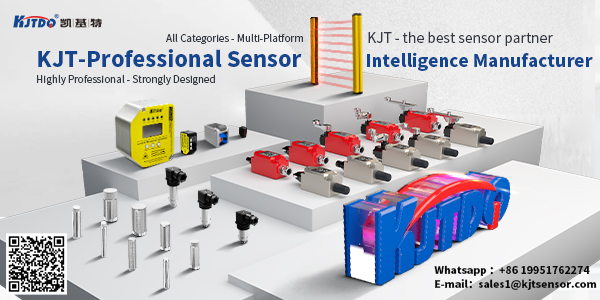
Why Choose Analog Inductive Sensors? Key Advantages
The unique capabilities of these sensors offer compelling benefits:
- Continuous Position Feedback: Granting insight into the exact location or displacement of a target, not just its presence/absence. This is crucial for processes like controlling valve positions, monitoring piston stroke, or measuring shaft runout.
- High Resolution and Repeatability: Capable of detecting minute changes in distance (micrometers or thousandths of an inch, depending on size and range), providing extremely precise measurement data with excellent consistency.
- Robustness in Harsh Environments: Inherently resistant to dust, dirt, oil, coolants, and vibration. Their sealed designs offer high IP ratings (like IP67 or IP69K), making them workhorses in manufacturing, hydraulics, automotive testing, and heavy machinery.
- Non-Contact Operation: Eliminates mechanical wear and tear on both the sensor and the target, ensuring long-term reliability and reducing maintenance costs.
- Immunity to Surface Conditions: Unlike optical sensors, they are largely unaffected by target surface color, transparency, or the presence of contaminants like oil film or dust (as long as it doesn’t interfere with the magnetic field), providing reliable position sensing even in dirty settings.
- Temperature Stability: Modern designs exhibit excellent stability over a wide operating temperature range, crucial for consistent performance in fluctuating industrial environments.
- Simple Integration: The standardized analog outputs (0-10V, 4-20mA) are readily compatible with PLCs (Programmable Logic Controllers), data acquisition systems, and industrial controllers.
Understanding Range, Linearity, and Outputs
Selecting the right аналоговый индуктивный датчик requires understanding key specifications:
- Sensing Range (Sr): The nominal distance within which the sensor can reliably detect the standard target (usually a square of mild steel, 1mm thick, side length equal to the sensor face diameter or 3x Sr). Crucially, the effective measurement range might be a portion of the sensing range where the output signal is linear.
- Linearity: This defines how closely the output signal change matches the actual distance change over the specified measurement range. A higher specification (e.g.,
- Output Signal: Choose based on your control system requirements. Voltage outputs (e.g., 0-10V) are common and simple for shorter cable runs. Current outputs (4-20mA) are highly resistant to electrical noise and voltage drop over long distances, making them ideal for factory floors. Ratiometric outputs (e.g., proportional to supply voltage) offer inherent noise immunity.
- Resolution: The smallest detectable change in distance the sensor can reliably report.
- Repeatability: The ability to report the same position value consistently under identical conditions. Typically excellent for inductive sensors.
Interpreting the Analog Output: The Measurement Value
The true power lies in converting the analog signal into meaningful position sensing data. For example:
- A sensor with a 0-10V output over a 5mm measurement range might report:
- 0V = Target at 0mm (nominal face contact)
- 5V = Target at 2.5mm
- 10V = Target at 5mm
- A sensor with 4-20mA output over a 10mm range might report:
- 4mA = Target at 10mm (furthest point)
- 12mA = Target at 5mm
- 20mA = Target at 0mm (closest point)
The receiving device (PLC, controller) is programmed with the sensor’s specific scaling to translate the received voltage or current value directly into distance or position units.
Real-World Applications: Where Precision Matters
The ability to provide continuous distance measurement makes analog inductive sensors indispensable in numerous industries:
- Machine Tooling: Monitoring spindle position, tool wear compensation (measuring tool projection), workpiece positioning, chuck jaw position.
- Hydraulics & Pneumatics: Providing precise feedback on piston position within cylinders, enabling advanced motion control and verification. This is a core position sensing application.
- Automotive Manufacturing & Testing: Measuring suspension travel during testing, monitoring brake pedal position, verifying component assembly gaps.
- Перевозка материалов: Controlling the position of grippers, monitoring roll diameter changes on winders/unwinders, ensuring precise stacking heights.
- Robotics: Providing end-effector position feedback relative to a work surface or component.
- Presses & Stamping: Verifying die height, monitoring ram position for precise force application.
- Test & Measurement Equipment: Any application requiring non-contact, high-repeatability distance measurement of conductive targets.
By offering robust, reliable, and highly accurate non-contact position sensing in challenging environments, analog inductive sensors bridge the critical gap between simple object detection and sophisticated process control. Their continuous analog output opens doors to finer adjustments, real-time monitoring, and enhanced quality control that binary signals simply cannot provide, proving that sometimes, the most valuable