inductive sensor m8
- time:2025-07-03 03:18:59
- Нажмите:0
M8 Inductive Sensors: The Compact Powerhouses for Precision Detection in Automation
Imagine a high-speed production line where robotic arms move with lightning speed, assembling intricate components. Ensuring a drill bit is perfectly positioned before machining, confirming a metal panel is present before welding, or detecting the precise position of a cylinder – all these critical tasks happen repeatedly, reliably, and contactlessly. The unsung hero enabling such precision detection in confined spaces? Often, it’s the M8 inductive sensor. This compact marvel is a cornerstone of modern industrial automation, offering robust, non-contact sensing where space is at a premium.
Understanding the “Inductive Sensor M8” Designation
Let’s break down the term. Inductive sensors operate on the principle of electromagnetic induction. Inside the sensor head lies an oscillator coil that generates a high-frequency alternating electromagnetic field. When a ferrous (iron-based) or non-ferrous (like aluminum, brass, copper) metallic target enters this field, it induces eddy currents within the target. These eddy currents cause a measurable change (typically a reduction) in the amplitude of the oscillator’s oscillation. An internal circuit detects this change and switches the sensor’s output state – from “OFF” to “ON” or vice-versa.
The “M8” designation refers specifically to the standardized thread size and cylindrical housing diameter of the sensor. M8 sensors have an impressive 8mm outside diameter thread (M8 x 1.0 mm pitch is common), making them significantly smaller than the also prevalent M12 and M18 versions. This compact form factor is their defining characteristic and primary advantage.
Why Size Matters: The Core Advantage of M8 Inductive Sensors
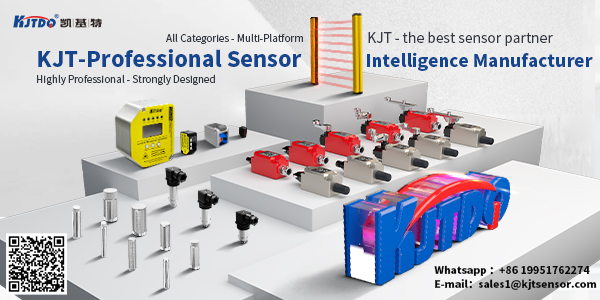
In the densely packed world of machinery, control panels, and robotic work cells, space is a critical commodity. Larger sensors, like M18s, simply cannot fit into tight mounting locations or sense targets in cramped corners. The ultra-compact M8 design solves this problem elegantly. Their miniature size allows for installation in locations previously inaccessible, enabling smarter machine design and finer-grained control over processes. Design engineers gain greater flexibility to integrate detection points exactly where needed.
Technical Capabilities: Punching Above Their Weight
Don’t let their small stature fool you. M8 inductive sensors deliver impressive performance:
- Sensing Range: While inherently limited by their physical size compared to larger sensors, typical sensing ranges for M8 inductive sensors range from 1mm to 2mm. Flush-mounted variants usually offer 1mm, while non-flush types can reach up to 2mm for ferrous targets. Selecting the correct type (flush vs. non-flush) is crucial for the application.
- Flush vs. Non-Flush Mounting:
- Flush-Mountable (Shielded): These M8 sensors can be installed flush with surrounding metal. Their electromagnetic field is concentrated primarily forward, minimizing side interference. Ideal for tight spaces with metal proximity.
- Non-Flush Mountable (Unshielded): Offer slightly longer sensing ranges. However, they must have sufficient clearance around the sides as their field extends laterally, making them susceptible to interference from adjacent metal. Less common in M8 size due to space constraints.
- Output Types: Available in standard configurations:
- PNP (Sourcing): The most common type. Switches the positive (+) voltage line to the load when activated.
- NPN (Sinking): Switches the negative (-) voltage line to the load when activated. Essential for some PLC input card requirements.
- Outputs can be Normally Open (NO) or Normally Closed (NC).
- Environmental Resilience: Engineered for harsh industrial environments, quality M8 proximity sensors boast high Ingress Protection (IP) ratings (like IP67, IP68, IP69K), signifying excellent resistance to dust, water jets, and even temporary submersion. They are resistant to vibration, common cutting fluids, oils, and offer reliable operation across a wide temperature range (-25°C to +70°C is typical).
- Switching Frequency: Capable of high switching speeds, often exceeding 1kHz (1000 times per second), making them suitable for detecting fast-moving parts or high-speed counting applications.
Key Applications: Where the M8 Shines
The compact M8 sensor finds its niche in countless demanding applications:
- Miniature Machinery & Robotics: Detecting end positions of small actuators, verifying gripper closure on tiny parts, confirming tool presence in compact spindle heads, or monitoring cylinder piston position on small pneumatic/hydraulic systems within robotic arms.
- Conveyor Systems: Verifying the presence of small metal parts, bottles with metallic caps, or cans on tight-spaced conveyors before processing, sorting, or packaging.
- Packaging Machines: Detecting foil seals, metallic components within packaging, or verifying the position of small cams, levers, or feeders in intricate packaging mechanisms.
- Electronics Assembly: Monitoring precise placement of SMD feeders, detecting the position of miniature slides, or confirming metal components on PCBs during testing (with careful distance consideration).
- CNC Machines & Tooling: Tool breakage detection (especially on smaller tools), spindle orientation verification, or monitoring coolant system components.
- Valve Position Feedback: Providing reliable position confirmation on small solenoid valves or actuators in fluid control systems.
Selecting and Deploying M8 Inductive Sensors Effectively
Choosing the right inductive proximity sensor M8 involves several key considerations:
- Target Material: Primarily ferrous steel? Or non-ferrous like aluminum, brass, copper? Sensing range is typically shorter for non-ferrous metals. Reliable detection is guaranteed for ferrous targets. Confirm range specifications for non-ferrous materials.
- Required Sensing Distance: Match the required gap between sensor face and target to the sensor’s rated sensing range (Sn), providing a small safety margin.
- Mounting Constraints: Is flush mounting essential due to surrounding metal? Choose shielded (flush) if yes. If ample space exists and maximum range is needed, unshielded (non-flush) might be viable (though less common in M8).
- Output Configuration (PNP/NPN, NO/NC): Must match the input requirements of your controller (PLC, relay, counter).
- Environment: Verify the required IP rating and temperature range. For washdown (IP69K) or extreme chemical exposure, specialized variants exist.
Installation requires attention to mounting torque (avoid over-tightening the small threads!) and ensuring the target approaches the sensing face correctly. Maintaining the specified operating voltage is critical for longevity and reliable operation.
The Compact Indispensable: Why M8 Sensors Endure
In the relentless drive for miniaturization and efficiency, the M8 inductive sensor has proven its immense value. Its ability to deliver robust, contactless, and reliable metal detection within an incredibly small footprint makes it an irreplaceable component in modern automation. From ensuring the precision of microscopic assembly robots to verifying the positions of components in high-speed packaging lines, these compact sensors are fundamental to the smooth, accurate, and efficient operation of countless industrial processes. When space is tight, but performance cannot be compromised, the M8 inductive proximity sensor is often the perfect solution, quietly ensuring quality and productivity one metallic detection at a time.