датчик высокотемпературного сближения
- time:2025-07-01 12:22:03
- Нажмите:0
Surviving the Heat: How High Temperature Proximity Sensors Revolutionize Industrial Automation
Imagine a critical metal casting line grinding to a halt. Molten metal flows, temperatures soar beyond 1500°F (815°C), and a standard proximity sensor, overwhelmed by the intense heat, fails catastrophically. Production stops, costs escalate, and downtime looms large. This scenario underscores the critical need for a specialized class of industrial heroes: high temperature proximity sensors. Designed to thrive where others melt, these rugged devices are the unsung enablers of efficiency and safety in the most thermally demanding environments.
Unlike their standard counterparts, which typically operate reliably up to about 70-85°C (158-185°F), high temperature proximity sensors are engineered to withstand ambient temperatures ranging from 150°C (302°F) to a staggering 250°C (482°F), with some specialized variants pushing even higher. This capability isn’t just about surviving; it’s about delivering consistent, accurate proximity detection in the heart of furnaces, near forging presses, along glass production lines, within engine test cells, or amidst automotive paint curing ovens.
The Core Challenge: Taming Extreme Environments
Standard sensors succumb to heat in several ways. Electronic components degrade, plastic housings deform or melt, and inductive coils lose their magnetic properties. High temperature proximity sensors overcome these limitations through deliberate design choices:
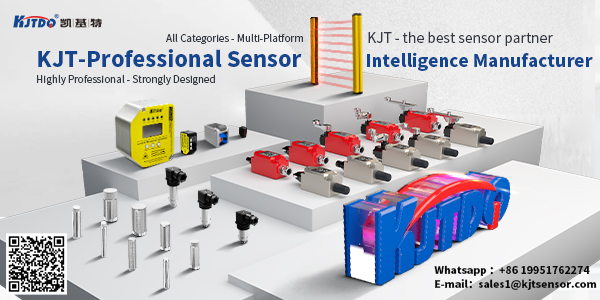
- Advanced Materials: The key lies in specialized construction. High-temperature ceramics replace standard plastics for housings and sensing faces. These ceramics offer exceptional thermal stability and resistance to thermal shock. Wires are sheathed in high-temp insulation like PTFE or fiberglass. Seals utilize specialized elastomers or metal-to-metal bonding to prevent ingress and withstand expansion/contraction cycles.
- Robust Sensing Elements: Inductive sensors, the most common type for metallic target detection in harsh environments, utilize coils wound with high-temperature wire and cores made from rare earth magnets or alloys that retain their magnetic properties at elevated temperatures. Capacitive sensors for non-metallic detection use ceramic or quartz substrates.
- Thermal Management & Circuitry: Designs often incorporate thermal barriers or heat sinks to protect the most sensitive internal electronics. Signal processing circuits are carefully selected or designed for thermal stability, ensuring the output signal remains reliable despite the ambient heat. Auto-tuning capabilities can compensate for temperature drift in some advanced models.
Primary Technologies in the Hot Zone
While inductive sensors dominate for metal detection, other technologies play vital roles:
- Inductive Sensors: The workhorse for high-temp metal detection. Their non-contact operation and insensitivity to dust, dirt, and splashes (when properly rated) make them ideal for foundries, forging, and heat treatment. Look for high temperature inductive proximity sensors specifically rated for your application’s maximum ambient temperature.
- Capacitive Sensors: Essential for detecting non-metallic objects (plastics, glass, liquids, wood chips) in hot environments like food processing ovens, plastic extrusion lines, or paper mills near dryers. They require careful tuning to ignore background effects but offer versatility.
- Magnetic Sensors (Reed Switches / Hall Effect): Used where permanent magnets can be attached to the target. Typically simpler and can be made very robust for high temperatures, often found on cylinder position feedback in hot machinery. Hermetically sealed versions excel here.
- Fiber Optic Sensors: While the sensor head itself can be engineered for extreme heat (using quartz or sapphire), the vulnerable electronics (amplifier) are remotely located in a cooler area. This makes them uniquely suited for ultra-high temperature applications (>250°C) like inside vacuum furnaces or turbine monitoring.
Where High Heat Sensors Are Essential
The applications demanding these rugged sensors are diverse and mission-critical:
- Metal Processing: Foundries (molten metal level, mold position), Forging (press position, billet presence), Rolling Mills (strip position, coil handling), Heat Treatment (quench tank level, part transfer position). Consistent detection prevents jams and ensures process control under intense heat.
- Glass Manufacturing: Position sensing near melting furnaces, mold handling in hot forming areas, annealing lehrs. Resistance to heat and infrared radiation is crucial.
- Automotive: Engine test cells (component position under hood heat), Paint Shops (curing oven conveyor tracking, door position), Brake testing. Durability prevents costly test interruptions.
- Plastic & Rubber: Extrusion lines (melt flow, cutter position near hot dies), Vulcanization presses (mold closure detection), Blow Molding. Sensors must handle heat and potential chemical exposure.
- Energy: Gas turbine monitoring, boiler systems, geothermal plants. Reliability ensures safety and operational efficiency.
- Food & Beverage: Baking ovens (conveyor jam detection, product presence), Retort processing (sterilization vessel monitoring), Drying tunnels. Hygiene ratings (like IP69K) combined with high-temperature tolerance are often required.
Choosing the Right High Temperature Proximity Sensor
Selecting the optimal sensor involves careful consideration beyond just the maximum ambient temperature rating:
- Actual Operating Temperature: Don’t just consider ambient air temperature. Account for radiant heat from nearby equipment or processes, which can be significantly higher. Always include a safety margin.
- Target Material & Detection Distance: Inductive for metal, capacitive for non-metals. Ensure the required sensing range is achievable under operating temperatures.
- Environmental Factors: Exposure to coolants, oils, chemicals, water jets, steam, or abrasive particles? Choose the appropriate IP rating (Ingress Protection) and housing material. Splash resistance is often critical near hot processes.
- Electrical Requirements: Voltage, output type (PNP/NPN, NO/NC), connection type (cable, connector).
- Physical Constraints: Size, mounting style (flush, non-flush), and available space.
- Duty Cycle: Will the sensor be exposed to peak temperatures continuously or intermittently? This affects longevity.
The Future: Smarter Sensors in the Heat
Advancements continue to push the boundaries. Integration of IO-Link communication allows high temperature proximity sensors to provide diagnostic data (like temperature warnings, signal strength) alongside the standard switch signal, enabling predictive maintenance. Materials science promises housings and components resilient to even more extreme conditions. Furthermore, intelligent compensation algorithms within the sensors themselves are becoming more sophisticated, ensuring unwavering accuracy across the entire operating temperature spectrum.
In essence, high temperature proximity sensors are not merely components; they are mission-critical enablers. They perform the fundamental, yet vital, task of presence detection in environments where standard electronics fail, allowing complex, high-heat industrial processes to run reliably, efficiently, and safely. Their robust design and specialized engineering make the invisible automation within blistering furnaces, roaring forges, and scorching ovens not just possible, but predictable and profitable. Investing in the right sensor for the specific thermal challenge translates directly into reduced downtime, lower maintenance costs, and enhanced operational resilience.