датчик регулируемого приближения
- time:2025-07-03 00:00:04
- Нажмите:0
Unlock Precision and Flexibility: The Power of Adjustable Proximity Sensors
Ever get frustrated by a sensor detecting something too early, or worse, missing it entirely because its range is fixed? In countless applications, from delicate assembly lines to interactive displays, a “one-size-fits-all” detection distance just doesn’t cut it. This inherent limitation is precisely where adjustable proximity sensors step into the spotlight, transforming rigid automation into adaptable intelligence.
Unlike their fixed-range counterparts, adjustable proximity sensors offer a crucial capability: the ability to fine-tune their detection range or sensitivity. This seemingly simple feature unlocks unprecedented levels of flexibility, precision, and efficiency across a vast spectrum of industries. No longer confined to a single, predetermined operating point, these sensors empower engineers and designers to optimize performance dynamically for specific situations, materials, or environmental conditions.
Understanding the Core Advantage: Beyond Fixed Detection
Proximity sensors, in essence, detect the presence or absence of an object within a specific field without physical contact. Common types include:
- Inductive: Detect metallic objects using electromagnetic fields.
- Capacitive: Detect both metallic and non-metallic objects (liquids, plastics, wood) by measuring changes in capacitance.
- Photoelectric (Optical): Use light beams (visible, infrared, laser) to detect objects based on light reflection (retro-reflective) or interruption (through-beam).
- Ultrasonic: Emit sound waves and detect their reflection to gauge distance or presence.
The defining characteristic of an adjustable proximity sensor is its user-modifiable core operating parameter: its sensing distance or sensitivity threshold. This adjustment allows tailoring the sensor’s active zone – the space within which it reliably detects a target object.
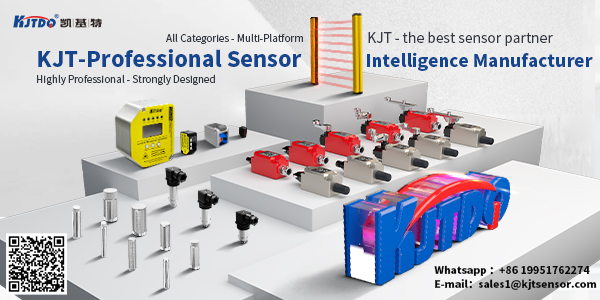
How Adjustability Makes a Difference (Mechanisms and Benefits)
The methods for adjustment vary by sensor type but commonly involve:
- Potentiometers: A physical dial or screw on the sensor housing manually alters internal circuit parameters (like amplification gain or comparator threshold), directly changing the sensing distance.
- Teach-in Buttons: Pushing a button while placing the target object at the desired detection point programs the sensor to recognize that specific distance as its new trigger point. Highly intuitive and common.
- Programmable Logic Controller (PLC) / Digital Interfaces: Sensors with communication capabilities (like IO-Link) allow software-based adjustment of parameters such as switching points, hysteresis, and even output behavior directly from the control system. This enables remote configuration and diagnostics.
The benefits of this adjustability are transformative:
- Optimized Performance: Achieve the perfect detection distance for a specific application. Avoid nuisance triggers from distant objects (over-sensing) or missed detections (under-sensing). For instance, in a bottling plant, adjust sensors to reliably detect glass bottles without triggering on the moving conveyor belt itself.
- Material & Surface Flexibility: Capacitive sensors can be tuned to ignore certain materials (like a container wall) while detecting the desired material inside (e.g., liquid level). Optical sensors can adjust sensitivity to work reliably with different colored or textured targets.
- Compensation for Variability: Account for mechanical tolerances, target positioning inconsistencies, wear and tear over time, or varying environmental factors (like temperature affecting ultrasonic performance). Adjustability provides valuable operational headroom.
- Simplified Installation & Maintenance: Instead of physically moving a fixed sensor during setup or troubleshooting, simply adjust its range electronically. This reduces downtime and mechanical adjustments. Teach-in functions make field commissioning remarkably quick.
- Enhanced Multi-Purpose Use: A single adjustable sensor model can often serve multiple different applications within a facility by simply reprogramming its range or sensitivity, reducing inventory complexity and cost.
Where Adjustable Proximity Sensors Shine (Key Applications)
The versatility of adjustable proximity sensors makes them indispensable in numerous scenarios:
- Industrial Automation & Robotics:
- Precision Assembly: Fine-tune detection for tiny components or critical alignment tasks (e.g., microchip placement).
- Conveyor Sorting: Accurately detect objects of varying sizes or heights without repositioning sensors for each product line changeover.
- Robot Guidance: Adjust sensing range for safe proximity detection or precise object picking at different distances.
- Fill Level Control: Tune capacitive sensors to detect specific liquids precisely within containers, ignoring the container material or foam.
- Consumer Electronics & Appliances:
- Touchless Controls: Adjust sensitivity on faucets, soap dispensers, or hand dryers for reliable activation without accidental triggers.
- Interactive Displays/Kiosks: Set optimal range for gesture detection, preventing interaction when users are just walking by.
- Automatic Doors/Gates: Fine-tune opening/closing sensitivity based on installation environment and typical user flow.
- Security & Safety Systems:
- Intrusion Detection: Configure perimeter sensors to ignore small animals but detect humans within a critical zone.
- Safety Light Curtains/Mats: Adjust muting zones to allow safe passage of materials while ensuring worker protection.
- Material Handling & Packaging:
- Web Guiding: Precisely detect the edge of moving material (film, paper, foil) despite width variations or flutter.
- Object Counting/Presence: Ensure reliable counting of packages or products on high-speed lines by tuning out background vibration or reflections.
- Automotive: Adjust sensors for parking assistance systems, foot-operated tailgates (kick sensors), or occupant detection systems to perform reliably under various conditions.
Choosing and Implementing Effectively: Key Considerations
While highly versatile, maximizing the value of adjustable proximity sensors requires careful selection and setup:
- Type Matters: Match the sensor type (inductive, capacitive, photoelectric, ultrasonic) to your target material and environment first. Then ensure it has the necessary adjustability (pot, teach-in, digital).
- Range Capability: Verify the total possible adjustment range meets your application’s requirements. Does it cover the minimum and maximum distances needed?
- Resolution & Repeatability: How fine-grained is the adjustment? Can it be set reliably to the exact same point repeatedly? High-precision tasks demand fine resolution and excellent repeatability.
- Environmental Robustness: Ensure the sensor housing (IP rating), temperature range, and resistance to chemicals/vibration suit the operational environment.
- Output Configuration: Does it provide the required output signal (PNP/NPN, analog, IO-Link) for your control system?
- Calibration & Documentation: After adjustment, clearly document the settings if applicable. For critical applications, periodic re-checking (especially after maintenance or environmental shifts) is wise.
The Indispensable Tool for Modern Sensing Needs
Fixed proximity sensors served us well, but the demand for agility, precision, and efficiency continues to rise. Adjustable proximity sensors are not merely a minor upgrade; they represent a fundamental shift towards intelligent, adaptable sensing. By empowering users to tailor detection parameters to the exact needs of the moment, they unlock solutions that are more reliable, more versatile, and ultimately, more cost-effective. From preventing costly production errors to enabling seamless user interactions, the ability to fine-tune detection distance or sensitivity is rapidly becoming not just an advantage, but an essential requirement in an increasingly dynamic technological landscape.