Маленький индуктивный датчик
- time:2025-07-03 02:06:41
- Нажмите:0
Small Inductive Sensors: Miniature Marvels Powering Modern Automation
In the intricate dance of modern machinery, where precision and reliability are non-negotiable, a tiny titan silently performs critical tasks: the small inductive sensor. Often overlooked due to their unassuming size, these robust electronic workhorses are fundamental components in countless industrial, automotive, and consumer applications. They epitomize the principle that big capabilities often come in the smallest packages, enabling non-contact detection of metallic objects with remarkable consistency. Understanding their function, advantages, and diverse uses reveals why they remain a cornerstone of automated systems.
The Core Principle: Electromagnetism at Work
At the heart of every inductive proximity sensor lies a core principle: electromagnetic induction. A simple coil housed within the sensor is energized by an oscillator circuit, generating a high-frequency alternating electromagnetic field at its active sensing face. When a ferrous or non-ferrous metallic target enters this field, eddy currents are induced on the surface of the target. These eddy currents draw energy from the sensor’s oscillating field, causing a measurable change in the oscillation’s amplitude or frequency.
An internal electronic circuit constantly monitors this change. Once the shift exceeds a predetermined threshold – corresponding to the sensor’s specified switching distance – the sensor triggers its output state. This output signal (typically a solid-state switch like NPN/PNP transistors) can then control other devices: activating a PLC input, turning on a warning light, stopping a conveyor belt, or counting parts. Crucially, this detection happens without any physical contact, eliminating wear and tear.
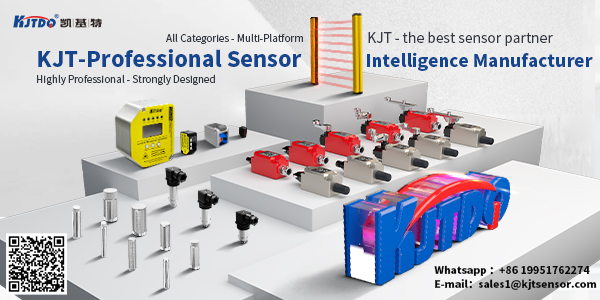
Why “Small” Matters: The Compelling Advantages
The defining characteristic of these sensors is their miniature form factor, but the benefits extend far beyond just saving space:
- Robustness and Longevity: With no moving parts and hermetically sealed sensing heads (often in rugged materials like nickel-plated brass or stainless steel), small inductive sensors thrive in demanding industrial environments. They resist dirt, dust, moisture (many boast IP67 or IP68 ratings), oils, and mechanical vibration far better than mechanical switches.
- High Switching Frequency and Speed: Capable of detecting rapidly moving targets thousands of times per minute, they excel in high-speed counting, positioning, and inspection tasks where mechanical switches would quickly fail or lag.
- Non-Contact Operation: This is their defining superpower. No physical touch means no target wear, no sensor wear, no contact bounce, and silent operation. It allows for detection through thin non-metallic barriers (like paint, plastic, or glass) and enables hygienic applications.
- Reliability & Repeat Accuracy: Once installed and correctly aligned, they offer incredibly consistent and repeatable detection, cycle after cycle, crucial for process stability and quality control. The switching point is precise and not subject to mechanical hysteresis like limit switches.
- Cost-Effectiveness: For their reliability and lifespan, small inductive sensors offer a very attractive total cost of ownership, minimizing downtime and replacement costs associated with mechanical counterparts.
- Simple Installation & Integration: Their compact size allows for mounting in confined spaces, and standardized cylindrical housings (e.g., M5, M8, M12, M18, M30) simplify integration into machinery and connection via pre-made cables or connectors.
Where Tiny Titans Rule: Key Applications
The versatility of small inductive proximity sensors means they are ubiquitous. Here are prominent examples:
- Factory Automation & Robotics: Detecting the position of machine components (end-of-stroke, part present/absent), counting products on a conveyor (object detection), verifying tool presence in CNC spindles, monitoring robotic arm positions.
- Перевозка материалов: Controlling filling levels (detecting metal parts in bins), verifying package position on conveyors, actuating sorting gates, confirming pallet presence.
- Automotive Manufacturing & Assembly: Verifying component placement (bolts, bearings, gears), detecting piston position in cylinders, confirming door/window closure for safety interlocks, monitoring robotic weld gun position.
- Packaging Machinery: Detecting filled cans/bottles, confirming cap placement, controlling case packer operations, verifying label presence.
- Machine Safety: Serving as part of safety interlock circuits (confirming guard doors are securely closed).
- Consumer Equipment: Detecting lid closure in appliances, position sensing in printers/copiers, speed sensing in power tools.
- Mobile Machinery: Monitoring hydraulic cylinder position, detecting bucket angle, confirming latch engagement.
Choosing the Right Miniature Sensor: Key Considerations
Selecting the optimal sensor involves more than just size:
- Sensing Distance: The nominal range specified for detecting a standard target (usually mild steel). Real-world distance varies with target material, size, and shape. Shielded models offer flush mounting capability but shorter ranges; unshielded models have longer ranges but require more surrounding space.
- Target Material: Standard sensors are calibrated for steel. Factors (typically 0.3-1.0) apply for non-ferrous metals like aluminum or brass, reducing the effective sensing range. Specialized sensors optimized for non-ferrous detection exist.
- Housing Size & Style: Cylindrical (M5, M8, M12, M18, M30) is most common, but rectangular or block styles are also available. Size dictates mounting options and space constraints.
- Output Configuration: Select between NPN (sinking) or PNP (sourcing) transistor outputs (3-wire), often with Normally Open (NO) or Normally Closed (NC) logic. 2-wire AC/DC models are also available.
- Electrical Specifications: Operating voltage range (e.g., 10-30V DC), current consumption, and load current capacity.
- Environmental Rating: IP rating for dust/water resistance is critical. Also consider resistance to chemicals, welding fields (high immunity models), temperature extremes, and mechanical shock/vibration.
- Connection Type: Pre-wired cable, quick-disconnect connector (e.g., M8, M12), or terminal block.
Beyond the Basics: Enhancing Capabilities
Manufacturers continuously innovate, adding features to these fundamental sensors. Some advanced variants include:
- Analog Output: Provide a continuous signal (e.g., 0-10V, 4-20mA) proportional to the distance to the target, enabling precise position monitoring.
- IO-Link Compatibility: This communication protocol transforms the simple sensor into a smart device, enabling remote configuration, detailed diagnostics, and process data exchange over a standard 3-wire connection.
- Enhanced Immunity: Specialized designs offer superior resistance to electromagnetic interference (EMI) common in welding environments or near large motors and drives.
- High-Temperature Models: Engineered to operate reliably in environments exceeding standard industrial temperature ranges.
From quiet sentinels on high-speed assembly lines to reliable checkpoints in complex robotic systems, small inductive sensors deliver indispensable performance. Their combination of ruggedness, non-contact operation, precision, and compact size makes them an enduringly vital component in the automation landscape. As technology evolves, integrating smarter features like IO-Link ensures these miniature marvels will continue to play a significant role in driving efficiency, reliability, and intelligence in countless applications for years to come, proving that true power often resides in the smallest details.