индукционный датчик ближнего действия
- time:2025-07-04 01:36:34
- Нажмите:0
Inductive Prox Sensors: The Unseen Guardians of Industrial Efficiency
Imagine a world where machines operate flawlessly, navigating complex tasks without physical contact. Where position is sensed instantly, production lines run smoothly, and equipment is protected from collisions. This silent orchestration relies heavily on a workhorse of automation: the индукционный датчик приближения. Often unnoticed but fundamentally indispensable, these robust electronic eyes form the backbone of modern manufacturing and control systems. Understanding their function, strengths, and applications reveals why they remain the most widely used type of non-contact sensor globally.
At its core, an индукционный датчик приближения (frequently shortened to “inductive prox sensor” or “prox switch”) is a non-contact device specifically designed to detect the presence or absence of metallic objects. Unlike mechanical switches requiring physical touch, they operate using the principles of electromagnetic induction, allowing them to sense targets through air gaps – a key advantage in harsh environments.
The Heart of Operation: Electromagnetic Induction
The magic lies within a carefully designed internal circuit centered around a coil wound around a ferrite core. Here’s the simplified breakdown:
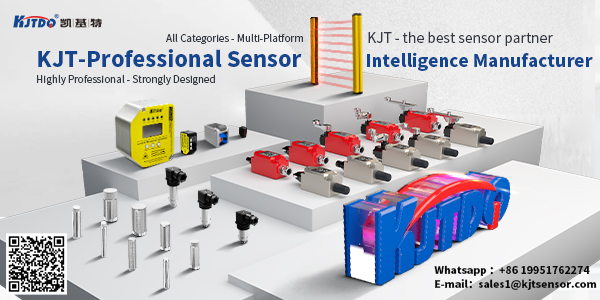
- The Oscillator: The sensor generates a high-frequency alternating magnetic field radiating outward from the face of the sensor coil. This is the sensor’s active zone.
- The Eddy Current Effect: When a conductive metal target (steel, aluminum, brass, copper, etc.) enters this magnetic field, it induces swirling electrical currents within the target material. These are known as eddy currents.
- Energy Drain and Damping: The generation of eddy currents consumes energy from the sensor’s oscillator. This energy loss damps or reduces the amplitude of the high-frequency oscillation.
- The Detector Circuit: The sensor constantly monitors the amplitude of its internal oscillation. A significant reduction in this amplitude indicates the presence of a metal target within its sensing range.
- Output Switching: The detector circuit triggers a solid-state electronic switch (like a transistor) to change state. This typically means switching its output load (e.g., a PLC input, relay, or indicator lamp) from OFF to ON (Normally Open, NO) or ON to OFF (Normally Closed, NC), signaling the target’s detection.
Key Characteristics Defining Inductive Prox Sensors
Their popularity stems from several inherent advantages:
- Ruggedness and Longevity: With no moving parts to wear out, and typically encapsulated in robust metal (stainless steel or nickel-plated brass) or industrial-grade plastic housings, they are exceptionally durable and resistant to impact, vibration, shock, and environmental contaminants like dust, oil, and coolants. Maintenance requirements are minimal.
- Non-Contact Sensing: By requiring no physical contact with the target, they eliminate mechanical wear on both the sensor and the target itself. This translates to extended operational life and higher reliability.
- High Switching Speed: Capable of detecting targets thousands of times per second, inductive sensors easily keep pace with fast-moving machinery, making them ideal for high-speed counting, positioning, and automation tasks where mechanical switches would falter.
- Insensitivity to Surface Conditions: They detect the metal itself, not surface characteristics like color, transparency, or the presence of oil or dust (unlike optical sensors). This predictability is crucial in dirty industrial settings.
- Resistance to Environmental Factors: Sealed designs offer excellent resistance against moisture, water jets, cutting fluids, and chemical splashes (varying by specific IP rating). Their operation is generally unaffected by ambient light conditions.
- Variety of Form Factors and Outputs: Available in diverse shapes (cylindrical barrels, rectangular blocks, ring-shaped for thread detection) and sizes to fit countless mounting constraints. Output options usually include DC versions (NPN/PNP transistors) operating at common voltages (10-30V DC) and AC versions.
- Cost-Effectiveness: Their robust design, long lifespan, and high reliability make them an extremely economical choice per switching cycle over the long term.
Understanding Sensing Range and Influencing Factors
Every inductive sensor has a specified nominal sensing range (Sn). This is the ideal distance at which a standard test target (usually a square of mild steel) will reliably trigger the sensor. Real-world performance can be influenced by:
- Target Material: Different metals have varying abilities to generate eddy currents. Mild steel provides the longest sensing range. Stainless steel (especially non-magnetic types like 304⁄316) reduces the range significantly. Copper and aluminum have even shorter ranges compared to steel.
- Target Size: The target must be large enough to interact sufficiently with the magnetic field. Targets smaller than the sensor’s face or thinner than its recommended minimum thickness may not be reliably detected at the full nominal range.
- Installation: Flush-mountable sensors can be installed flush with metal surfaces. Non-flush sensors require a clear zone around their sides to avoid interference from adjacent metal. Embedding a sensor too deeply in metal or having nearby metallic structures can drastically reduce its effective range or cause false triggering.
- Temperature: Extreme temperatures can affect the sensor’s internal electronics and coil resistance, potentially altering the sensing range. Always consult specifications for operating temperature ranges. Selecting the correct sensor involves carefully considering these factors for the specific application.
Where Inductive Prox Sensors Shine: Industrial Applications
The reliability, speed, and robustness of inductive prox sensors make them ubiquitous across virtually every industry. Common applications include:
- Position Detection: Verifying parts are present, correctly seated, or have reached a specific point in a machine cycle (e.g., end-of-stroke detection on hydraulic or pneumatic cylinders).
- Object Counting: Counting bottles, cans, packages, or parts moving on a conveyor line.
- Speed Monitoring: Detecting gear teeth, encoder flags, or rotating shafts to measure rotational speed.
- Level Detection: Sensing the presence of metal objects within bins or tanks.
- Machine Safety: Serving as part of safety interlocks on machine guards to prevent operation when guards are open.
- End-of-Travel Sensing: Confirming the open/closed position of valves, slides, or doors.
- Перевозка материалов: Detecting pallets, carts, or metallic components on automated guided vehicles (AGVs) or assembly lines.
- Automotive Manufacturing: Widely used in assembly line robotics, part positioning, fluid level checks (metal floats), and welding systems.
Choosing the Right Inductive Prox Sensor
Selecting the optimal sensor involves evaluating several criteria:
- Sensing Distance: Required distance to the target.
- Target Material: Type of metal being detected.
- Mounting Constraints: Available space and mounting configuration (flush/non-flush).
- Environmental Conditions: Temperature, presence of chemicals, moisture exposure (IP rating needed).
- Electrical Requirements: Supply voltage (DC/AC), required output type (NPN/PNP), current rating.
- Housing/Form Factor: Cylindrical (M8, M12, M18, M30), rectangular, or specialty shapes.
Modern advancements include sensors with IO-Link digital communication, allowing for parameter setting, remote diagnostics, and process data transmission beyond simple ON/OFF signals, enhancing their role in Industry 4.0 applications. Inductive proximity sensors, driven by their fundamental electromagnetic principle, offer a uniquely reliable and cost-effective solution for detecting metal objects without contact. Their rugged construction, immunity to harsh environments, and high-speed operation cement their position as indispensable components in the unseen world of industrial automation, silently ensuring precision, efficiency, and safety in countless applications worldwide. Understanding their operation and capabilities is fundamental for designing and maintaining robust automated systems.