autonics proximity sensor
- time:2025-07-01 14:04:28
- Нажмите:0
Autonics Proximity Sensors: The Unsung Heroes of Reliable Object Detection
Imagine a high-speed bottling line humming smoothly. Bottles zip past filling stations, capping heads descend with perfect timing, labels are applied without a hitch. What ensures this intricate dance happens flawlessly, preventing collisions and guaranteeing each step occurs only when the bottle is truly present? Often, the answer lies in the quiet vigilance of Autonics proximity sensors.
These unassuming devices are fundamental components in countless industrial automation and machinery applications. Before delving into why Autonics stands out, let’s clarify their core function. An Autonics proximity sensor is a non-contact sensing device designed to detect the presence or absence of a target object (typically metal for inductive types) within its sensing range without physical contact. They achieve this by emitting an electromagnetic field or beam and monitoring changes caused by the target’s approach. The key outputs are simple: a solid-state switch activates (ON) when the target is within range and deactivates (OFF) when it moves away, providing a crucial signal to a PLC (Programmable Logic Controller) or other control system.
Why Autonics Proximity Sensors Command Respect in Industrial Settings
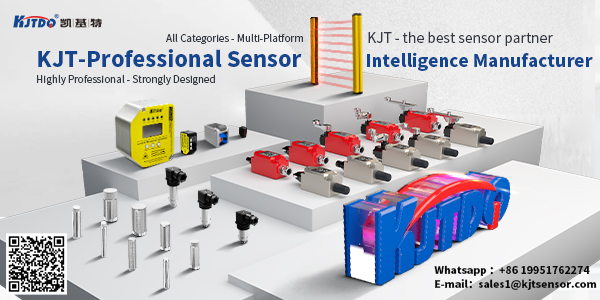
While many manufacturers offer proximity sensors, Autonics has carved a significant niche through a relentless focus on core principles essential for demanding environments:
- Exceptional Reliability & Durability: Operating on factory floors means exposure to vibration, electrical noise, temperature fluctuations, and potential physical impact. Autonics designs its sensors with robust housings, often featuring stainless steel (particularly beneficial in corrosive environments or food processing), and high-grade plastics. Their internal circuitry is hardened against electrical interference (EMI/RFI), minimizing false triggering – a critical factor for maintaining uptime. High IP (Ingress Protection) ratings (like IP67 and IP69K) ensure resistance against dust and high-pressure water jets, making them suitable for washdown environments common in food & beverage or pharmaceutical applications.
- Consistent, Accurate Detection: Repeatability and sensing stability are paramount. Autonics proximity switches provide dependable object detection cycle after cycle, ensuring machines operate precisely as programmed. Their tight manufacturing tolerances guarantee that the specified sensing distance is consistently achieved under defined conditions. This accuracy translates directly to process reliability.
- Wide Range of Sensing Technologies & Models: Understanding that one size doesn’t fit all, Autonics offers a comprehensive portfolio:
- Inductive Proximity Sensors: The workhorses for detecting metallic targets (ferrous and non-ferrous). Autonics provides these in various shapes (cylindrical, block, rectangular), sizes (including ultra-compact options), sensing distances, and output configurations (NPN/PNP, NO/NC).
- Capacitive Proximity Sensors: These detect a much wider range of materials, including liquids, powders, plastics, and wood, by sensing changes in capacitance. Ideal for level detection in tanks or presence detection of non-metallic objects.
- Magnetic Proximity Sensors (Reed Switches): Designed specifically to detect the presence of a magnetic field, often used with small magnets embedded in cylinders or actuators.
- Optimized Performance Features: Autonics integrates features that enhance usability and longevity:
- Short-Circuit and Reverse Polarity Protection: Safeguards the sensor and connected circuitry from wiring errors or faults, reducing downtime and maintenance costs.
- LED Status Indicators: Built-in LEDs provide clear visual confirmation of power status and output state, simplifying installation, commissioning, and troubleshooting.
- Temperature Stability: Engineered to perform reliably across broad temperature ranges typical of industrial settings.
Choosing the Right Autonics Proximity Sensor: Key Considerations
Selecting the optimal sensor involves matching its capabilities to the application’s demands:
- Target Material: Is the object metallic? Choose inductive. Is it non-metallic (liquid, plastic, wood, etc.)? Choose capacitive. Need to sense a magnet? Choose magnetic.
- Sensing Distance: What is the required distance between the sensor face and the target? Select a model whose nominal sensing range (Sn) comfortably exceeds the actual operating distance, accounting for installation tolerances and potential target variations. Never size exactly to the maximum required distance.
- Environmental Conditions: Consider temperature extremes, potential for water/dust ingress (requiring high IP ratings), exposure to chemicals or oils, and levels of vibration or shock. Autonics sensors are rated for specific environmental resilience – ensure the chosen model matches or exceeds the conditions.
- Size and Mounting Constraints: Space is often limited. Autonics offers cylindrical sensors in various thread sizes (M5, M8, M12, M18, M30 are common) and compact block-style designs. Ensure the physical dimensions and mounting method (flush or non-flush for inductive) are suitable for the location.
- Electrical Requirements: Match the sensor’s operating voltage (common DC ranges like 10-30VDC) and output type (NPN sinking, PNP sourcing - crucial for compatibility with the PLC input card) and switching function (Normally Open - NO, or Normally Closed - NC) to the control system.
- Output Configuration: While standard 3-wire (power, ground, signal) DC models are most common, Autonics also offers specialized variants like 2-wire AC/DC or analog output sensors for specific needs.
Beyond Presence: Smart Integration for Enhanced Automation
The primary role is object detection, but Autonics proximity sensors enable far more sophisticated control:
- Position Verification: Confirming an actuator has fully retracted/extended, a part is loaded in a fixture, or a door is closed.
- Counting: Tracking items moving on a conveyor.
- Speed Monitoring: Detecting the rotation of gears or shafts.
- End-of-Travel Detection: Safely halting motion at the limits of travel.
- Jamming Prevention: Ensuring parts are progressing correctly through a machine sequence.
The Autonics Advantage: Precision You Can Trust
In the intricate world of automation, where milliseconds matter and unplanned stops cost money, the reliability of core components like proximity sensors is non-negotiable. Autonics proximity sensors deliver that essential reliability. Their focus on robust construction, consistent performance accuracy, resistance to harsh industrial environments, and a broad portfolio tailored to diverse applications makes them a trusted choice for engineers and maintenance professionals worldwide. From controlling high-speed packaging machinery to ensuring safety in material handling systems, these sensors provide the critical, non-contact detection foundation upon which efficient, modern automation is built. Selecting the right one, based on a clear understanding of the target, environment, and required signal, unlocks significant benefits in operational efficiency and process control.