m18 индукционный датчик приближения
- time:2025-07-03 03:37:03
- Нажмите:0
M18 Inductive Proximity Sensors: The Compact Powerhouses of Industrial Automation
Imagine a high-speed bottling line. Glass containers whizz by, filled, capped, and labeled in a blur. Suddenly, a misplaced metal component jams a critical conveyor. Production grinds to a halt. Downtime costs escalate. This scenario highlights the critical importance of reliable, non-contact detection – precisely where the M18 inductive proximity sensor shines as an unsung hero on the factory floor. These rugged, versatile sensors are fundamental to modern automation, offering robust metal detection in a remarkably compact package.
Understanding the Inductive Principle: Sensing Without Touch
At the heart of every M18 inductive proximity sensor lies a simple yet brilliant electromagnetic principle. Inside its typically cylindrical, 18mm diameter stainless steel or nickel-plated brass housing resides an oscillator coil generating a high-frequency electromagnetic field. This field emanates from the active face of the sensor.
When a metallic target (ferrous – like iron and steel, or non-ferrous – like aluminum, brass, copper) enters this field, eddy currents are induced within the target. These eddy currents draw energy from the sensor’s oscillator circuit, causing a measurable change – typically a reduction in oscillation amplitude. The sensor’s built-in electronics detect this change and trigger a solid-state output switch (PNP, NPN, NO, NC). Crucially, this happens without any physical contact, enabling detection through non-metallic barriers and eliminating wear and tear.
Why M18? The Goldilocks of Sensor Sizes
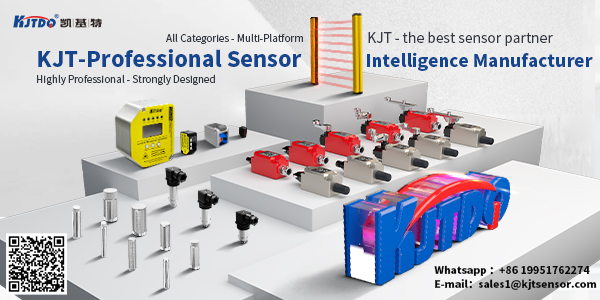
The “M18” designation refers to the sensor’s standard threaded barrel diameter – 18 millimeters. This size has become arguably the most popular in industrial automation for several compelling reasons:
- Многогранность: The M18 form factor strikes an excellent balance between size and performance. It’s large enough to house robust electronics and offer substantial sensing ranges (often 2mm, 4mm, 5mm, or 8mm, depending on the specific model and target material), yet compact enough to fit into tight spaces where larger sensors simply couldn’t go. This makes them suitable for a vast array of applications, from intricate machinery to larger assembly lines.
- Robustness & Standardization: The threaded barrel allows for easy and secure mounting using standard M18 nuts. Their construction is inherently robust, designed to withstand the harsh realities of industrial environments, including exposure to oil, coolants, dust, vibration, and moderate impacts. Many models boast high IP ratings (like IP67 or IP69K), indicating excellent dust and water resistance.
- Wide Availability & Compatibility: Due to their popularity, M18 inductive sensors are offered by virtually every major industrial sensor manufacturer. This leads to intense competition, driving innovation and ensuring competitive pricing. It also means extensive compatibility with mounting brackets, protective accessories, and control systems.
- Cost-Effectiveness: Their mass production and standardization make M18 sensors highly cost-effective, delivering reliable performance without breaking the bank. This is crucial for applications requiring numerous sensors.
Key Features and Capabilities: Beyond Basic Detection
Modern M18 inductive sensors offer more than just simple presence detection. Key features that enhance their value include:
- Embedded Output Indicators: A built-in LED typically signals power-on status and output activation, simplifying debugging and commissioning directly at the sensor.
- Shielded vs. Unshielded Designs: Shielded (flush-mountable) sensors allow mounting flush in metal without affecting their sensing field. Unshielded (non-flush) sensors offer slightly longer sensing ranges but require a specific clearance around them when mounted near metal. Choosing the correct type is vital for reliable operation.
- Output Configuration Flexibility: Available in Normally Open (NO), Normally Closed (NC), or configurable versions, with transistor outputs (NPN sinking or PNP sourcing) compatible with most PLCs and controllers. Reliable solid-state switching ensures long life.
- High Switching Frequencies: Many models can operate at high speeds, detecting rapidly moving targets (e.g., gear teeth, fast-moving parts on conveyors), essential for high-throughput automation.
- Temperature Resilience: Designed to operate reliably across a wide industrial temperature range, often from -25°C to +70°C or beyond.
Diverse Applications: Where M18 Sensors Excel
Their robustness, size, and reliability make M18 inductive sensors ubiquitous across countless industries:
- Machine Tooling: Detecting tool presence/absence, position of slides and chucks, end-of-stroke confirmation.
- Перевозка материалов: Monitoring conveyor line objects (metal cans, cartons with metal staples, pallets), counting parts, detecting metal components on non-metallic carriers, verifying bin presence. Critical for preventing jams and ensuring smooth material flow.
- Packaging Machinery: Verifying cap or lid placement (metal), detecting foil seals, monitoring moving parts.
- Automotive Manufacturing: Position sensing of robots, detecting engine blocks or chassis components on assembly lines, presence/absence checks in fixtures. Essential for precision assembly.
- Food & Beverage (Specific Models): Detecting metal tags, foil seals, cans, or specialized stainless steel sensors for wash-down areas.
- General Assembly: Position feedback for cylinders, detecting pallet stops, verifying part orientation before processing.
Selecting the Right M18 Sensor: Critical Considerations
Choosing the optimal M18 inductive proximity sensor requires careful thought beyond just the size:
- Sensing Distance: Select a sensor with a rated operating distance (
Sn
) suitable for your application, considering factors like target size and approach direction. Always allow for a safety margin; don’t operate right at the limit.
- Target Material: Ferrous targets (steel) trigger the longest sensing distances. Non-ferrous metals (aluminum, copper) significantly reduce the range – often requiring sensors specifically designed or rated for them. Stainless steel detection typically requires special factors or sensors optimized for it.
- Shielded vs. Unshielded: If mounting in metal or needing a flush surface, choose shielded. If maximum range is needed and mounting in non-metal, unshielded might be suitable.
- Output Type & Wiring: Ensure compatibility (PNP vs. NPN, NO vs. NC) with your controller input modules and voltage level (commonly 10-30V DC).
- Environmental Rating: Match the sensor’s IP rating to the environment (dust, moisture, washdown, oils). IP67 is common; IP69K is needed for high-pressure/high-temperature washdown.
- Housing Material: Stainless steel (V4A/AISI 316L variants) offers superior corrosion resistance for harsh chemical or washdown environments compared to nickel-plated brass.
- Temperature Range: Ensure the sensor’s operating temperature range covers your application’s extremes.
- Connection Type: Integral cable or connector (M8, M12)? Connectors offer easier replacement and cable management.
The Indispensable Workhorse
From preventing costly jams on bottling lines to ensuring robotic arms position components flawlessly, the M18 inductive proximity sensor remains a cornerstone of efficient and reliable industrial automation. Its winning combination of compact size, robust construction, standardized form factor, non-contact operation, and proven performance makes it an indispensable tool for engineers and technicians worldwide. By understanding their operating principle, key features, and selection criteria, you can leverage these sensors effectively to enhance the speed, reliability, and safety of your automated processes. Whether counting parts, verifying positions, or safeguarding machinery, the humble M18 sensor quietly powers the precision of modern manufacturing.