ac proximity sensor
- time:2025-07-02 01:42:43
- Нажмите:0
AC Proximity Sensors: The Non-Contact Detection Powerhouse in Industrial Automation
Think about the technology silently orchestrating the world around you – from the elevator doors that open seamlessly to the intricate dance of robots on a factory floor. Often hidden from view, proximity sensors are the unsung heroes enabling countless automated processes. Among these, AC proximity sensors stand out as a particularly robust and reliable solution, indispensable in demanding industrial environments. Unlike their optical or ultrasonic cousins, AC inductive proximity sensors excel where dirt, dust, moisture, or vibration are constant companions. This article dives into the core principles, advantages, and critical applications of these workhorses of non-contact detection.
Demystifying the AC Proximity Sensor: Core Technology
An AC proximity sensor is a specific type of индукционный датчик приближения that operates using an alternating current (AC) power supply. Its fundamental purpose is to detect the presence (or absence) of metallic objects without any physical contact, making it ideal for wear-free operation in tough conditions.
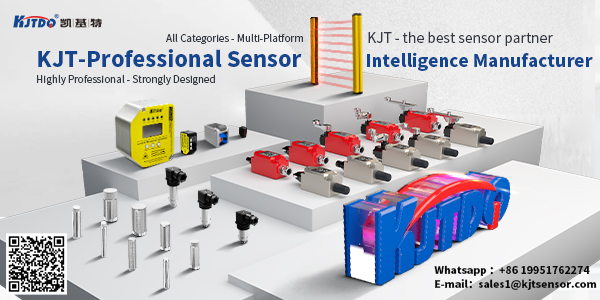
How Do AC Proximity Sensors Work?
The operation hinges on Faraday’s Law of Electromagnetic Induction and the principles of eddy currents:
- The Coil & Oscillator: At the sensor’s core lies a coil wound around a ferrite core. When powered by AC voltage, an oscillator circuit generates a high-frequency alternating magnetic field radiating out from the active sensing face.
- The Target Effect: When a metallic object (the “target”) enters this oscillating magnetic field, electromagnetic induction occurs. This induces swirling electrical currents called eddy currents on the target’s surface.
- Energy Absorption: The creation of these eddy currents absorbs energy from the sensor’s oscillating magnetic field. This energy loss or damping effect directly impacts the oscillator circuit.
- Signal Detection: An internal amplifier and detector circuit continuously monitors the amplitude of the oscillation. As the target approaches, the oscillation weakens due to the damping effect. Once the damping reaches a preset threshold (corresponding to the sensor’s specified sensing range), the detector triggers a state change.
- Output Switching: Typically, this state change controls a solid-state output switch (like a transistor). The AC sensor usually provides an alternating current output signal proportional to its supply voltage when activated. This output change signals the presence of the metal target to a controller (like a PLC).
Why Choose AC? Key Advantages Over DC Counterparts
While DC (Direct Current) inductive proximity sensors are incredibly common, AC models offer distinct advantages in specific scenarios:
- Robustness Against Electrical Noise: Industrial environments are often electrically noisy. High-power motors, variable frequency drives (VFDs), and welding equipment generate significant electromagnetic interference (EMI). AC sensors, inherently operating with an alternating field, are generally more resistant to this type of interference compared to some DC sensors, leading to fewer false triggers and more reliable operation. Their immunity to contact welding is also a plus.
- Inherent Current Limiting: AC sensors often exhibit a degree of inherent current limitation. When activated, their output impedance increases under overload conditions (e.g., a short circuit). While not foolproof protection, this characteristic provides a basic level of safeguarding for the sensor and associated wiring without needing an external fuse in many cases. This contrasts with DC PNP/NPN outputs that can typically sink or source high currents continuously unless externally protected.
- Simple Driving of AC Loads: Some specific applications involve directly controlling AC-powered devices like solenoids or small contactors. An AC proximity sensor’s output can sometimes directly interface with these AC loads without needing an intermediate relay, simplifying wiring and reducing component count. (Note: Always check sensor load specifications).
- Suitability for Older Systems: In facilities with legacy equipment originally designed around AC control circuits, AC sensors provide direct compatibility, avoiding the need for signal converters.
Where AC Proximity Sensors Shine: Primary Applications
Their unique blend of non-contact detection, metal-sensing capability, and resilience makes AC inductive proximity sensors vital across numerous industrial sectors:
- Metal Detection & Positioning: Foundational to their function. Used countless times per minute to:
- Detect the presence, passage, or precise position of metal parts on conveyor belts or assembly lines (gears, pistons, tools, etc.).
- Confirm the open/closed state of metal valves or doors.
- Position control of metal components within machinery or on transfer systems.
- Machine Safety & Monitoring: Providing critical inputs for safeguarding operations:
- Verifying safety guards or access panels (metal) are securely closed before machine start-up.
- Providing end-of-travel detection for cylinders or moving parts to prevent over-travel damage.
- Monitoring rotating shafts or equipment for speed or presence via detection of bolts, keys, or other metal features.
- Material Handling & Robotics: Enabling automation in logistics and manufacturing:
- Detecting metal pallets, carts, or AGVs (Automated Guided Vehicles) to trigger loading/unloading sequences or automated doors.
- Providing positional feedback for robotic arms manipulating metal objects or operating within metallic frameworks.
- Counting metal packages or components.
- Automotive & Heavy Machinery: Withstanding harsh environments critical to this sector:
- Engine assembly line part verification.
- Position sensing of hydraulic cylinders on construction or agricultural equipment.
- Detecting metal components during painting or coating processes.
- Monitoring fluid levels via detection of a metal float.
- Metalworking & Fabrication: Thriving amidst the chaos of metal shops:
- Detecting the presence of metal sheets on feed tables for stamping presses or laser cutters.
- Confirming correct positioning of metal blanks or formed parts.
- Tool breakage detection (detecting the sudden absence of a rotating metal tool).
- Safety interlocks on CNC machine tool doors.
The Tangible Benefits Driving Adoption
The widespread use of AC proximity sensors is underpinned by concrete operational benefits:
- Non-Contact Operation: Eliminates mechanical wear and tear, ensuring long service life and reducing maintenance costs.
- High Reliability & Repeatability: Provides consistent and accurate detection cycles, often numbering in the millions, essential for process stability.
- Resilience: Capable of operating in demanding conditions: oily, dusty, damp environments where optical sensors might fail. Their robust housings (typically stainless steel, nickel-plated brass, or specialized plastics) offer protection against impacts and harsh chemicals.
- Fast Response Times: Capable of detecting objects at high speeds, making them suitable for fast-moving production lines.
* **