Датчик приближения HTM
- time:2025-07-03 01:18:32
- Нажмите:0
HTM Proximity Sensors: Unlocking Touchless Control with Magnetic Precision
Ever wondered how your smartphone screen automatically dims when held to your ear? Or how sophisticated industrial machinery detects the precise position of components without physical contact? The answer often lies in a category of sensors known by the acronym HTM – Hall-effect, Touchless, Magnetic. HTM proximity sensors represent a cornerstone of modern touchless detection, leveraging magnetic fields to deliver reliability where other sensors falter. Understanding their unique capabilities is key to unlocking efficient and robust automation solutions across countless industries.
Decoding the “HTM” in Proximity Sensing
While not a single, rigid standard, “HTM” effectively captures the defining characteristics of this sensor family:
- Hall-effect: The core technology. Named after Edwin Hall, this principle dictates that when a current-carrying conductor is placed in a magnetic field perpendicular to the current flow, a voltage (the Hall voltage) is generated perpendicular to both. This voltage is proportional to the magnetic field strength.
- Touchless: Detection occurs without any physical contact between the sensor and the target object. This eliminates wear and tear, reduces maintenance, and allows for detection through non-magnetic barriers.
- Magnetic: These sensors specifically respond to magnetic fields. The target object must be ferromagnetic (like iron or steel) or incorporate a permanent magnet.
How HTM Proximity Sensors Work: A Magnetic Dance
The core operation is elegantly simple:
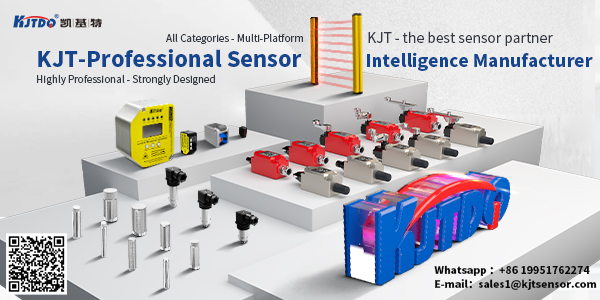
- The Sensor: An HTM proximity sensor contains a Hall-effect element (often an integrated circuit), a magnet (either internal or requiring an external target magnet), and signal conditioning electronics.
- The Field: The sensor’s internal magnet (or the target magnet) generates a static magnetic field in the surrounding space.
- Interaction: When a ferromagnetic target (like a piece of steel) or a permanent magnet enters this magnetic field, it disturbs the field lines.
- Detection: The Hall-effect element within the sensor detects the change in the magnetic field’s strength or polarity. This change causes the Hall voltage to shift.
- Output: The sensor’s internal circuitry processes this shift. When the change exceeds a predefined threshold (hysteresis), the sensor’s electronic output switches state. This typically means changing from an “OFF” (open circuit) to an “ON” (closed circuit) state, or vice-versa, providing a clean digital signal usable by controllers like PLCs.
Why Choose HTM Sensors? Key Advantages Propelling Adoption
HTM proximity sensors offer distinct benefits over alternative technologies like inductive or capacitive sensors:
- Reliable Operation in Dirty Environments: Unlike optical sensors easily blinded by dust, grime, or oil mist, HTM sensors are virtually immune to contamination. Their magnetic sensing principle functions reliably where visibility is poor or conditions are harsh (foundries, machine shops, agricultural equipment).
- Extended Sensing Ranges: Compared to standard inductive sensors, HTM sensors can often achieve significantly longer sensing distances, especially when paired with a permanent magnet target. This provides greater flexibility in machine design and positioning.
- Speed and Precision: They offer high switching frequencies suitable for detecting very fast-moving targets. Their digital output provides a precise, unambiguous signal - the target is either present or not within the defined range.
- Non-Contact Operation: The fundamental advantage. No physical contact means eliminated friction, zero mechanical wear, and vastly extended operational lifespans. This translates directly to reduced downtime and maintenance costs.
- Position Sensing Versatility: Beyond simple presence detection, specific HTM types can discern the position or movement of magnetic targets. This makes them ideal for tasks like speed sensing (gears, shafts), linear position feedback (using multiple sensors or analog outputs), and end-of-travel detection.
- Direction Detection: Certain HTM sensors, particularly those utilizing the Hall-effect principle to detect magnetic pole changes, can determine the direction of movement of a magnetic target (e.g., North pole approaching vs. South pole).
- Barrier Penetration: They can detect magnetic targets through non-ferromagnetic materials like plastic, aluminum, or stainless steel enclosures, enabling sealed sensor designs or detection inside housings.
Pervasive Applications: Where HTM Sensors Shine
The unique strengths of HTM proximity sensors make them indispensable across a broad spectrum:
- Automotive Manufacturing & Systems: Engine timing control (camshaft/crankshaft position), gearbox position sensing, seat belt buckle detection, anti-lock braking systems (ABS - wheel speed sensing), transmission gear detection.
- General Industrial Automation: Position detection of cylinders (piston rod magnets), rotary encoders for motor feedback, conveyor line object counting, machine guarding (door position), spindle position, tool changer positioning.
- Перевозка материалов: Detecting the presence of metal pallets, cart position on automated lines, overhead crane positioning.
- Consumer Electronics: Smartphone flip cover detection (screen on/off), laptop lid close detection.
- White Goods: Washing machine drum position sensing, dishwasher door latch detection, fridge door open/closed status.
- Medical Equipment: Precision fluid level detection (using magnetic floats), component positioning in analyzers.
- Building Automation: Elevator car position sensing, door and gate position control, security systems.
Selecting the Right HTM Sensor: Critical Considerations
Choosing the optimal sensor requires careful evaluation:
- Sensing Distance: Maximum and minimum distances required for reliable detection.
- Target Type: Is it ferromagnetic (steel) or a permanent magnet? Size, shape, and material matter. Using a magnet typically provides longer, more reliable ranges.
- Output Type: Digital (PNP/NPN transistor, NO/NC) or Analog (voltage/current proportional to distance)? Digital is common for presence detection; analog is crucial for precise position feedback.
- Electrical Requirements: Operating voltage (e.g., 10-30V DC), current consumption, output current capability.
- Environmental Factors: IP rating (sealing against dust and water), temperature range, resistance to chemicals, shock/vibration tolerance.
- Mounting & Form Factor: Cylindrical, rectangular block, slot-style? How much space is available?
- Special Features: Direction detection, speed sensing capability, enhanced EMC protection, IO-Link communication for advanced diagnostics and parameterization.
Beyond the Basics: Advanced HTM Capabilities
The technology continues to evolve:
- Programmable Sensors: Some modern HTM sensors allow engineers to configure operating parameters like sensing range or output behavior via software, increasing flexibility.
- Analog Outputs (LVDT/RVDT principles): While Hall-effect is most common for digital outputs, similar “magnetostrictive” principles (often still categorized under HTM in broad terms) provide high-precision analog position feedback over longer linear or rotary strokes.
- Integrated Electronics (ASICs): Advanced Signal Conditioning Chips enable smaller sizes, lower power consumption, and enhanced noise immunity.
The Enduring Role of Magnetic Sensing
In a world increasingly focused on touchscreens and optical interfaces, the robust, contactless detection provided by HTM proximity sensors remains fundamentally vital. Their ability to perform reliably under challenging conditions, offer long sensing ranges, and provide precise digital or analog feedback ensures their continued dominance in demanding industrial applications, automotive systems, and beyond. From the factory floor to the smartphone in your pocket, HTM proximity sensors are the invisible, magnetic workhorses enabling seamless touchless interaction. Selecting and applying the right HTM sensor technology is crucial for engineers seeking durability, precision, and consistent performance in their automation and detection solutions.