Переключатель приближения клапана
- time:2025-07-01 02:23:02
- Нажмите:0
Valve Proximity Switches: The Silent Guardians of Process Control
Imagine your facility’s intricate network of pipes and valves as its circulatory system. Like a nervous system constantly reporting back to the brain, knowing the precise state – open or closed – of each critical valve is paramount. This is where the unassuming yet vital Переключатель приближения клапана steps into the spotlight. Far more than a simple on/off indicator, this sophisticated sensor acts as a watchful sentinel, providing essential feedback for automation, safety, and efficiency in countless industrial applications. Neglecting its role is akin to operating machinery blindfolded – a risky proposition indeed.
Decoding the Valve Proximity Switch
At its core, a valve proximity switch is an electronic sensor designed specifically to detect the precise position of a valve’s moving component – typically the stem or actuator – without any physical contact. This “non-contact” principle is fundamental. Instead of mechanical levers or pushbuttons that can wear out, it relies on detecting the presence (or absence) of a metallic target attached to the valve mechanism as it moves between its open and closed positions.
The Mechanism: Sensing Without Touching
The most common and robust type used for valve position sensing is the индукционный датчик приближения. Here’s a simplified breakdown of its operation:
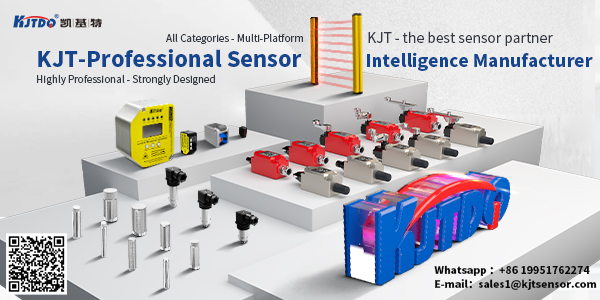
- Generating the Field: Inside the sensor’s head, an electronic oscillator generates a high-frequency alternating electromagnetic field that radiates from its sensing face.
- Target Interaction: When a metallic target (usually ferrous steel, but specific sensors work with non-ferrous metals too) attached to the valve stem moves into this active field area…
- Field Disturbance: …the target induces eddy currents within itself. This interaction absorbs energy from the oscillator’s electromagnetic field.
- Detection and Signal: The sensor’s circuitry continuously monitors the strength of this oscillating field. The energy loss caused by the eddy currents dampens the oscillation amplitude.
- Output Change: Once the damping reaches a predefined threshold (indicating the target is sufficiently close), the sensor’s solid-state electronic switch (like a transistor) instantly changes state. This means its output signal flips – typically from “OFF” (Open Circuit or 0V) to “ON” (Closed Circuit or supply voltage, e.g., 24V DC), or vice-versa depending on configuration.
- Valve Position Confirmation: This clean, fast, and bounce-free electrical signal is sent to the plant’s control system (PLC, DCS), providing unambiguous real-time confirmation of whether the valve is fully open, fully closed, or potentially even in an intermediate position if multiple sensors are used.
Why Non-Contact Sensing is a Game-Changer
The non-contact nature of inductive proximity switches offers significant advantages over traditional mechanical limit switches for valve position feedback:
- Exceptional Reliability & Longevity: No moving parts to wear, break, or jam. No contact bouncing leading to false signals. Built for millions of reliable switching cycles.
- High Resistance to Contaminants: Sealed housings (typically IP67, IP68, IP69K) protect against dust, dirt, oil, coolants, and high-pressure washdowns, making them ideal for harsh industrial environments common around valves.
- Vibration Immunity: Impervious to vibration that could cause false trips or damage mechanical switches.
- Fast Response Time: Provides near-instantaneous detection and signal output, critical for high-speed processes or safety interlocks.
- Maintenance Reduction: Eliminates the need for frequent adjustment or replacement of mechanical contacts.
Ubiquitous Applications: Where Valve Position Matters
Valve position feedback via proximity switches is indispensable across diverse sectors:
- Process Industries (Chemical, Petrochemical, Oil & Gas): Monitoring critical block valves, control valves, emergency shutdown (ESD) valves, and isolation valves for process control, safety interlocks, and leak prevention. Confirming valve status is fundamental for Safety Instrumented Systems (SIS).
- Water & Wastewater Treatment: Controlling flow through gates, butterfly valves, and ball valves for intake, treatment stages, and discharge.
- Power Generation: Managing water, steam, and fuel lines in boilers, turbines, and cooling systems.
- Manufacturing & Automation: Activating processes based on valve position in assembly lines, paint shops, material handling, and machine tools (coolant control).
- Pharmaceutical & Food & Beverage: Ensuring proper valve sequencing in hygienic processes, adhering to strict cleanliness standards (using specialized stainless steel housing sensors).
The Tangible Benefits: More Than Just a Signal
Implementing reliable valve proximity sensors delivers concrete operational advantages:
- Enhanced Process Control: Accurate valve position data is fundamental for closed-loop control systems and sequence logic. Knowing a valve is actually closed before proceeding to the next step prevents errors and spills.
- Boosted Safety: Provides critical feedback for safety interlocks. For instance, ensuring a drain valve is closed before pressurizing a line, or confirming an ESD valve has actuated during an emergency shutdown.
- Increased Operational Efficiency: Reduces process downtime caused by manual valve position checks or undetected valve malfunctions. Enables automated diagnostics.
- Predictive Maintenance Insights: Monitoring the timing of valve actuation (open/close signals) can reveal developing issues like sticking stems or failing actuators before they cause a breakdown.
- Reduced Maintenance Costs: The inherent robustness and longevity of proximity switches significantly lowers maintenance requirements compared to mechanical alternatives.
Choosing and Implementing Wisely
Selecting the right valve proximity switch involves key considerations:
- Sensor Type: Inductive is most common for metal valve stems/actuators. Ensure the target material (steel, stainless, aluminum) is compatible with the sensor’s specifications.
- Sensing Range: The distance at which the sensor reliably detects the target. Must accommodate the valve’s stroke and mounting constraints.
- Mounting: Options include threaded barrels (e.g., M8, M12, M18, M30), flat-pack, or block designs. Must withstand vibration and environmental exposure. Adjustable brackets are often crucial for precise alignment.
- Electrical Output: Typically PNP (sourcing) or NPN (sinking) DC transistor outputs compatible with the control system’s input cards. Commonly 3-wire configurations (Supply +, Supply -, Signal).
- Housing Material: Stainless steel (V4A/AISI 316L) offers superior corrosion resistance for demanding environments.
- Environmental Ratings: Essential IP (Ingress Protection) rating for dust/water and temperature range suitability.
- Connection Style: Pre-wired cables or connectors (like M12).
Proper installation is critical: precise mounting for reliable target detection, secure wiring, and protection against mechanical damage ensure the Переключатель приближения клапана delivers its intended performance. It’s not merely an accessory; it’s the essential link transforming physical valve movement into actionable intelligence for the modern automated plant.