датчик плоского сближения
- time:2025-07-03 02:18:44
- Нажмите:0
Flat Proximity Sensors: The Essential Guide to Slim, Powerful Detection
Imagine a sensor thinner than your smartphone, virtually invisible when installed, yet capable of detecting objects without a single touch. This isn’t science fiction; it’s the reality of flat proximity sensors. In a world where device miniaturization reigns supreme and sleek aesthetics are non-negotiable, these low-profile marvels are quietly revolutionising how machines interact with their environment. From the device in your pocket to the factory floor, flat proximity sensors are the slim, indispensable workhorses enabling smarter, cleaner, and more efficient designs. They’re the essential vitamins of modern automation, packed without bulk.
Why Flatness Matters: The Core Advantage
Traditional proximity sensors often protrude. While functional, they create design headaches. Flat proximity sensors, as the name implies, feature an exceptionally low-profile housing. This seemingly simple characteristic unlocks critical benefits:
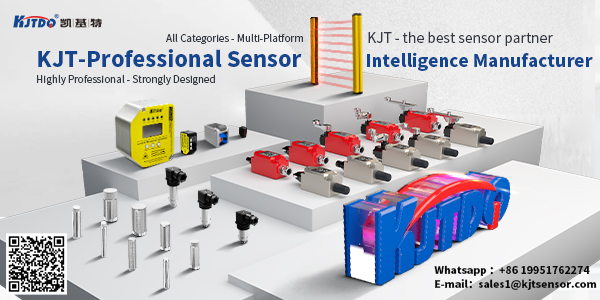
- Space Savings: Crucial in compact devices like smartphones, tablets, laptops, and wearables, where internal real estate is at a premium. They fit seamlessly without compromising other components.
- Simplified Installation: Their design allows for flush mounting directly into panels, enclosures, or bezels. No complex machining or bulky mounts are needed, leading to cleaner aesthetics and easier assembly.
- Reduced Vulnerability: Sitting flush makes them less likely to suffer physical damage from bumps, scrapes, or passing objects compared to protruding sensors.
- Enhanced Aesthetics: For consumer electronics and modern machinery, a sleek, unbroken surface is desirable. Flat sensors contribute significantly to a clean, high-tech appearance.
- Easier Sealing: Achieving weatherproofing (IP ratings) or dust resistance is often more straightforward with a flat mounting surface, enhancing durability in harsh environments.
How Do Flat Proximity Sensors Work? The Core Technologies
While the form factor is defining, the underlying detection principles follow established proximity sensor technologies, primarily adapted into a slim package:
- Capacitive Proximity Sensing: This is exceptionally common for flat sensors. They detect changes in the electrical field around their active surface (sensing face). When an object (conductor or non-conductor, depending on sensor type) enters this field, it alters the capacitance, triggering the sensor. Flat capacitive sensors excel in detecting fingers through glass (think smartphone screens/touchless buttons), plastics, or thin materials. Their non-contact operation is key.
- Infrared (IR) Proximity Sensing: These sensors combine an IR emitter and an IR detector. The emitter sends out an infrared light beam. If an object comes close, the light reflects back to the detector, signaling presence. Carefully designed optics allow these to function effectively within the constraints of a flat profile. They are widely used for screen blanking in phones/tablets when held to the ear.
- Magnetic Proximity Sensing: Utilizing a Reed switch or a Hall Effect sensor, these detect the presence of a magnet. The flat design allows them to be easily embedded within the surface of machinery or equipment to detect the position of moving parts equipped with magnets. Their operation is highly reliable and unaffected by non-magnetic materials.
Where You’ll Find Them: Essential Applications
The unique combination of slim dimensions and reliable non-contact detection makes flat proximity sensors indispensable across numerous sectors:
- Consumer Electronics: The most visible application. Responsible for screen blanking (IR) when phones are held near the ear, enabling touchless gestures or buttons (capacitive) hidden beneath glass or plastic bezels. Found in laptops (lid close detection), tablets, wearables, and smart home devices. Their integration is key to the modern user experience.
- Промышленная автоматизация: Used for precise position detection of components on assembly lines, verifying the presence of materials or products, end-of-travel sensing on cylinders (especially magnetic types), and inside machinery where space is extremely limited. Flush mounting prevents snagging in busy environments.
- Automotive: Employed in dashboard controls (capacitive touch), gear shift position sensing, door ajar detection, glove box illumination, and increasingly in advanced driver-assistance systems (ADAS). Robustness and reliability are paramount here.
- Elevators & Building Automation: Hidden behind stainless steel panels or glass for touchless call buttons (hygienic solution). Used for door safety edges and position verification.
- Medical Devices: Integrated into handheld equipment for mode switching or activation, and within diagnostic instruments requiring reliable component positioning. Hygienic flush surfaces are a major benefit.
- Security Systems: Discreetly installed for tamper detection on doors/windows or presence sensing in restricted areas.
Key Advantages Driving Adoption
Beyond the core benefit of their form factor, flat proximity sensors deliver significant operational advantages:
- Non-Contact Sensing: Eliminates mechanical wear and tear, ensuring long operational lifetimes. Ideal for clean environments or delicate objects.
- High Reliability: Solid-state electronics (especially capacitive and Hall Effect) offer consistent, repeatable performance with minimal maintenance.
- Fast Response Times: Detecting presence or absence near-instantly, crucial for high-speed automation processes.
- Многогранность: Capable of detecting a wide range of materials – metals, plastics, liquids, skin (depending on the technology chosen).
- Seamless Integration: The ultra-thin design allows OEMs to incorporate detection capabilities without compromising the intended industrial design or product footprint. This design flexibility is a major competitive advantage.
Choosing the Right Flat Proximity Sensor: Key Considerations
Selecting the optimal датчик плоского сближения requires careful evaluation of your specific application needs:
- Detection Technology: What material are you detecting? (Metal, plastic, hand, liquid?) What’s the required sensing range? This dictates whether capacitive, IR, or magnetic is appropriate. Capacitive sensors offer great flexibility for non-metals, while magnetic sensors excel for precise position detection with magnets.
- Sensing Distance: Flat proximity sensors generally have shorter ranges than their larger counterparts. Ensure the specified nominal sensing range meets your requirements, factoring in installation specifics.
- Mounting Requirements: Confirm the exact dimensions, cutout size (for flush mounting), and sealing needs (e.g., IP67, IP69K for washdown environments). Proper installation is critical for performance.
- Output Type: Does your system require a simple digital signal (PNP/NPN transistor, NO/NC)? Or analog output (for distance measurement)? Ensure compatibility with your controller’s inputs.
- Environmental Conditions: Consider temperature extremes, humidity, potential exposure to chemicals, oils, or cleaning agents. Choose sensors rated for the operating environment.
- Power Supply: Match the sensor’s voltage requirements (e.g., 10-30V DC, 5V DC) to your system’s available power.
The quest for thinner, smarter, and more seamlessly integrated technology shows no signs of slowing. Flat proximity sensors are a fundamental enabler of this trend. By shrinking the footprint of reliable detection, they empower designers and engineers to push boundaries. Whether it’s creating the next generation of impossibly thin smartphones, building more efficient factory robots, or designing intuitive automotive interfaces, the low-profile, high-performance nature of these sensors makes them an essential component. Understanding their capabilities and applications is key to unlocking innovative solutions where space is constrained and reliability cannot be compromised. As technology evolves, expect these sensors to become even more powerful, versatile, and seamlessly woven into the fabric of our devices and machinery.