Датчик DPT
- time:2025-07-03 01:54:38
- Нажмите:0
DPT Sensor: The Silent Sentinel Optimizing Industrial Processes, Energy, and Safety
Imagine a critical industrial process humming along smoothly. Fluids flow through intricate piping, air circulates in vast cleanrooms, filters trap contaminants – all seemingly automatic. Yet, beneath this seamless operation, countless silent sentinels constantly monitor and report vital health metrics. Among the most crucial and versatile are Differential Pressure Transducers (DPT Sensors). These unassuming devices are fundamental to efficiency, safety, and control across a staggering array of modern industries.
What Exactly is a DPT Sensor?
Put simply, a differential pressure transducer is an electronic device engineered to measure the difference in pressure between two distinct points. It doesn’t provide an absolute pressure reading relative to a vacuum or atmosphere; instead, it precisely quantifies how much higher or lower the pressure is at one point compared to another. This seemingly simple function unlocks powerful capabilities for monitoring, control, and protection. DPT sensors convert this measured pressure difference into a standardized electrical signal – commonly 4-20 mA or 0-10 V DC – which can then be easily interpreted by control systems, data loggers, or human-machine interfaces (HMIs).
The Core Mechanism: Sensing the Difference
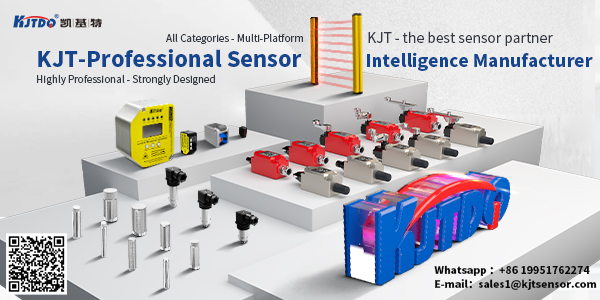
While designs vary, the fundamental principle often involves a sensitive diaphragm. This diaphragm separates two pressure chambers: one connected to the “High” pressure port, the other to the “Low” pressure port. The pressure difference (ΔP) across this diaphragm causes it to deflect minutely. This deflection is then meticulously measured. Modern dpt sensors typically employ advanced technologies for this detection:
- Strain Gauge: Tiny resistive elements bonded to the diaphragm change resistance as it flexes. This resistance change is measured within a Wheatstone bridge circuit to produce the output signal. Known for robustness and cost-effectiveness.
- Capacitive: The diaphragm acts as one plate of a capacitor, while a fixed plate sits nearby. As the diaphragm deflects, the distance between the plates changes, altering capacitance. This change is converted into the output signal. Offers high accuracy and stability, excellent for low-pressure applications.
- Piezoresistive: Similar to strain gauge, but utilizes semiconductor materials (like silicon) where resistance changes significantly under stress. Often integrated into MEMS (Micro-Electro-Mechanical Systems) designs, enabling very small, sensitive devices.
- Resonant: Measures the shift in resonant frequency of a vibrating element attached to the diaphragm caused by pressure-induced strain. Extremely high accuracy and stability.
Where DPT Sensors Shine: Critical Applications
The ability to measure pressure differences makes dpt sensors indispensable in countless scenarios:
- Filter Monitoring: The most common application by far. Installed across filters (air, liquid), a differential pressure transducer indicates the buildup of contaminants. As the filter clogs, the ΔP increases. Monitoring this provides a clear signal for timely filter changes, preventing damage from excessive pressure drop, energy waste from blocked flow, or loss of filtration efficiency. Predictive maintenance saves costs and prevents downtime.
- Flow Measurement: Based on Bernoulli’s principle, flowing fluid creates a pressure drop across a restriction in a pipe (like an orifice plate, venturi tube, or flow nozzle). A Датчик DPT measures this ΔP directly, and the flow rate can be calculated precisely using the known characteristics of the restriction. This method is widely used for liquids, gases, and steam.
- Tank Level Measurement: In a vented tank, the pressure at the bottom is proportional to the liquid height above it. A Датчик DPT can measure the difference between this bottom pressure and the atmospheric pressure at the top (vent), providing accurate level indication. For closed tanks under some pressure, one port measures pressure above the liquid, while the other connects to the tank bottom; the ΔP relates directly to the liquid level.
- HVAC Systems: Crucial for monitoring airflow across coils, dampers, and filters, ensuring energy efficiency and occupant comfort. They control variable air volume (VAV) systems and maintain critical pressure differentials in cleanrooms or isolation rooms to prevent contamination spread.
- Leak Testing: Precise differential pressure measurement is a cornerstone of leak detection in sealed vessels, pipelines, or assemblies. Even tiny leaks cause a measurable drop in pressure difference over time.
- Boiler Draft Control: Monitoring draft pressure in boiler stacks is essential for safe and efficient fuel combustion. Dpt sensors provide the feedback needed for precise airflow control.
- Medical Devices: Found in ventilators, anesthesia machines, and respiratory monitors, where measuring breath pressure differentials is critical for patient safety and treatment efficacy.
- Process Control: Monitoring pressure drops across critical valves, reactors, or heat exchangers provides insights into process health, enabling optimization and early fault detection.
Why Choosing the Right DPT Sensor Matters: Key Considerations
Selecting the ideal differential pressure transducer involves understanding the specific demands of the application:
- Pressure Range: The sensor must comfortably handle both the static line pressure and the maximum expected ΔP without over-range damage or loss of accuracy.
- Accuracy: Critical for flow measurement or level control. Specified as a percentage of full scale (% FS) or span. Consider Total Error Band (TEB) for a realistic view.
- Output Signal: Ensure compatibility with existing control systems (4-20mA, 0-5/10V, digital protocols like HART, Modbus, or IO-Link).
- Media Compatibility: The wetted parts (diaphragm, seals, housing ports) must resist corrosion or degradation by the measured fluid or gas. Common materials include 316L stainless steel, Hastelloy, and specific elastomers.
- Operating Environment: Temperature limits, potential exposure to humidity, vibration, EMI/RFI interference, and hazardous areas requiring intrinsically safe or explosion-proof certifications (ATEX, IECEx).
- Reference Pressure: For gauge sensors (common), the low-pressure side is referenced to atmosphere. Sealed gauge sensors reference to a fixed pressure within the device. True differential sensors measure any two pressures independently.
- Porting and Mounting: Physical connection types (e.g., NPT threads, G½”) and orientation requirements.
The Undeniable Value Proposition: Beyond Just Measurement
Integrating robust dpt sensors delivers tangible benefits that boost the bottom line:
- Enhanced Process Efficiency: Optimizing flow rates, filter changes, and combustion directly reduces energy consumption. Real-time monitoring enables precise control.
- Improved Product Quality and Consistency: Maintaining critical pressure differentials is essential in pharmaceutical manufacturing, food & beverage processing, and semiconductor fabrication.
- Predictive & Preventative Maintenance: Early detection of clogged filters, leaks, or abnormal pressure drops allows for planned interventions, avoiding costly unplanned shutdowns and catastrophic failures. This proactive approach maximizes asset lifespan.
- Strict Safety Compliance: Monitoring pressures in boilers, gas lines, and critical processes ensures operations stay within safe limits, protecting personnel and equipment.
- Reduced Operational Costs: Minimizing energy waste, preventing equipment damage, and enabling efficient maintenance scheduling all contribute significantly to lowering overall operating expenses.
From the complex machinery driving industrial giants to the life-sustaining equipment in hospitals, the differential pressure transducer operates tirelessly in the background. Its ability to detect minute differences unlocks vast capabilities in monitoring, control, and safety. Understanding what a dpt sensor is and how it fundamentally enables critical operations highlights why this technology remains a cornerstone of modern engineering and process control. Choosing and deploying the right sensor for the application is an investment in reliability, efficiency, and safety that pays continuous dividends.