Сварочный датчик приближения иммунитета
- time:2025-07-01 01:01:22
- Нажмите:0
Weld Immune Proximity Sensors: Your Ultimate Defense Against Industrial Interference
Imagine this: a critical robotic welding cell, arcs flashing, metal fusing. This intense environment generates an invisible storm – a maelstrom of intense electromagnetic interference (EMI), scorching spatter, and punishing physical shocks. Standard inductive proximity sensors, the workhorses of factory automation, often falter here. Erratic signals, premature failures, and costly downtime become unwelcome constants. This is the battlefield where Сварочный датчик приближения иммунитета emerge not just as components, but as essential survival gear for reliable automation. They are engineered specifically to shrug off the harsh realities of environments dominated by resistance welding (spot welding, projection welding) and robotic arc welding processes.
The Invisible Enemy: Why Welding Wreaks Havoc on Sensors
Understanding the necessity for weld immunity requires appreciating the sheer brutality of the welding environment on standard electronics:
- Electromagnetic Interference (EMI): Welding, especially high-current processes like spot welding, creates massive, rapidly fluctuating electromagnetic fields. These fields can induce false voltages within nearby sensor circuitry, causing phantom object detections or complete signal loss.
- Metal Spatter & Molten Splatter: The welding arc violently ejects droplets of molten metal. These droplets can travel surprisingly far, coating sensor faces (sensing surfaces), embedding themselves in housing seams, or causing short circuits on exposed connections. Over time, this accumulation physically blinds the sensor or damages it.
- Intense Heat Proximity: While not always in direct contact with the weld pool, sensors near welding operations face significant radiated heat and conducted heat from mounting structures. Temperatures exceeding standard sensor ratings can degrade internal components and plastics.
- Mechanical Shock and Vibration: Robotic welding arms move with significant force and speed. Heavy fixtures clang into place. This constant jarring can loosen internal components, break solder joints, or damage the sensitive oscillator circuits within proximity sensors.
- Coolant, Cleaning Agents, and Grinding Dust: Post-weld processes often involve coolants, aggressive cleaning chemicals, and metal grinding dust. These substances can be corrosive or abrasive, attacking sensor housings and seals over time.
Standard inductive sensors, designed for cleaner, less electrically noisy environments, simply lack the robust defenses needed to withstand this multi-pronged assault consistently. Their failure translates directly into production stoppages, scrap parts, and maintenance headaches.
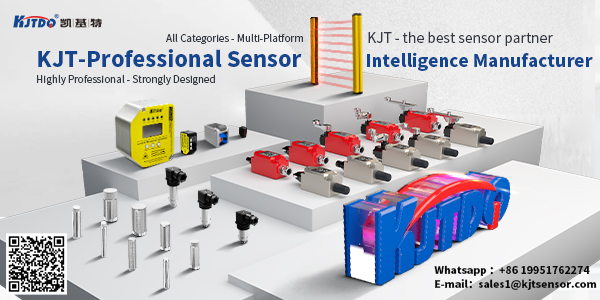
Engineering Resilience: How Weld Immune Sensors Fight Back
Weld immune proximity sensors are not merely minor upgrades; they are built from the ground up, or significantly reinforced, to defy these harsh conditions through sophisticated design and rugged construction:
- Advanced Shielding & EMI Immunity: This is the cornerstone. Manufacturers employ multiple layers of defense:
- Potting: Encapsulating the internal electronics in a specialized resin or epoxy compound shields them physically and electrically from EMI penetration.
- Ferrite Cores: Strategically placed ferrite components absorb and suppress high-frequency electromagnetic noise before it can disrupt the sensitive oscillation circuitry.
- Optimized Circuit Design: Electronic components and circuit board layouts are specifically chosen and arranged to minimize susceptibility to induced currents and voltage spikes. This often includes sophisticated filtering and signal processing algorithms capable of distinguishing the true target signal from background noise. Phase detection technology is also frequently employed, analyzing the phase shift caused by a target rather than just amplitude changes, offering superior noise rejection.
- Robust Physical Armor: The external housing is a fortress:
- High-Temperature Resistant Materials: Housings made from specialized thermoplastics (like PPS) or stainless steel withstand proximity to weld heat without deformation or melting. Viton seals maintain integrity.
- Spatter-Resistant Coatings: Special non-stick coatings (often PTFE-based like Teflon) are applied to the sensor face. Molten spatter beads up and rolls off, preventing adhesion and buildup that would block the sensing field. Stainless steel armored fronts provide an extra sacrificial layer.
- Exceptional Sealing: IP67 and IP69K ratings are commonplace, ensuring total resistance against high-pressure washdowns, coolants, oils, and dust ingress. Multi-lip seals and precision machining keep contaminants out.
- Vibration Resistance: Internal components are securely mounted, often with additional shock-absorbing features or ruggedized connectors, to endure the relentless shaking of an active production line.
- Extended Sensing Ranges: Recognizing that mounting a sensor further away from the worst of the heat and spatter zone is often the safest strategy, weld immune sensors frequently offer sensing distances substantially beyond those of standard sensors in the same form factor.
Where Immunity is Imperative: Key Applications
The value proposition of Сварочный датчик приближения иммунитета shines brightest in specific demanding scenarios:
- Robotic Welding Cells: Detecting fixture clamps, part presence/position near the welding torch, or confirming electrode position on weld guns. Reliable signal integrity amidst intense EMI is non-negotiable for cycle time and quality.
- Resistance Welding Machines (Spot/Projection Welding): Monitoring electrode wear (detecting when the electrode retracts fully), verifying part nesting in fixtures, or confirming weld gun open/close status. Extreme EMI from the high welding currents makes immunity essential.
- Heavy Fabrication & Structural Steel Welding: Tracking part flow on conveyors near large-scale welding operations, monitoring manipulator positions, or confirming jig locations. Spatter and physical abuse are major factors.
- High-Pressure Weld Washdown Areas: Foundries or facilities requiring frequent cleaning after welding operations demand sensors that can handle both the welding environment and subsequent aggressive cleaning.
- Automotive Body-in-White (BIW) Lines: The epitome of robotic welding intensity. Thousands of spot welds per car body generate enormous EMI fields. Sensors for part verification, clamp detection, and robot position feedback in these lines must be weld immune to ensure uninterrupted, high-volume production.
Beyond Avoiding Failure: The Tangible Benefits
Investing in weld immune sensors delivers measurable operational advantages that extend far beyond just preventing a sensor failure:
- Dramatically Reduced Downtime: Eliminating false trips and premature sensor failures keeps lines running smoothly, maximizing Overall Equipment Effectiveness (OEE).
- Lower Maintenance Costs: Fewer replacements, less cleaning required for spatter-clogged sensors, and reduced troubleshooting time translate into significant savings.
- Enhanced Process Reliability & Quality: Consistent, accurate sensing signals ensure fixtures clamp correctly, parts are positioned accurately before welding, and processes trigger only when they should, leading to fewer defects.
- Improved Worker Safety: Reliable detection of machine states (like clamp positions or robot clearances) is crucial for safeguarding personnel working around automated welding equipment.
- Longer Service Life: The rugged construction inherently withstands the environment longer than standard sensors, offering a better return on investment.
Choosing Your Shield: Key Selection Criteria
Not all weld immune sensors are created equal. Careful selection is vital:
- Required Immunity Level: Assess the severity of the EMI, spatter intensity, heat levels, and potential chemical exposure.
- Sensing Distance & Range: Ensure the sensor provides adequate range for your mounting constraints.
- Output Type & Electrical Connection: PNP/NPN, NO/NC, cable or connector style (M8/M