Сенсор PNP
- time:2025-07-01 14:58:35
- Нажмите:0
PNP Sensors: The Positive Switching Solution for Industrial Automation
Ever wondered what makes a machine stop automatically when you get too close, or how a robotic arm precisely picks up a component on a fast-moving conveyor belt? Behind these vital safety features and precision operations often lies an unsung hero: the PNP sensor. This specific type of proximity or photoelectric sensor plays a fundamental role in countless industrial automation tasks, prized for its reliability and straightforward integration. Understanding what a PNP sensor is and why it dominates many factory floors is key to optimizing automated systems.
Decoding PNP: The “Sourcing” Sensor
At its core, the designation “PNP” refers to the type of transistor output stage used within the sensor. It describes the internal electronic switch responsible for conveying the sensor’s state (detected or not detected) to the machine’s control system, typically a Programmable Logic Controller (PLC) or similar controller.
Imagine a simple switch. A PNP sensor acts like a switch connected between the positive supply voltage (+V, often 24V DC in industrial settings) and the output signal line leading to the controller. Here’s how it functions:
- No Target Detected: The internal PNP transistor is “off” or non-conducting. The output signal line is electrically disconnected from the positive supply voltage (+V). In this state, the output signal line essentially “floats” or is pulled low (to 0V) through a resistor in the controller’s input card. The controller reads this as a logical LOW or OFF state.
- Target Detected: When the sensor activates (e.g., a metal object enters its sensing field, or a light beam is interrupted), the internal PNP transistor turns “on” or becomes conducting. This effectively closes the switch, connecting the output signal line directly to the positive supply voltage (+V). The controller now sees +V (24V) on its input, interpreting this as a logical HIGH or ON state.
In essence, a PNP sensor sources current from the positive supply to the load (the controller’s input circuit) when activated. It provides the positive voltage signal. This characteristic earns it the nickname the “sourcing sensor”.
PNP vs. NPN: Understanding the Critical Difference
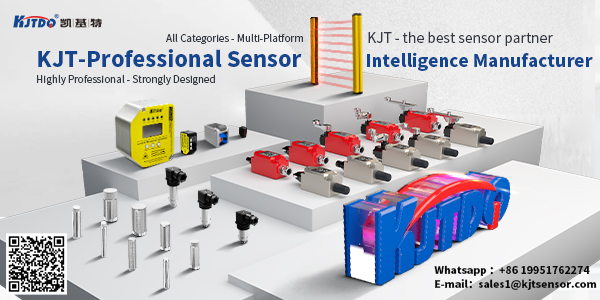
PNP sensors are frequently discussed alongside their counterpart: NPN sensors. The fundamental difference lies in the transistor type and, consequently, how they switch the circuit:
- PNP (Sourcing): Switches the positive voltage (+V) to the load/output line. Output is HIGH (+V) when active.
- NPN (Sinking): Switches the negative voltage (0V/GND) to the load/output line. Output is LOW (0V) when active (connects the load to ground).
While functionally opposite, both serve the same purpose: signaling detection. However, the choice between PNP and NPN has significant practical implications.
Why PNP Sensors Dominate Industrial Applications
Several factors contribute to the widespread preference for PNP sensors in industrial automation, particularly in regions like Europe and North America:
- Compatibility with Conventional PLC Inputs: Many traditional PLC input modules are designed with “sinking” inputs. This means they expect to be connected to a sourcing field device (like a PNP sensor) that provides the positive voltage when active. Connecting a PNP sensor to a sinking input is straightforward: the sensor output wire connects to the PLC input terminal, and the PLC input’s internal circuit provides the connection to ground (0V), completing the circuit when the sensor activates. This natural compatibility simplifies wiring and reduces component count.
- Reduced Risk of Ground Loops: Because the PNP sensor switches the positive leg of the supply, the sensor housing and its associated wiring (like the shield in a cable) are typically connected to ground (0V) at the sensor end. NPN sensors, switching the ground leg, often require their 0V reference to be connected at the load (PLC) end. The PNP configuration generally makes it easier to maintain a single, consistent grounding point, minimizing the risk of troublesome ground loops, which can cause erratic signal behavior or noise interference.
- Enhanced Noise Immunity (Perceived): While both types can be designed for high noise immunity, the nature of switching the positive voltage is often perceived as less susceptible to certain types of electrical interference common in industrial environments compared to switching the ground path. Robust performance is paramount where electromagnetic noise from motors, drives, and welding equipment is prevalent.
- Safety Considerations (Certain Cases): In specific safety-related circuits involving multiple contacts in series (like emergency stop chains), PNP configurations can sometimes offer advantages in diagnosing faults related to wire breaks, though modern safety relays handle both types effectively. The primary safety advantage often lies in the simpler, more robust wiring reducing potential failure points.
Wiring a PNP Sensor: Keeping it Simple
The typical wiring for a standard 3-wire DC PNP sensor is intuitive and reflects its sourcing nature:
- Brown Wire: Connect to the Positive (+) Supply Voltage (e.g., +24V DC).
- Blue Wire: Connect to the Power Supply Common (0V/Ground).
- Black Wire: This is the Output Signal Line. Connect this wire to the input terminal on your PLC or control device. The PLC input itself is configured (internally or via wiring) to connect this terminal to 0V/Ground through its internal circuitry (sinking input).
When the sensor detects its target, the black wire becomes electrically connected to the brown wire (+24V), sending that positive voltage signal to the PLC input.
Ubiquitous Applications: Where You Find PNP Sensors
The reliability, noise immunity, and compatibility of PNP sensors make them ideal for countless industrial tasks:
- Object Detection: Count bottles on a conveyor, detect the presence of a pallet, confirm a part is in place for machining. Proximity sensors (inductive, capacitive) and photoelectric sensors (through-beam, retro-reflective, diffuse) dominate here.
- Position Feedback: Verify cylinder rod position (piston detection), confirm doors are closed, ensure guards are in place. Position verification is critical for safety and sequencing.
- Level Sensing: Detect bulk material levels in bins or tanks.
- End-of-Stroke Detection: Signal when a linear actuator or cylinder has reached its extended or retracted position.
- Automotive Manufacturing: Used extensively in assembly lines for part positioning, robot guidance, and safety interlocking.
- Packaging Machinery: Detecting boxes, controlling fill levels, tracking labels.
- Перевозка материалов: Monitoring conveyor speeds, detecting jams, controlling sorting gates.
Choosing Right: PNP vs. NPN - The Key Question
The choice between PNP and NPN ultimately boils down to your PLC or controller’s input configuration:
- If your controller has Sinking Inputs, you need Sourcing Output sensors: **PNP Sensors